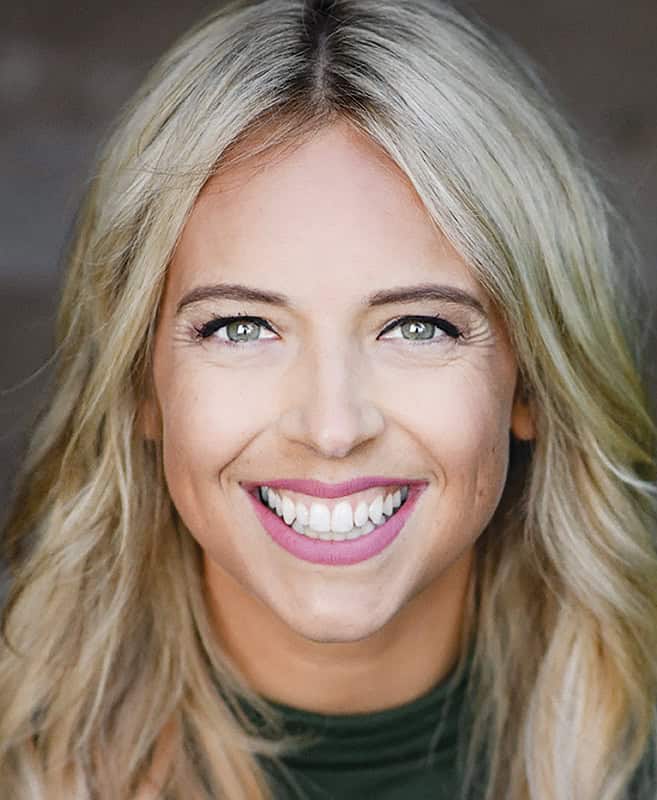
Patrick Lumber Company Names Natalie Heacock as New President
The Patrick Lumber Company Board of Directors recently announced the appointment of Natalie Heacock as the new President. Heacock brings a wealth of experience and a proven track record of building strong teams within both Patrick’s trading and finance groups. Her dedication, expertise and visionary leadership make her an excellent choice to guide the company through its next phase of growth and success.
Heacock succeeds Patrick Burns, who will continue to play an active role in trading. With the unanimous support of the Board of Directors, Heacock is well positioned to elevate the organization’s performance and achieve our strategic objectives.
Heacock has been with Patrick Lumber Company since May 2014. As CFO since 2021, Heacock has fine-tuned financial processes and ensured smooth operations across the finance, accounting, IT and HR departments, according to a company representative. Additionally, she serves on the Board of Directors, contributing deeply to the company’s strategic direction.
Heacock holds an MBA from Willamette University, a BS in Finance from the University of Portland and is a Certified Public Accountant. She has been recognized with numerous awards, including being named to the Portland Business Journal’s 40 under 40 and the North American Wholesale Lumber Association’s (NAWLA) 40 under 40. Her background equips her to lead with a focus on unity and excellence and she is passionate about fostering a culture of leadership and high performance.
“We are confident that Natalie’s leadership as President and CFO will drive our company to new heights,” said CEO Dave Halsey. “Her commitment to our core values and her innovative approach will continue to enhance our relationships with customers, suppliers, employees and the communities we serve.”
Learn more at www.patlbr.com or call 503-222-9671.
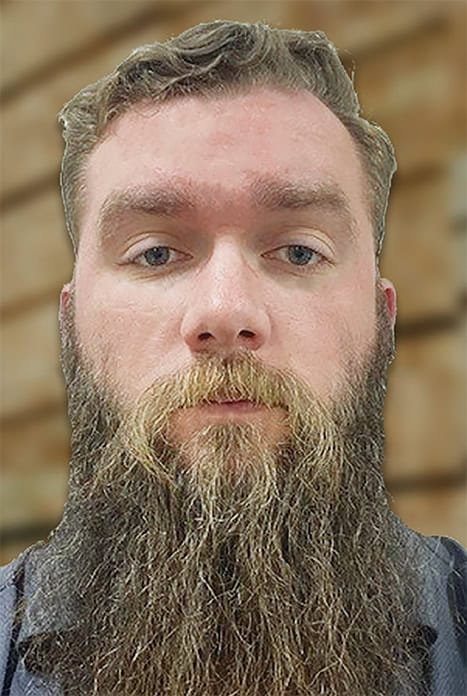
Culpeper Wood Preservers Appoints New Director of Purchasing, Marks Retirement of Longtime Company Leader
Culpeper Wood Preservers, Culpeper, VA, a leading manufacturer of pressure-treated lumber, is promoting from within to fill an important role on its leadership team following the retirement of a longtime employee. Nick Aylor recently assumed the role of director of purchasing. He succeeds Jeff Lineberger, who had held that title at Culpeper for 25 years.
Aylor joined the company in 2021 and had been serving in the role of purchaser prior to this appointment. As the department lead, Aylor will oversee the company’s procurement processes, develop purchasing strategies and manage key supplier relationships. A graduate of James Madison University, Aylor formerly served in a manager role at a farm equipment supply company prior to joining Culpeper.
Lineberger began his career in building materials in 1983, immediately after graduating from the University of North Carolina. He joined Culpeper in 1999.
“Our entire team will miss Jeff, and we wish him and his wife well as they retire to North Carolina. At the same time, we are enthusiastic about our future with Nick. Supported by a seasoned team, he will continue to enhance the strong relationships that Jeff has cultivated over the years,” said Jonathan Jenkins, president of Culpeper Wood Preservers.
Culpeper Wood Preservers is one of the largest producers of pressure treated lumber in the United States. In 1976, Culpeper Wood Preservers started from a single location in Culpeper, VA. Today, the company is a leading manufacturer of pressure-treated products for the residential, commercial, industrial, and marine markets. Culpeper Wood Preservers’ brand-name products are sold exclusively through independent lumber dealers throughout the Mid-Atlantic, Northeast, Midwest and South.
For more information, visit www.culpeperwood.com.
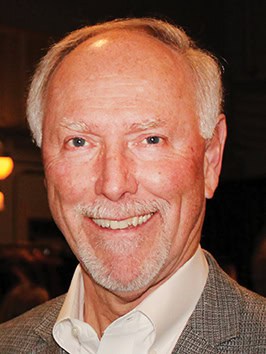
Wildwood Trading Group of Vaagen Bros. Lumber Announces Leadership Transition
Wildwood Trading Group (WTG), located in Tualatin, OR, the trading arm of Vaagen Bros. Lumber, recently announced a significant leadership transition following the retirement of one of its founding partners, Mike Phillips.
Since its inception in September 2018, Wildwood Trading Group has experienced remarkable growth under the leadership of Mike Phillips, Kevin Dodds and Grant Phillips. The company has not only increased its total sales but also established itself as an industry leader, supporting independent sawmills and customers. Key milestones include the addition of new reload locations and the expansion of PET unit saw capacity to multiple locations across the U.S.
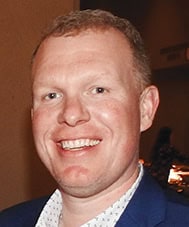
With Mike’s retirement, the company is excited to announce the promotion of Grant and Dodds to co-presidents. Dodds and Grant have been instrumental in driving Wildwood’s success and are well-prepared to lead the company into the future. Their combined expertise and innovative approach will ensure that Wildwood continues to excel and expand its market presence.
Grant and Dodds’ leadership has already resulted in significant achievements, including the enhancement of Wildwood’s sales staff, marketing reach and customer service capabilities. Their vision for the company includes not only maintaining the high standards set by Mike but also introducing new strategies to adapt to the evolving market landscape.
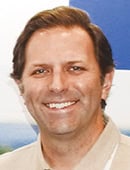
“The promotion of Grant and Kevin to co-presidents marks a new chapter for Wildwood Trading Group,” said Mike. “Their youthful enthusiasm and dynamic leadership will drive the company forward, building on the solid foundation we’ve established over the past five years. I have full confidence in their ability to lead Wildwood to even greater success.”
This transition sets the stage for further organizational developments, with additional promotions and changes to be announced in the near future. The extensive support team in Tualatin, Colville and Portland has been pivotal in creating a profitable and exciting work environment, and this collaborative spirit will continue to thrive under the new leadership.
As Wildwood Trading Group looks to the future, the company remains committed to its core values and mission of providing exceptional marketing services to vendors and customers. The team is poised to build on past successes and explore new opportunities for growth and innovation.
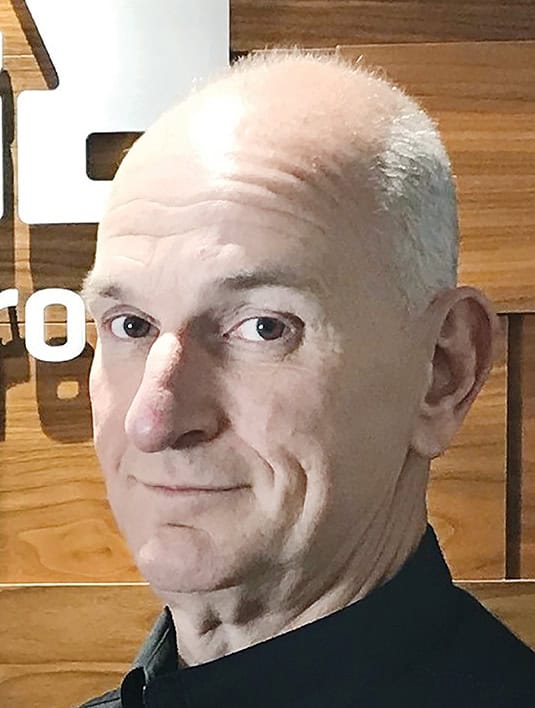
BID Group Partners With Tough By Nature
BID Group is pleased to announce a strategic partnership with Tough By Nature (TBN) to distribute the revolutionary WonderCoat kiln sticks across North America. This collaboration sets a new standard in the lumber industry, providing mill operators with longer-lasting, more durable kiln sticks that enhance efficiency at the stacker and significantly reduce operational costs.
This partnership enhances BID Group’s ability to support its customers with solutions that drive efficiency and reliability. “We are excited about this partnership,” said Simon Potvin, President of Wood Processing at BID Group. “The integration of Tough By Nature Sticks into our product offerings aligns perfectly with our mission to provide innovative and efficient solutions to our clients.”
Jeff Yurk, Managing Partner at Tough By Nature, expressed his enthusiasm for the partnership, stating, “This partnership exemplifies the innovative spirit and commitment to excellence that both companies embody. We are proud to be working with BID Group as they have demonstrated innovation and success throughout the years.”
TBN’s relationship with BID Group is built on mutual respect and a shared vision for the future. The company’s extensive experience in the wood processing industry, combined with TBN’s pioneering product, ensures that customers receive the highest quality and most reliable products on the market.
Since 1924, the privately-owned BID Group has been providing industry-leading solutions for its highly valued customers. As one of the largest integrated suppliers to the wood processing industry, and the North American leader in the field, BID Group, according to a company representative, is its clients’ one-stop source for guaranteed, comprehensive and innovative solutions.
The ability to provide complete, smart connected, turnkey manufacturing facilities that includes engineering, project management, equipment, software, installation, startup and after sales parts and services is the BID Group companies’ strategic value to its customers. The company has offices in 17 locations situated to serve the predominant wood processing regions of North America.
Learn more about BID at www.bidgroup.ca.

MiCROTEC Welcomes Norvin Laudon As New Head Of Sales
Norvin Laudon is the new head of sales at MiCROTEC, in Corvallis, OR. Laudon’s team serves the United States, Canada, Australia and New Zealand markets, offering optimized wood scanning solutions. Laudon has 21 years of wood products industry experience, with beginnings in board scanning and moving into log scanning and optimization.
Laudon has been with MiCROTEC for 16 years, where he was a key developer of the CT Log; using computed tomography technology to provide a complete reconstruction of a logs’ internal features and optimized cutting solutions.
With the new role, Laudon is excited to introduce the industry-changing fingerprint system, MiCROTEC Connect, integrated with CT technology for hardwood and softwood mills across North America. The system offers massive benefits for mill-wide value and recovery optimization.
MiCROTEC is the only company offering scanning and optimization solutions from log to final board, providing innovative scanning solutions focused on recovery and sustainability. MiCROTEC’s customer support is backed by a team of industry experts, including ex-graders, engineers and specialized technicians. The scanning solutions offered by MiCROTEC allows logs to be graded and sorted by quality and optimizes the cutting solution with the highest value in real time. The company’s board scanning technology is well-known in the industry in the Lucidyne and Goldeneye scanners, revolutionizing automated defect detection and grading.
MiCROTEC is a member of the Southeastern Lumber Manufacturers Association, Indiana Hardwood Lumbermen’s Association, Northeastern Lumber Manufacturers Association, Southern Forest Products Association, National Hardwood Lumber Association, Mississippi Lumber Manufacturers Association and the Western Wood Products Association.
For more information on Norvin’s new role or MiCROTEC’s solutions, call 541-753-5111, email norvin.laudon@microtec.us or visit www.microtec.us.
Wholesale Building Products Upgrades with Nyle Dry Kilns
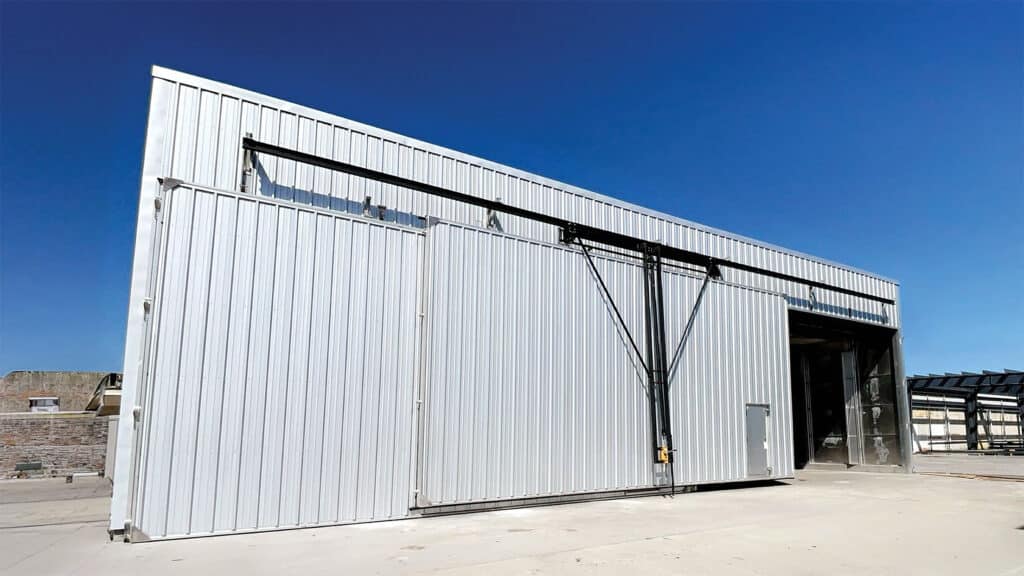
Nyle Dry Kilns, headquartered in Brewer, ME, recently announced the successful installation of two state-of-the-art 65 thousand board feet Gas Kilns at Wholesale Building Products’ Jacksonville, FL, facility. These kilns are designed to optimize the drying process for Southern Yellow Pine, ensuring superior quality and efficiency for Wholesale Building Products.
The kilns feature cutting-edge technology, including indirect-fired gas heaters and high-efficiency heat recovery vents. These systems are engineered to deliver precise temperature control, energy efficiency and consistent performance. The advanced control systems allow for detailed data logging and remote management, providing operators with comprehensive insights into the drying process. According to a company representative, this installation not only enhances Wholesale Building Products’ operational capabilities but also aligns with their commitment to sustainable and cost-effective practices.
According to Nyle Dry Kilns, Wholesale Building Products invested in a solution that significantly boosts their production capacity while maintaining the highest standards of quality. Nyle’s kilns are built to handle large volumes of lumber while maintaining reliability, ensuring that Wholesale Building Products can meet increasing market demands. This successful installation is a testament to the collaborative effort between Nyle’s teams and reflects their dedication to innovation and excellence in kiln manufacturing.
For more information on Nyle Dry Kilns’ wide range of products and services, visit www.nyle.com or call (800) 777-6953.
IWT-Moldrup Introduces New Quality Certification For Thermally Modified Wood
IWT-Moldrup based in Denmark and Singapore has introduced a new system, Moldrup-TMT classes 3.1, 3.2 and S for reliable quality certification of thermally modified wood.
Thermal modification has gained increased market share around the world during recent years. The market has been missing a quality assessment and certification system based on the actual treated wood instead of a process-based system like the Thermowood scheme.
IWT-Moldrup has developed the system based on EN335 Use Classes. EN335 as well as many other international standards for wood protection in Oceania and North America work with Use Classes. Use Class 3.1 (Europe and Oceania – UC 3.a. in North America) is used for wood which is occasionally wetted like cladding or joinery and Use Class 3.2 (Europe and Oceania – UC3b in North America) is used for wood wetted frequently and/or for longer periods of time, such as decking material and has an extra layer of protection in form of renewable coating, boicide treatment or resin treatment where biocides are not acceptabe, and class “S” for wood where durability is not an issue but increased dimensional stability is wanted. IWT-Moldrup has one class called Moldrup-TMT “Heritage” for those that want the aesthetic of worn wood and the visual appearance of the wood still maintain the integrity of dimensional stability and durability.
The Moldrup system incorporates a quality control by an independent third-party inspection agency of the treated wood instead of being just process based. Process based quality controls have been used for biocide impregnation also, but the industry generally recognizes the need for a result-based system like the one that IWT-Moldrup is now proposing for thermally modified timber.
The marketing of quality checked thermally modified timber is backed by an extensive toolkit including labeling of the wood, wood packs, datasheets for customers and dealers as well as video material to use on websites.
IWT-Moldrup’s treating plants are sold by AWT (American Wood Technology) in the U.S. AWT is located in Jefferson, GA.
For more information, visit www.moldrup.com or www.AmericanWoodTechnology.com.

SFPA Announces LaSalle Lumber Co. And Others As 2023 Sawmill Safety Award Recipients
The Southern Forest Products Association has announced the recipients of the John Edgar Rhodes 2023 Sawmill Safety Excellence Awards. The SFPA Safety Awards embody the impact, dedication and legacy of the Association’s founding leader, John Edgar Rhodes.
The eight award recipients represent a record of 2,282,255 total hours worked among 987 employees – achieving safety excellence with zero reported incidents. As a side note, this follows two years in a row where seven member mills reported zero incidents.
SFPA Lumber Manufacturer members are considered for the award based on standardized information submitted using OSHA Form 300A. Awards are presented in three divisions and safety performance is judged by how each mill’s safety record stacks up against facilities with comparable lumber output throughout the year.
“In an industry where worker safety is of utmost importance, operating without any reportable incidents is a significant achievement,” said Eric Gee, SFPA’s executive director. “We are extremely proud of each of these operations and their commitment to safety excellence.”
Division One: (SFPA member mills that produce 50 million board feet or less annually)
- Almond Brothers Lumber Co. – Coushatta, LA
- McShan Lumber Co. – McShan, AL
- Swift Lumber – Atmore, AL
Division Two: (SFPA member facilities that produce 51 to 150 million board feet annually)
- West Fraser – Fitzgerald, GA
- West Fraser – Lake Butler, FL
- West Fraser – Blackshear, GA
- West Fraser – Mansfield, AR
Division Three: (SFPA member mills that produce more than 150 million board feet annually)
- LaSalle Lumber Co. – Urania, LA
Having a successful career in the forest and paper industry, Rhodes was chosen to lead the Southern Pine lumber industry. Under Rhodes’ leadership, the Association grew into the model trade association in American industry. He was a strong champion for the forest products industry – advocating for proactive forest resource management and standardized grading rules.
SFPA represents Southern Pine lumber products and services around the globe, managing a comprehensive product promotion program. Our mission is to advance the Southern Pine lumber industry, promote the use of member products in domestic and international markets, and facilitate the exchange of information and ideas.
For more information, visit www.sfpa.org.
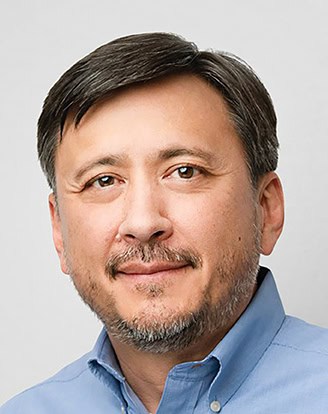
SLB Study Reveals Importance of WUI Code Work in Defending Market Share
According to the Softwood Lumber Board (SLB) up to 150 million board feet of siding and 770 million board feet of decking from the repair and remodeling market are at risk from Wildland-Urban Interface (WUI) code changes and adoption, according to an SLB-funded study by Forest Economic Advisors. The study quantifies the importance of the American Wood Council (AWC) and the SLB’s codes and standards work defending the use of lumber in regions with wildfire hazard.
“The Forest Economic Advisors (FEA) study is timely and relevant given recent major wildfire losses and significantly increased WUI code activity as a result,” says Phil Line, vice president of codes and regulations at the AWC. “The study findings that lumber siding and decking are at risk aligns with WUI code requirements that regulate exterior building materials to reduce the spread of fire.”
Wildfires have been on a steady increase in recent years. Between 2005 and 2022, more than 100,000 structures were lost to fires in areas where structures and development meet undeveloped wildland or vegetative fuels. More jurisdictions are considering implementing building codes to mandate wildfire-resistant construction in these areas.
FEA’s analysis shows that while the use of lumber and structural panels is not affected by WUI codes when used structurally in roofs, walls, and floor systems, lumber volumes in the repair and remodeling market, especially decks and siding, are at risk. While the higher end of the estimates is not likely to be lost over the short to medium term, the potential volumes represent between 7 percent and 17 percent of total consumption for siding and 4 percent and 14 percent for decking.
The AWC is active in the development process for WUI codes including ICC 605, the new standard for residential construction in regions with wildfire hazard. The AWC is also using full-scale fire tests of hardened wood-frame buildings to demonstrate the viability of fire-resistant wood construction versus noncombustible materials alone.
SLB investors can request a copy of the report by emailing info@softwoodlumberboard.org or visit www.softwoodlumberboard.org for more information.
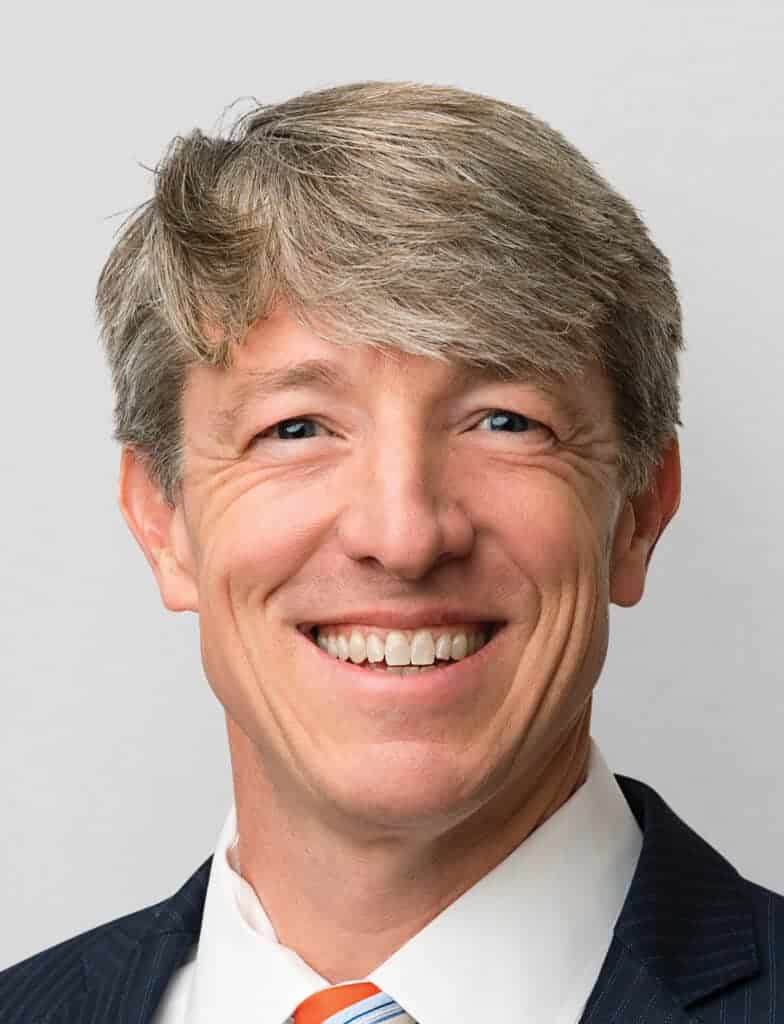
AWC Selected for $6 Million EPA Grant for EPD Development
The American Wood Council (AWC), headquartered in Washington, D.C., has been selected for a $6 million grant from the Environmental Protection Agency (EPA) to increase transparency in the U.S. wood product industry by further developing Environmental Product Declarations (EPD) and Product Category Rules (PCR) for the industry.
AWC’s successful grant proposal was submitted as part the EPA’s Inflation Reduction Act funding that seeks to reduce embodied greenhouse gas emissions for construction materials and products.
“This grant will ensure existing data gaps of wood products’ environmental performance are filled, furthering the industry’s commitment to radical transparency and informing our remarkable sustainability story,” AWC President and CEO, Jackson Morrill, said. “The projects that will be funded from this grant will bring the whole of the industry together to collect and report life cycle data for the U.S. wood products industry. We thank the EPA for its commitment to collecting robust data that will ultimately support meaningful reductions of carbon in the built environment.”
Overall, this grant aims to support work that will reduce embodied carbon emissions in building products globally and locally through the development of an EPD generator, creating a funding mechanism for mills to develop their own EPDs, educating AEC firms on whole building life cycle assessments utilizing EPDs, and other projects that will result in more robust data for the U.S. wood products sector at large.
“This grant ensures coordination among the industry to fill existing data gaps and bring the whole of the industry together to collect and report life cycle impact data for U.S. wood products,” said Rachael Jamison, AWC’s vice president of markets and sustainability.
AWC is currently working with the EPA and partners to refine project scope and timelines. The grant supports work over a five-year period.
Partners included in the grant include the Treated Wood Council, U.S. Endowment for Forestry and Communities and WoodWorks.
AWC has also launched its expanded Life Cycle Survey to collect life cycle impact data from wood product mills across the United States. The Survey, first launched in 2022, has previously only been open to AWC member companies. However, with support from a 2023 Wood Innovations Grant (WIG), the Survey is now open to all U.S. wood product mills.
The Survey is the central collection point for the U.S. wood product industry’s life cycle impacts data, and its expansion will lead to more representative and stronger datasets, adding even more strength to the sustainability claims of U.S. wood products. As a low-carbon building material, wood is a right now solution in helping to lower the environmental impact of the built environment.
“U.S. wood products have a powerful sustainability, carbon and rural development story made even stronger by the data AWC is collecting through our survey. Wood products are the lowest in embodied carbon of the major structural building materials and as we continue to work to reduce carbon emissions, data driven solutions are more and more imperative. The data we have collected shows that specifying wood products are a climate solution to lower the carbon impacts of a building,” said Rachael Jamison, vice president of markets and sustainability at AWC.
The Survey collects production and process data from mills helping to trace the life cycle of wood products. The data collected includes values related to primary products, byproducts, fiber sourcing information, energy use, waste generation and more. This data is then brought together and analyzed to demonstrate the low environmental impact and sustainability of U.S. wood products. The data is used to generate industry life cycle assessments (LCAs) that then becomes the basis of Environmental Product Declarations (EPDs).
“The survey is a vital tool that demonstrates our industry’s commitment to data transparency. The more mills that participate, the more representative the data will be,” said David Brabham, Co-Chair of AWC’s Sustainability Committee. Tyler Congleton, fellow Sustainability Co-Chair, added, “The survey data, resulting LCAs, and published EPDs work together to tell our industry’s remarkable sustainability and low embodied carbon story.”
The Life Cycle Survey is now open to all eligible U.S. wood product mills and manufacturers.
To participate contact Adam Robertson at adam@sustainatree.ca.