Bingaman & Son Lumber Inc. Introduces New President
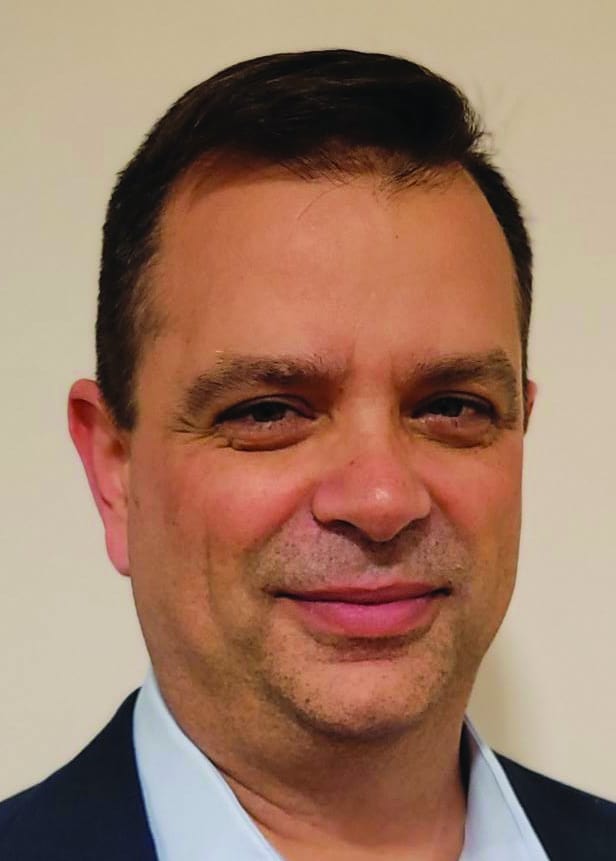
Chris Bingaman announced that Scott Hurst assumed the role of president of Bingaman & Son Lumber Inc. on January 1st, 2024. Hurst joined Bingaman as accounting manager in 1994 and served as CFO since 2008. When making the announcement Chris stated, “I am confident Scott is dedicated to maintaining our core values and possesses the skills we need for our future.” Chris will remain as CEO.
Chris added, “One of our company’s core values is stewardship. We describe it as, managing our relationships and resources as a trust given from God, which inspires our vision for the future!” This value applies to the stewardship of the organization.
In 2017 Bingaman created an Executive Team to plan corporate leadership transition that would bring continuity to the values and the talent that the company needed for a successful future. They are making this change now to demonstrate an intentional transition plan to their employees and business partners. Bingaman & Son Lumber Inc. headquartered in Kreamer, PA is an ESOP company with five locations in Pennsylvania.
For more information, visit www.bingamanlumber.com.
Koppers Names James A. Sullivan President And Chief Operating Officer
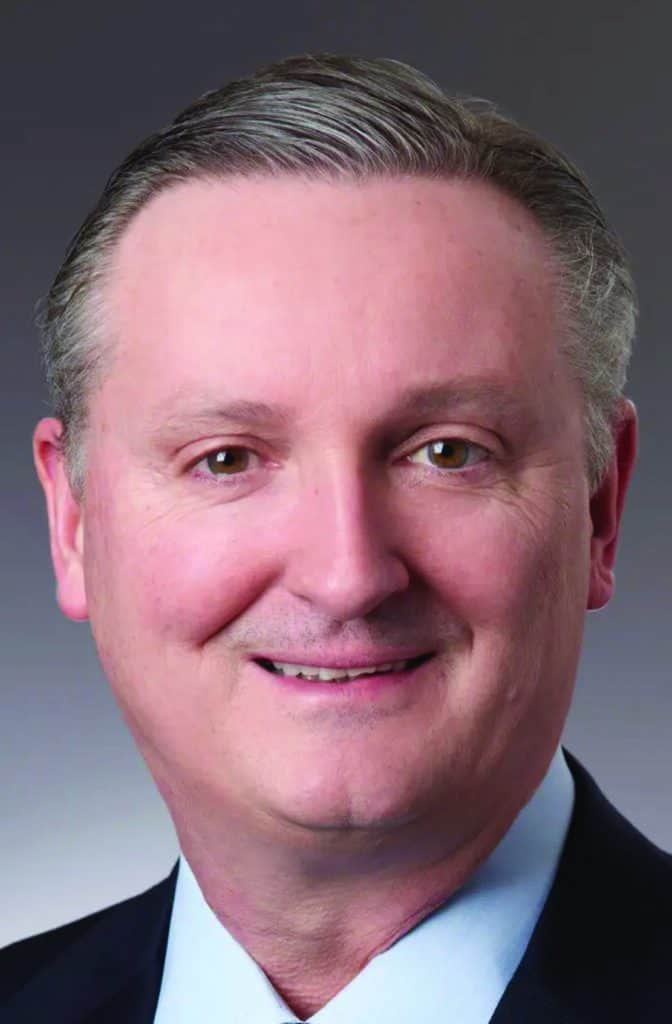
Koppers Holdings Inc. announced the election of James A. Sullivan as president and chief operating officer, effective January 1, 2024. Sullivan has been Executive Vice President and Chief Operating Officer since January 2020. Leroy M. Ball will continue to serve as Chief Executive Officer of Koppers.
As president, Sullivan will have a bigger role in the development of Koppers 2030 strategy, which is expected to build upon the company’s 2025 Expand and Optimize strategy that has consistently produced improved safety performance, steady progress in sustainability, and record financial results. Ball will continue to apply his leadership to drive shareholder value, which includes setting the company’s corporate strategy, advancing its people-first culture and building key stakeholder relationships.
With over 20 years of direct industry experience, Sullivan joined Koppers in June 2013 as Vice President of Business Development before advancing into various roles of increasing responsibility, culminating in his appointment to Executive Vice President and Chief Operating Officer in January 2020.
Commenting on the change, Ball said, “Jim has contributed so much to the evolution of Koppers since he joined the company over 10 years ago. From spearheading the restructuring and resurgence of the Carbon Materials and Chemicals business, to breaking down business unit silos by uniting operational leadership, and advancing our 2025 Expand and Optimize strategic plan, he has driven a culture of performance. I am very happy to recognize Jim’s accomplishments in this way while also keeping him engaged in the next phase of Koppers evolution.”
Sullivan added, “It is my honor to accept this new responsibility as President of Koppers. I am proud of our team around the world, who has demonstrated the power of working together to drive results, improve safety, lead in sustainability, and promote our values of People, Planet, and Performance. I look forward to continuing to grow our business under Leroy’s leadership.”
Koppers, with corporate headquarters in Pittsburgh, PA, is an integrated global provider of treated wood products, wood treatment chemicals, and carbon compounds. Their products and services are used in a variety of niche applications in a diverse range of end markets, including the railroad, specialty chemical, utility, residential lumber, agriculture, aluminum, steel, rubber and construction industries. They serve their customers through a comprehensive global manufacturing and distribution network, with facilities located in North America, South America, Australasia, and Europe.
For more information, visit www.koppers.com.
Carbotech Group Announces Expansion In USA
Carbotech Group, headquartered in Plessisville, QC, continues to expand in the United States with the acquisition of a 14,000-square-foot plant in Roebuck, SC. In perfect synergy with its growth strategy, the company planned to start operations at its new facilities in mid-January 2024, primarily to serve customers in the southern United States.
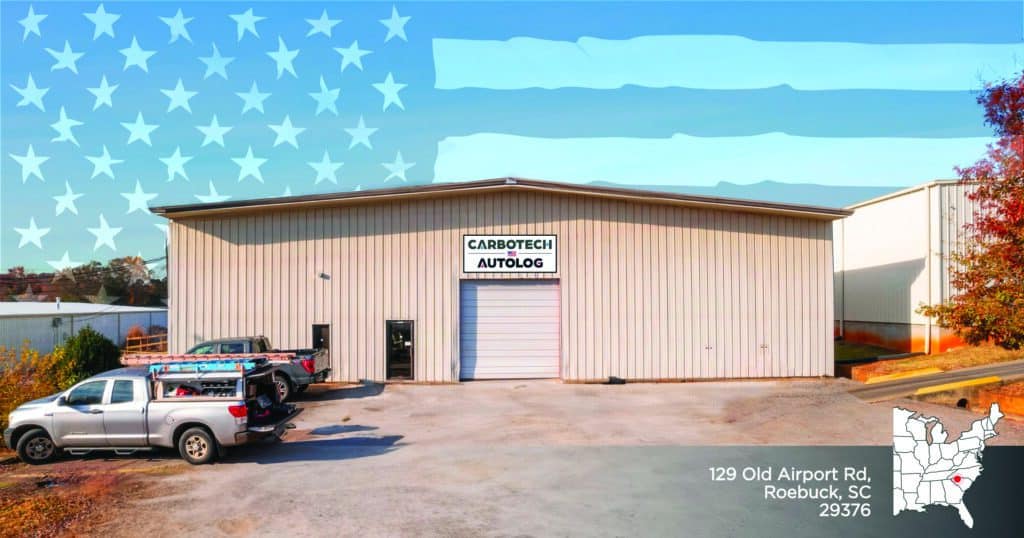
Carbotech Group’s new location in Roebuck, SC.
With this acquisition, Carbotech Group is strengthening its ability to quickly meet the needs of its American customers. A new local team of mechanical and automation technicians will also be created. Together with the plant, this will improve the manufacturing of Carbotech equipment and enable the storage of spare parts for Autolog and Carbotech equipment.
The plant is strategically located in the heart of the American South. It will also be home to a training center to develop expertise on Carbotech and Autolog equipment so that it can reach its fullest potential.
Carbotech Group also announced the appointment of Jon Comber as Managing Director of U.S. Operations. His extensive knowledge of Carbotech and Autolog products, as well as his impressive professional background in the sawmilling industry (including experience as a plant manager), make him the ideal person for the role, according to a company spokesperson.
Carbotech Group was born of Carbotech’s acquisition of Autolog. Together, the two specialists in their fields boast over 70 years of experience in comprehensive sawmill solutions for the wood industry.
For more information, visit www.carbotech.ca.
Cleereman Industries Installs New Mazak Machines
Cleereman Industries, headquartered in Newald, WI, recently installed a Mazak C&C-Vertical Mill with four axes and a Mazak CNC Turning center with live tooling in their Edger Division, located in Crandon, WI, which is the machining center for the company. “We have several C&C machines in this facility for doing a lot of our machining. We machine our band mills, log turner bars and edgers, along with a wide variety of other components for our sawmill equipment lines,” said Paul Cleereman, Vice President of Cleereman Industries. Currently the company is building one complete edger a month along with other sawmill equipment.
Paul noted that the Mazak team spent a week training the Cleereman machinists and that both machines are in full production after being installed at the beginning of January.
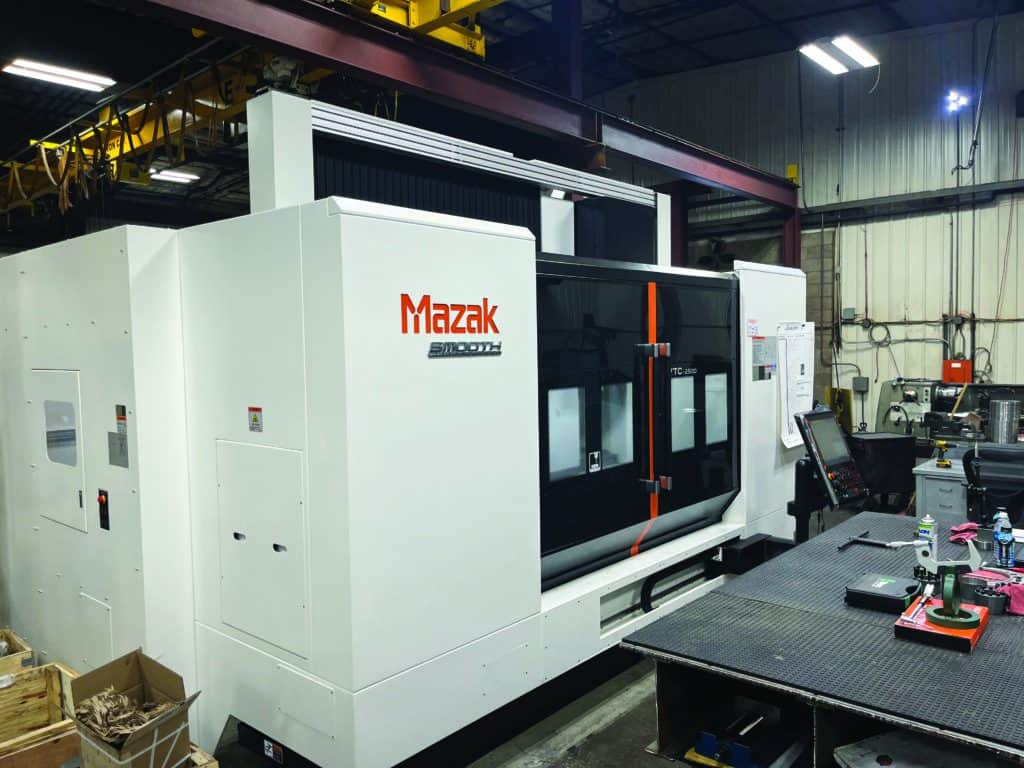
Mazak CNC-Vertical Mill with live tooling.
“This was a large capital investment by our company, and it will increase production and allow Cleereman to improve our delivery and lead times on equipment. These two machines open a lot of new possibilities of what Cleereman can do in house. In the past on some of our new equipment lines we had to send different items out for machining but now we can do everything in house. This is huge for us because we control turnaround times where in the past we were at the mercy of someone else’s schedule,” Paul said.
The new machine centers will allow Cleereman to be more efficient and increase their production. This will not only allow them to control rising costs and long lead-times in the supply chain, but it will also allow them to manufacture at a lower cost, passing the savings on to their customers, according to Paul.
Cleereman Industries has a major expansion planned in 2024 and is adding 15,000 square feet of manufacturing. The new facility will allow the company to increase production to keep up with the demand for their different equipment lines.
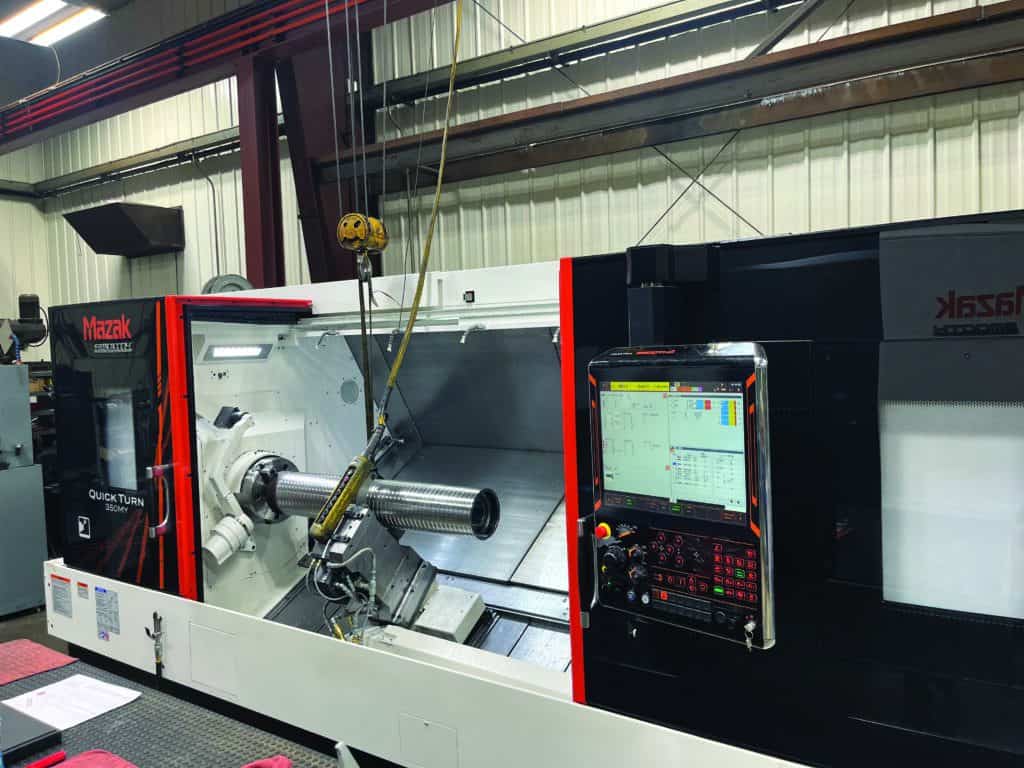
Mazak CNC turning center with live tooling and a Cleereman edger roll being machined.
“With the demand for our turnkey sawmill solutions and different equipment lines the expansion allows us to increase production. Cleereman Industries offers complete turnkey sawmills, and this has become something that we are doing more and more of. Over the last several years we have been building more complete sawmills. Cleereman takes care of everything from engineering to electrical drawings and all the equipment from the Debarker through the trimmer and everything in-between. This is all done as an engineered solution which saves time and money for the sawmill customers,” Paul added.
Cleereman Industries is a family-owned business located in Wisconsin and employs over 50 employees. Cleereman Industries president is Fran Cleereman who has over 60 years at Cleereman Industries. Fran’s beliefs have always been customer service and quality equipment at a fair price.
For more information, visit www.cleereman.com.
Nicholson Manufacturing: Innovating The Forestry Industry With Additive Manufacturing
Nicholson Manufacturing Ltd., a name synonymous with innovation in the forestry industry, is once again at the forefront of technological advancement. Known for revolutionizing the industry in the 1940s with the introduction of lathe and rosser-head-style debarkers, and later, in 1951, with the first whole-log mechanical ring-type debarker, Nicholson has continuously set the benchmark for efficiency and effectiveness. Today, from their base in Sidney, British Columbia, Canada, they design and build ring debarkers that serve lumber facilities worldwide, boasting processing speeds exceeding 650 feet per minute.
Building on their legacy of pioneering progress, Nicholson Manufacturing is now embracing additive manufacturing, a cutting-edge form of 3D printing, to enhance their wear parts, starting with the innovative MLX™ knife tips. This technological leap marks a significant step forward in customizing products for specific applications, offering a blend of precision and versatility previously unattainable.
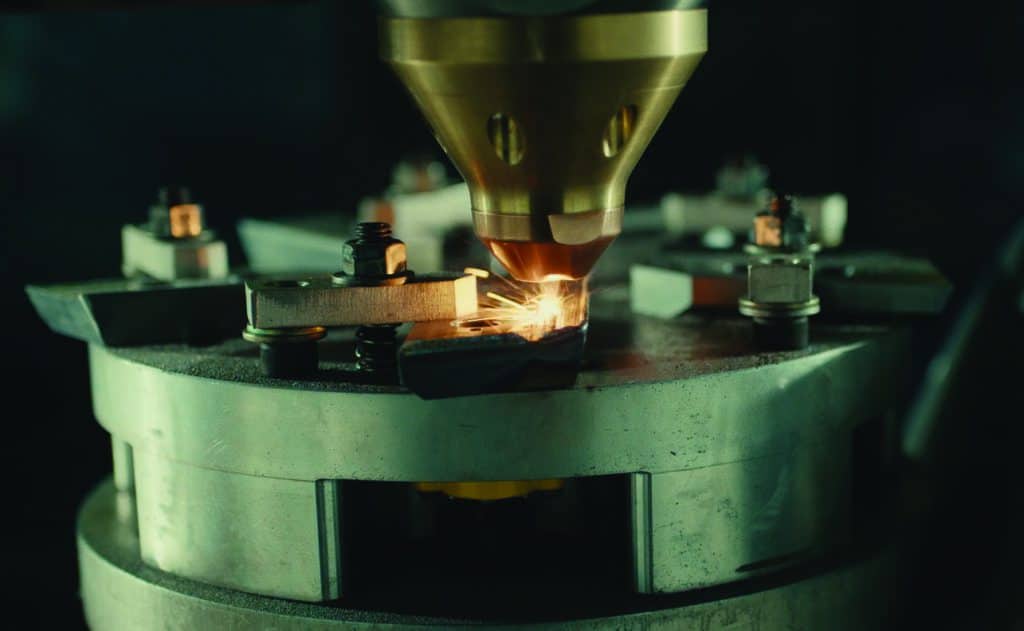
Nicholson Manufacturing’s additive manufacturing head.
The success of their field-tested debarking knife tips has paved the way for further advancements. Nicholson plans to extend this technology to other critical wear parts. Their goal is simple yet ambitious: to reimagine every part susceptible to wear and tear, ensuring enhanced durability and efficiency.
This move towards additive manufacturing is not just a technological leap; it represents Nicholson’s commitment to sustainability and cost-effectiveness. The benefits of this approach are multifaceted:
Increased Wear Life: The new parts promise extended durability, although the exact lifespan varies by mill.
Impact Resistance: Enhanced resistance to carbide breakage from unforeseen elements like rocks.
Reduced Maintenance: The frequency of tip changes on debarkers is significantly lowered.
Easier Recycling: Aligning with Environmental, Social, and Governance (ESG) standards, the new parts are designed to be more recyclable.
The team at Nicholson Manufacturing, which, according to a company statement, is always quick to spot the ‘forest between the trees,’ demonstrates an ability to integrate cutting-edge technology into their proven models. By adopting additive manufacturing, they not only uphold their reputation as industry leaders but also underscore their commitment to innovation, sustainability, and efficiency, noted a company representative.
In a world where adaptation is key, Nicholson Manufacturing stands tall, continuing to shape the future of the forestry industry, one groundbreaking innovation at a time.
For more information, visit www.nicholsonmfg.com.
TS Manufacturing Acquires Remaining Shares In A&E
TS Manufacturing, located in Lindsay, ON, is proud to announce the acquisition of the remaining shares in A&E.
As TS enters this new phase with the acquisition of A&E, they are eager to share key updates and reassure their valued customers and partners about the future of this collaboration.
According to a company representative, they are proud to announce the purchase of the remaining shares from Brian Smith, Managing Director at A&E. Smith, and the dedicated teams at A&E, both in New Zealand and the USA, have forged deep connections with their customers, developing products that are integral to the industry.
These relationships and innovations are the bedrock of A&E’s success and will continue to be a focal point for TS as they move forward.
The commitment that TS has to continuing to service their customers under their existing brands remains unwavering. The company wants to assure all their clients that the high standards of service and product quality will continue as they uphold the unique strengths of both TS Manufacturing and A&E operating independently.
This acquisition symbolizes not just organizational growth but a strengthening of their shared dedication to innovation and excellence in customer service.
TS is optimistic about the future and the myriad of opportunities this partnership will continue to bring as they expand their offerings with the enhanced breadth of knowledge and expertise available in a team of nearly 150 strong capable personnel.
TS Manufacturing offers a complete line of machinery, controls and software to fit your mill. For more information on their complete line of sawmill and planer mill offerings, please email them at sales@tsman.com, call at (705) 324-3762 or visit www.tsman.com.
Continental Underwriters Inc. Promotes Andrea Green
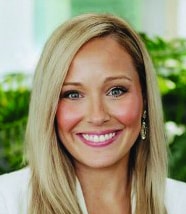
Continental Underwriters Inc., located in Richmond, VA, recently promoted Andrea Green to Risk Assessment and Claims Director of Operations. In this new role Green will oversee the day-to-day operations of the Risk Assessment and Claims Division by evaluating and implementing processes throughout the division, while coordinating with other divisions throughout Continental Underwriters to develop and implement processes that connect all of the company’s divisions and to help their teams operate more efficiently. She also manages and oversees all of the claims for Continental Underwriters book of business and helps in the recruiting, hiring and onboarding process for her division.
Continental Underwriters Inc. is a Managing General Agency (MGA) and wholesaler providing the forest products industry in North America with a broad range of insurance and risk management solutions designed to safeguard against losses and protect the value of the businesses they insure. Their programs offer a portfolio of insurance coverages for the building materials, lumber, forest products and woodworking industries.
Green’s first job in the forest products industry was when she was hired by Continental Underwriters in 2019. When she first joined the company, she brought over nine years of valuable experience in the insurance industry, primarily in claims handling. A company representative said that Green has proven to be an excellent addition to their team, as she possesses a strong passion for assisting others and is driven to develop her career further by deepening her knowledge of the company’s forest products niche. She is dedicated to providing top-notch service to Continental Underwriters’ clients, agents and carrier partners.
Green has been married to Bobby Green since 2022 and enjoys spending time with family and friends, as well as visiting local wineries and traveling.
Continental Underwriters is a member of Lake States Lumber Association, Indiana Hardwood Lumbermen’s Association, Appalachian Hardwood Manufacturers Inc., National Wooden Pallet & Container Association, Hardwood Manufacturers Association, North Carolina Forestry Association, Western Wood Products Association, Mississippi Lumber Manufacturers Association, Southeastern Lumber Manufacturers Association Inc., Great Lakes Timber Association, National Hardwood Lumber Association, Virginia Forestry Association, West Virginia Forestry Association and Wood Products Manufacturers Association.
For more information, visit www.contund.com.
TMX Shipping Co. Inc. Welcomes Ryan Todd
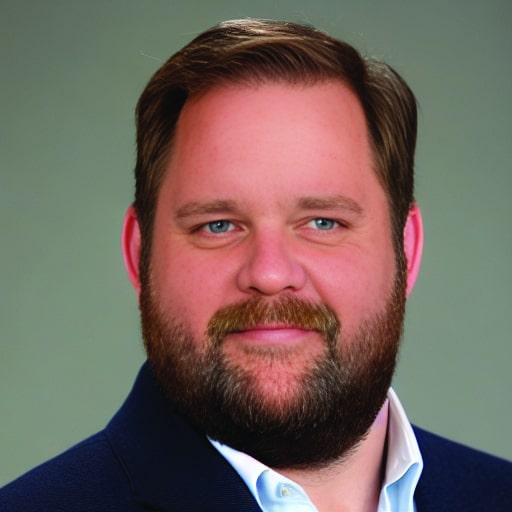
Ryan Todd recently joined TMX Shipping, located in Morehead City, NC. Todd came to TMX from the Ocean Carrier segment of the Global Transportation Industry. Todd was previously with Mediterranean Shipping Company (MSC) for 16 years where he worked in various roles including customer service, line management, special projects teams, business transformation teams and led the Customer Experience division.
Thrilled to leverage his extensive knowledge, Todd envisions a future at TMX marked by a personalized and seamless shipping experience, considering it the epitome of successful business transactions in the industry. He is excited to add innovative value to TMX’s customer base and actively contribute to the expansion of product offerings into new market segments. This strategic move positions Todd as a key player in TMX Shipping’s pursuit of excellence and the company is thrilled to have him join the team.
For more information, visit www.tmxship.com.
Bipartisan Legislation Introduced To Promote Domestic Hardwood Products
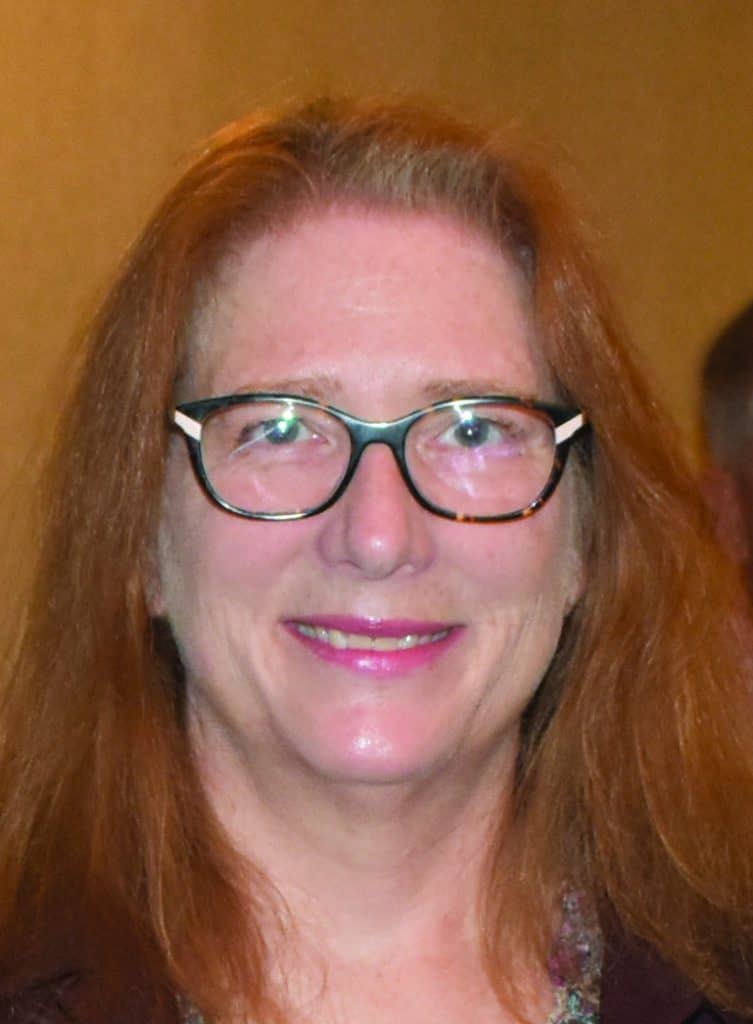
Congressman Tom Tiffany (WI-07) and Congresswoman Ann Kuster (NH-02) recently introduced bipartisan legislation to support domestic Hardwood products. H.R. 6880, the Hardwood Products Access and Development Program Act, permits the Secretary of Agriculture to authorize grants that bolster domestic industry efforts and research that directly supports end-user information on the benefits of Hardwood products.
This will allow various non-profits, universities and other eligible applicants to research the low carbon footprint and sustainability of domestically produced Hardwood products to educate the public on the benefits of these products.
“Wisconsin is home to numerous Hardwood manufacturers, and this important legislation will inform consumers on the sustainability of domestically produced Hardwood products,” said Congressman Tiffany. “I will continue to promote Made in America wood products that benefit our environment and economy.”
“New Hampshire’s Hardwood foresters generate some of the highest-quality products in the world – we need to ensure they have the support to continue serving their customers,” said Congresswoman Kuster. “American-grown Hardwood offers an incredible opportunity to create more sustainable, durable products in countless industries right here at home. I’m proud to help introduce this legislation today to support our wood producers and strengthen our economy and supply chains.”
“The U.S. Hardwood industry is a multi-billion-dollar industry supporting over 1.8 million jobs, mostly in rural, underserved areas. Although wood products are widely recognized as sustainably produced and have significant carbon storage capacity, public awareness and recognition of these qualities is limited. The domestic industry and domestically produced products, including flooring, cabinetry, doors, mouldings, railway ties, pallets and other Hardwood building and infrastructure products will benefit greatly from the much needed research and education dollars through the enactment of the Hardwood Products Access and Development Program Act. This essential funding will help sustain and grow the Hardwood companies and their employees in rural, agricultural communities across the country,” said Dana Lee Cole, Executive Director of the Hardwood Federation.
“Consumers around the world express a strong preference for U.S. Hardwood home finishings and furnishings but are often confused by the mixed messages they receive from non-sustainable competitor products. The Hardwood Products Access and Development Program Act will put important data into the hands of decision makers and allow them to make the best choices for their homes and the environment,” said Troy Brown, President of Kretz Lumber in Antigo, WI.
“The U.S. Hardwood industry is proud of the products we produce and the forest, carbon reduction and storage as well as home health benefits that are realized from modern forest management practices that supply the raw materials to our mills. The Hardwood Products Access and Development Program Act will facilitate the development and sharing the science-based data that supports our claims as one of the most environmentally friendly building materials available,” said Jameson French, President and CEO, Northland Forest Products, Kingston, NH.
For more information, visit www.hardwoodfederation.com.
Dovetail Partners Commissioned By AHEC To Provide Risk Assessments For 33 States
The American Hardwood Export Council (AHEC) has commissioned Dovetail Partners to complete independent jurisdictional risk assessments covering Hardwood production in each of the 33 U.S. states identified as significant producers of Hardwoods.
The results of the project will provide public access to endorsed statewide risk assessments to “ensure equitable access to international markets for U.S. producers and to serve as the backbone of due diligence systems that are increasingly required for the trade of forest products.”
Following passage of the European Union Deforestation Regulation (EUDR) in 2023, AHEC adopted an amended strategy to implement a new form of verification to demonstrate that U.S. Hardwood is legal and deforestation-free.
“The first priority,” said Michael Snow, executive director of AHEC, “is to implement a set of procedures that will enable U.S. Hardwood suppliers to address the EUDR requirements, including investigating and providing an independent determination of the risk of illegal harvesting in accordance with the EUDR definitions.”
The EUDR went into force in June 2023 and provides companies trading wood products an 18-month transition period to adopt the new requirements.
The scope of the project includes the 33 U.S. states identified by U.S. Forest Inventory Analysis (FIA) data as producing substantial Hardwood volumes. Roughly in order of volume produced these states include Tennessee, North Carolina, Virginia, Pennsylvania, Kentucky, Alabama, New York, Maine, West Virginia, Michigan, Ohio, Georgia, Mississippi, Arkansas, South Carolina, Missouri, Wisconsin, Louisiana, Texas, Indiana, Washington, Oregon, Minnesota, Illinois, Maryland, New Hampshire, California, Vermont, Iowa, Florida, Oklahoma, Massachusetts and Delaware.
For more information, contact Dovetail Partners, info@dovetailinc.org, 612-333-0430 or visit www.dovetailinc.org.
Wood Flooring Manufacturers Cautiously Optimistic
Despite a sluggish second half, U.S. floor coverings manufacturer sales (shipments minus exports plus imports) rose 7.5 percent in 2022 to $37.6 billion, according to Catalina Research.
At $1.2 billion, laminate flooring accounted for 3.2 percent of the overall market and Hardwood flooring, at $4.56 billion, accounted for 12.1 percent.
In a separate survey of the Hardwood sector, manufacturer members of the National Wood Flooring Association (NWFA) said they remain “cautiously optimistic” heading into 2024 despite the continuing shadow of rising interest rates and inflation.
According to the annual NWFA Industry Outlook survey, 21 percent of respondents said they expect sales to be up “significantly.” Forty one percent expect sales to be up “somewhat” and 24 percent believe sales will be “about the same.” Only 4 percent forecasted a “slight downturn” and 10 percent expected a drop in sales of 8 percent or higher.
When it comes to styles and overall type, the 2024 outlook calls for an increased demand for natural wood colors and matte sheen finishes, wider planks, longer boards, increased use of engineered wood and factory-finished products.
•2022 worldwide sales by members of the European Producers of Laminate Flooring were 367.2 million m², down 24 percent from 2021, “mainly due to the war in Ukraine.” Western Europe accounted for 49 percent with sales of 179.0 million m² sold, while North America was at 37.3 million m².
•Research and Markets projects the global wood and laminate flooring market to reach $101.31 billion USD by 2030, growing at 5.8 percent compound annual growth rate (CAGR), from $64.72 billion in 2022.
• Although roughly one-third of consumers “shopped” online, according to research by TraQline (Home Improvement Research Institute), 81 percent of U.S. consumers purchased their flooring in-store, 9 percent online and 10 percent “other.” Similarly, in Canada, 82 percent of purchases were in-store, 9 percent online and 9 percent “other.”
More data on North American woodworking and the specific wood product market segments can be found at www.woodworkingdigital.com or www.woodworkingnetwork.com.