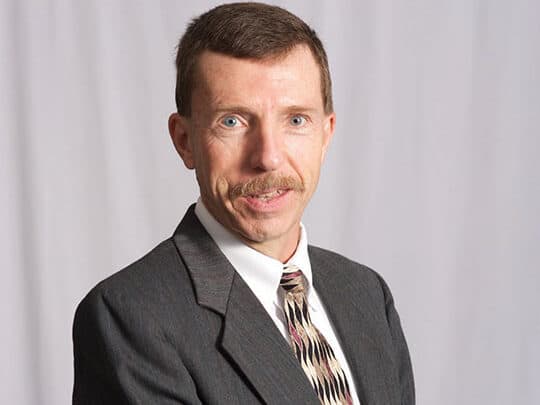
By Michael Culbreth, Loss Control Services Consultant,
Pennsylvania Lumbermens Mutual Insurance Company
Like many businesses in the lumber industry, sawmills require heavy-duty machinery, specialized equipment and extensive electrical systems for daily operations. Using this type of equipment on a day-to-day basis opens the door for accidents leading to employee injury and catastrophic fires. However, with the right safety measures in place sawmill managers can mitigate these risks and address key safety areas to keep their businesses running smoothly.
General Housekeeping
The first step for any sawmill manager looking to protect their business, particularly sawmills and pallet manufacturers, is creating a solid housekeeping program to ensure that sawdust, wood chips and bark that have built up during the day are safely removed from the building at the end of each workday. A strong housekeeping plan will be written down and be a part of regular training so that every employee knows their responsibilities and will be held accountable for their role in the program.
The sawmill basic cleanup procedure should be followed daily along with a more comprehensive cleanup performed at the end of every week. Materials that can build up, if left unchecked, become more combustible with time and create a severe fire hazard.
Automatic collection and conveyor systems capture much of the wood refuse materials and transport them to an outside trailer or dust bin.
The housekeeping program should include removing dust buildup in corners, along walls and under machinery as well. Approved and listed vacuum systems suitable for combustible dust applications are ideal for periodically cleaning overhead dust buildup, but some sawmill managers may conduct an air pressure blowdown. If this is the case, ensure all ignition sources in the facility are off, doors are open for ventilation purposes and reduce air pressure to less than 15 pounds per square inch (psi).
Once combustible materials like sawdust, bark and wood chips have been removed, bulk piles of these materials should be stored at least 100 feet away from the building. Sawdust, chips and bark are commonly hauled away by truck for use by others, including as boiler fuel or landscaping purposes.
Employee training and ongoing attention to housekeeping are the key to preventing dangerous buildup that could put everyone in the facility, and even neighboring areas, at risk.
Hot Work, Electrical and Maintenance
Hot work activity such as welding, torch cutting and grinding, present an ignition source. Obviously, this is an important fire safety issue to address for any lumber business, especially sawmills and pallet manufacturers. In fact, welding is often the leading cause of sawmill fires each year. OSHA offers general safety and health tips for hot work. While these are helpful, having a written hot work permit program is necessary to create a system of checks and balances between the welder, fire watcher and Permit Authorizing Individual (PAI).
Any welding or other hot work activity requires a fire watcher, a designated individual responsible for paying close attention and extinguishing any smoldering condition. Even after the job is complete, a fire watcher should remain vigilant at least two hours afterward – preferably longer if possible – conducting visual inspections and wetting down the surrounding area.
Additionally, hydraulic equipment near welding activity should have a fire blanket covering hydraulics systems, preventing sparks from reaching these areas and any other combustible materials located within 35-feet of the hot work area. Fire safety precautions outlined on the written hot work permit checklist should be closely and consistently followed.
For electrical and machinery maintenance, ensure all work is being done by experienced and qualified/licensed personnel. At least twice per year, open the electric panel boxes and remove any sawdust that has built up inside. An electrical infrared thermography scan should also be conducted on a yearly basis. This has become increasingly popular over recent years, as loss control representatives are being certified to use infrared cameras that show hotspots inside the panel boxes.
These overheating conditions are not visible to the human eye and often result from loose electrical connections. The infrared scan can also include checking motors and bearings for overheating conditions. Repairs should be completed on a timely basis for each overheating condition identified during the scan. Infrared thermography is beneficial for fire safety reasons, extends the lifespan of motors and equipment and saves costs by avoiding unnecessary energy consumption.
Preventative maintenance schedules for sawmills are vital to fire safety and profitability. Good maintenance keeps machinery in proper working condition and makes it less likely to cause a fire. It also lessens breakdowns and reduces machinery downtime that can bring business to a halt. Sawmill managers should create checklists to help track every step of the business’s preventative maintenance program. As with all operations within a sawmill, each employee responsible for maintenance should be well trained and qualified to handle the task at hand.
Having a Backup Plan
When it comes to protecting employees and dealing with fire hazards, it’s always better to be safe than sorry. Sawmill managers should identify which first response fire department will be at their sawmill and work with the local fire department to create an emergency fire plan. As part of this plan, request that they visit the facility on a yearly basis, mapping out each building and its occupancy, the location of fire hydrants or other water sources, fuel tank and propane locations, electrical disconnect locations and identifying the safest escape route.
There are numerous steps that should be taken to address general safety issues for sawmills. Rather than go it alone, sawmill managers should work with a specialized loss control representative who is familiar with the specific hazards of the lumber business and can help ensure they’re doing everything possible to keep their employees and business safe.
Michael Culbreth, Pennsylvania Lumbermens Mutual Insurance Company, is a loss control services consultant based in Inman, South Carolina who joined PLM in 2002. He protects businesses in territories including North Carolina and South Carolina. Michael can be reached at mculbreth@plmins.com or by phone at (267) 825-9146.