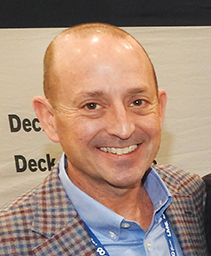
Industry News
Culpeper Wood Preservers Expands Fire-Treated Lumber Availability to the Northeast
Chris Brown
Culpeper Wood Preservers, a leading manufacturer of pressure-treated lumber, is expanding its FlamePRO® fire-retardant lumber product offerings into the Northeast region of the United States. The availability of Culpeper fire-treated wood will help serve the multifamily and commercial construction sectors across the region by making faster delivery times available.
Culpeper’s plant in Lancaster, MA, is the first of the organization’s Northeast facilities to stock fire-treated lumber, which will help reduce lead times for Culpeper’s contractor and dealer customers in the region.
“At Culpeper, we are constantly looking for ways to better serve our customers and meet growing market demand,” said Chris Brown, executive vice president at Culpeper Wood Preservers. “By bringing our fire-treated lumber to Lancaster, we’re not only expanding our product reach, but also helping regional builders minimize delays and keep projects on schedule.”
Culpeper FlamePRO brand fire-retardant treated wood is pressure-treated with proven FlamePRO Interior Type A High Temperature fire-retardant chemicals. It is an independently tested, proven formulation based on the American Wood Protection Association P50 Standard for fire retardants.
In addition to fire-treated lumber, the Lancaster location provides all of Culpeper’s traditional MCA pressure-treated lumber that customers know and trust.
Culpeper Wood Preservers is one of the largest producers of pressure treated lumber in the United States. In 1976, Culpeper Wood Preservers started from a single location in Culpeper, VA. Today, the company is a leading manufacturer of pressure-treated products for the residential, commercial, industrial and marine markets. Culpeper Wood Preservers’ brand name products are sold exclusively through independent lumber dealers throughout the Mid-Atlantic, Northeast, Midwest and South.
For more information, visit culpeperwood.com.
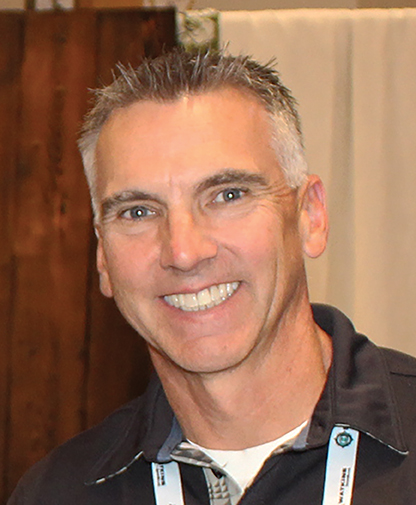
Elk Creek Forest Products Acquires All-Coast Forest Products
Brett Slaughter
Elk Creek Forest Products, located in McMinnville, OR, a full-service lumber producer and distributor, announced that they have acquired All-Coast Forest Products.
Brett Slaughter, president of Elk Creek Forest Products stated, “All-Coast Forest Products is a company that we admire, and are deeply honored to be carrying on their long-standing legacy and tradition.” Opening in 1975 and being a family-owned business since 1978 and located in Cloverdale, CA, since 1988, All-Coast shares values that resonate with Elk Creek Forest Products, creating a strong foundation for integrity, commitment to service, partnership and innovation. Slaughter went on to say, “We are grateful that we have now joined the Elk Creek and All-Coast families together, carrying on a joined legacy for both companies.”
Elk Creek is committed to preserving the legacy of quality lumber products and customer service that has defined All-Coast’s success over the past 50 years.
Elk Creek Forest Products is a trusted name in the lumber distribution industry, specializing in sourcing, producing, milling and delivering Douglas Fir products ranging from commodity to premium categories. Their commitment to excellence, pride in their products and dedication to meeting customer needs drives their growth, fostering partnerships that last decades, stated a company spokesperson.
For more information, visit elkcreekforest.com.
Hancock Lumber Acquires Johnson Lumber
Hancock Lumber, a family-owned integrated forest products company operating high-efficiency White Pine sawmills, a network of lumberyards, truss and wall panel manufacturing facilities, full-service kitchen design showrooms, and a robust e-commerce shopping and online account management platform, closed on a deal to acquire Johnson Lumber, a single-location lumberyard based in Salisbury, MA. The deal closed recently and business operations under the Hancock name have begun. This will be Hancock Lumber’s 12th lumberyard but their first in Massachusetts.
Johnson Lumber has been a family business since its opening in 1963, with an extensive presence in Northeast Massachusetts, Southern Maine and Southern New Hampshire. Johnson Lumber is located on 12 acres that house covered storage in addition to contractor focused inventory. Johnson Lumber is an operation that is motivated by delivery, as more than 80 percent of its sales are delivered to job sites.
Including three second-generation owners, 20 employees from Johnson will join Hancock. Two of those owners will remain on to assist with the transition while one of them will work full-time.
This acquisition, according to Hancock, is considered an extension of the company’s markets by amplifying the reach between existing locations, such as the Kennebunk, ME, and Wolfeboro, NH, sites, which are around 40 to 70 minutes away. The acquisition of this lumberyard will assist in expanding important product lines including wall panels, trusses, Tiny Homes and Pine products all made by Hancock. Marvin window product lines will also experience growth, while increasing additional capacity and efficiency for delivery across the region.
Hancock Lumber was founded in 1848, has 750 employees and has a people-first and values driven culture.
For more information about Hancock Lumber, visit hancocklumber.com.
Allweather Wood Improves Safety And Durability of Redwood Siding
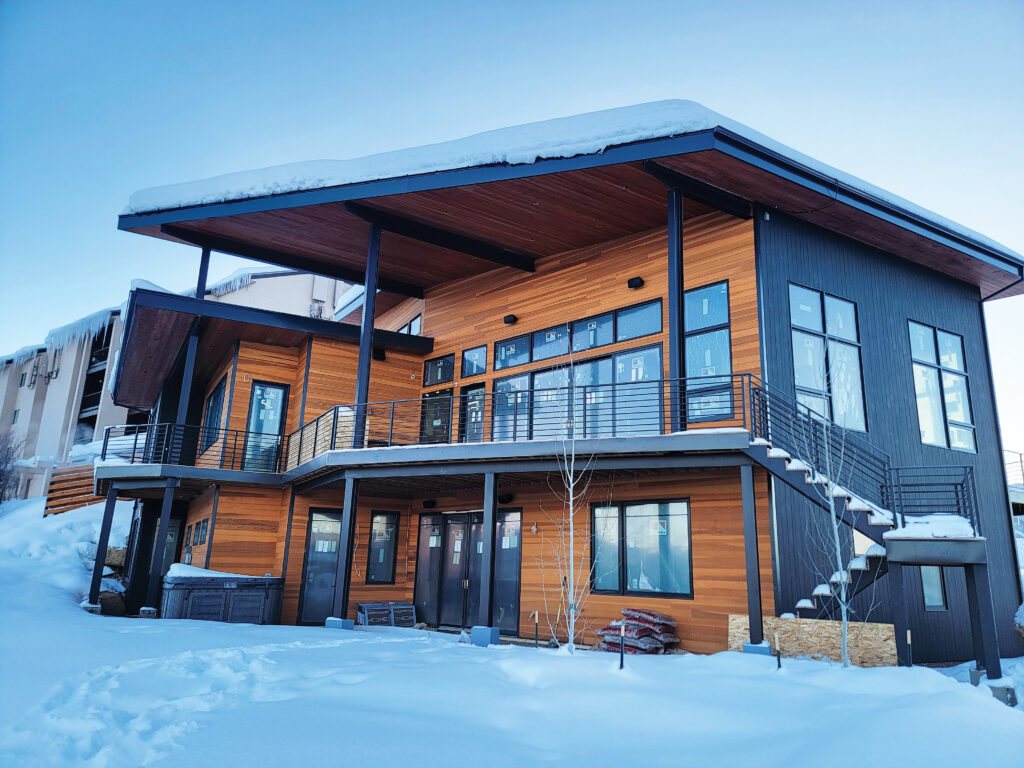
Allweather Wood’s new product line, Class A Fire Retardant Treated Redwood Siding.
Allweather Wood recently launched a new product line that improves upon the safety and durability of Redwood siding.
The new product line is a Class A Fire Retardant Treated Redwood Siding.
Allweather Wood, the manufacturer and distributor of the Redwood siding profiles, explained the product is treated with the Exterior Fire-X® fire retardant formulation from Hoover Treated Wood Products.
The treatment process gives the wood a Class A fire rating, a step above the Class B designation that typical Redwood siding receives naturally, with no treatment.
“This treatment ensures that your siding not only retains the natural beauty of Redwood but also offers enhanced safety and fire protection,” the company said. “Designed for exterior applications, our fire-retardant-treated Redwood meets the highest standards for durability and performance, especially in wildfire-prone areas.”
The product is launching throughout Allweather Wood’s central and southwest sales regions — California, Colorado, Kansas, Nebraska, Nevada, New Mexico, South Dakota and Wyoming.
The company says the ability of the product to meet Class A requirements is a market advantage, especially as some municipalities step up their codes from Class B to Class A in efforts to mitigate damage from fires.
Allweather Wood operates six treating plants in California, Colorado, Oregon, Utah and Washington, three distribution centers in California and Hawaii and remanufacturing and fencing plants in California.
For more information, visit allweatherwood.com.
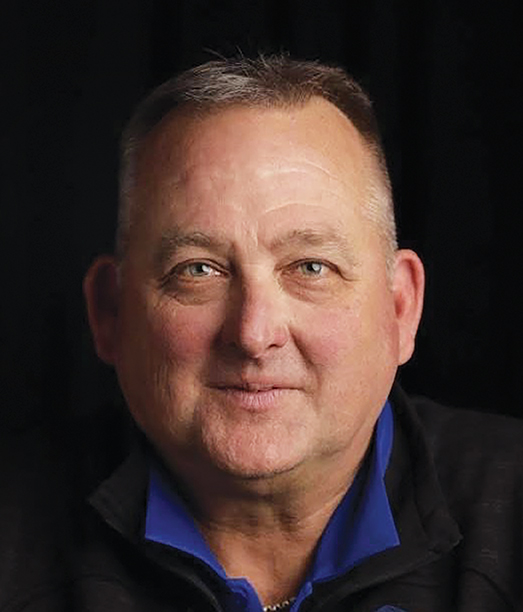
Richardson Timbers Announces New COO And New Products
Harley Finnell, Jr. “Bubba”
Harley Finnell, Jr. “Bubba” has recently been promoted to chief operating officer (COO) at Dallas and Bertram, TX-based, Richardson Timbers.
The Texas remanufacturer focuses on milling wood timbers and manufacturing custom made millwork products in addition to corbels, brackets, timber truss arches and rafter tails. Species offered include: Western Red Cedar, Douglas Fir, kiln-dried Fir, specialty exotic timbers and mixed hardwoods.
Finnell has been a member of the forest products industry since June of 1978, where he started at Oldham Lumber Co. in Dallas, TX, as a sweeper and order puller. He also worked in the dispatch, sales and purchasing departments in addition to being a general manager until 1986. In 1987, he transitioned to Sunnyvale, TX-based, Associated Truss & Lumber as the general manager until 1995. From 1995 to 1996, he worked at International Paper, which is headquartered in Memphis, TN, as the manager of the carpenter’s corner. He returned to Oldham Lumber Co. in 1996 and became the owner in 2003. He left in 2021 to join ULBM as the market president of the Dallas, TX, and Fort Worth, TX, locations.
Finnell graduated from McComb, MS-based, McComb High School in 1978.
Jerolyn Finnell is his wife of 43 years and they have two grandchildren ages 23 and two-and-a-half. He enjoys golfing and car collecting.
Finnel is the president and a member of the board of directors for the Lumbermen’s Association of Texas and is an LBM advantage member.
In other news, Richardson Timbers is now offering Accoya and Red Grandis. Accoya wood, according to a Richardson Timber representative, is “known for its exceptional durability, dimensional stability and resistance to rot. Accoya is a natural fit for Richardson Timbers’ high-quality exterior applications like siding, decking and architectural elements. Their ability to mill large and unique timber profiles makes them an ideal partner for projects requiring the long-lasting, sustainable benefits of Accoya.”
Red Grandis is sourced from the Eucalyptus Grandis tree and ranges in pale pink to deep red. It “offers a warm and appealing aesthetic,” stated a company representative. The wood is also “highly durable, resistant to decay, and easy to work with, making it ideal for end-user products and even outdoor applications. Its sustainable sourcing from FSC-certified plantations adds to its appeal as an eco-friendly choice.”
Call 214-358-2314 or visit richardsontimbers.com for more.

Woodgrain Transitions Leadership
Todd Dame
Woodgrain, a leading manufacturer and distributor of millwork and building materials, recently announced the implementation of its long-term succession plan.
The Woodgrain board of directors has elected a new chief executive officer, making a seamless transition to third-generation leadership and reinforcing the company’s long-term vision for continuity and growth.
After 16 years of dedicated service as chief executive officer, Kelly Dame will begin transitioning leadership responsibility to Todd Dame, who will assume the role of CEO of Woodgrain by September of 2025. Todd brings over 18 years of experience in the door, millwork and building products industry- most recently as president of the Woodgrain distribution division. Kelly Dame will remain actively involved as chairman of the board and trusted advisor.
He stated, “It has been my privilege to help guide Woodgrain’s growth alongside our exceptional team. Todd’s leadership experience and nearly two decades of commitment to Woodgrain will serve him well in this role. He is dedicated to our mission and values. I also want to express my heartfelt gratitude to all our dedicated associates and loyal customers.”
“I am humbled by the trust placed in me and excited to lead Woodgrain into its next chapter, building on our strong foundation,” said Todd Dame. “Throughout my life, I’ve had the honor of observing the generations before me lead Woodgrain with integrity, hard work and a genuine passion for our craft. Their example inspires me every day. As I take on this responsibility, I am committed to carrying forward the values they instilled in me—always putting our people and our customers first. Together with our incredible team, I look forward to building on our legacy, embracing new opportunities and ensuring that Woodgrain remains a company we can all be proud of for generations to come.”
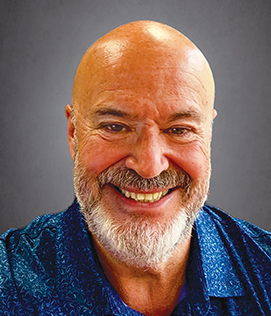
Steve Prado
In other news, Woodgrain recently announced the promotion of Steve Prado to vice president for the Southwest region of the distribution division. This newly established region includes the Woodgrain and Kelleher Corporation distribution centers in California and Hawaii.
Prado brings a wealth of experience to the role. He spent 26 years with OrePac Building Products and the last nine years with Kelleher, holding a variety of positions ranging from salesperson to senior vice president. Prado resides in Ontario, CA, with his wife, and they have a blended family of five sons, one daughter and a beloved bulldog named Stogie.
Woodgrain is a family-owned business and a leader in the millwork and building products industry, operating over 60 manufacturing and warehouse facilities across the United States and South America. With over 70 years of quality craftsmanship and service, Woodgrain is a leading producer of moulding, doors, windows and lumber, as well as a premier distributor of specialty building products. Woodgrain, Inc. is headquartered in Fruitland, ID.
For more information, visit woodgrain.com.
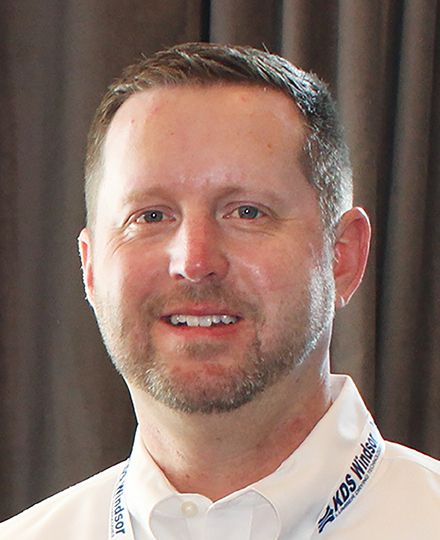
Adam Duplisea Appointed VP of Sales and Marketing at Nyle Dry Kilns
Adam Duplisea
Nyle Dry Kilns has recently appointed Adam Duplisea as their new vice president of Sales and Marketing. Duplisea joined the company in 2022, bringing with him 14 years of experience as an account manager in the transportation sector.
“Duplisea is dedicated to ensuring a positive experience for every customer. He is committed to collaborating with them to identify the optimal solutions for their specific operational needs,” stated a company spokesperson.
Passionate about understanding customer objectives, Duplisea enjoys listening to their experiences and working together to explore how Nyle Dry Kilns can help them reach their goals by offering relevant ideas and options, the spokesperson continued.
Outside of work, Duplisea enjoys golfing, fishing and spending quality time with his wife, Janie, and their two sons, Jayden and Brentley.
For more information, visit nyle.com.
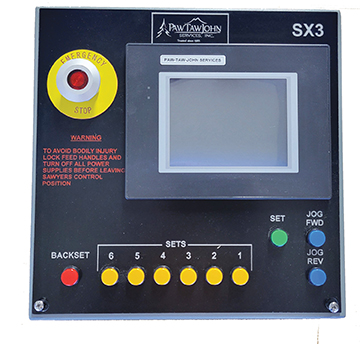
PawTaw John Services Inc. Introduces SX3 Setworks
Pictured is PawTaw John’s SX3 Setworks.
PawTaw John Services Inc., located in Rathdrum, ID, is now offering a cost-effective solution for precise linebar, vertical/horizontal resaw positioning and the ability to improve accuracy of two-saw edgers, with their SX3 Setworks.
The SX3 Setworks is a powerful single-axis motion controller designed to bring new levels of accuracy and efficiency to sawmill operations, affordably.
The SX3’s self-contained controller operator panel integrates all essential electronics, power and a user-friendly Human Machine Interface (HMI) for accurate positioning of both closed-loop and open-loop hydraulic cylinders and motors.
Key features and benefits of the SX3 Setworks include being a cost-effective solution, versatile application, integrated design, accurate measurement, flexible valve control, improved accuracy, reduced waste, minimized downtime, user-friendly operation and increased production efficiency.
The consistent resaw positioning allows for higher yields and less rework. This transforms a two-saw edger into a precision dimensional cutting tool. Replacing aging setworks with a reliable solution for continuous production.
The SX3 Setworks is an investment in the efficiency, accuracy and profitability of a company’s wood processing.
Call 208-687-1478 or email info@pawtaw.com to learn more about the SX3 Setworks or visit pawtaw.com for details and quotes.
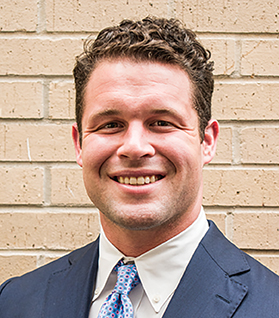
Taylor Machine Works Names Zach Taylor New Director Of Operations
Zach Taylor
Taylor Machine Works, headquartered in Louisville, MS, recently announced that Zach Taylor will be the company’s new director of operations. Zach steps into this role following the retirement of Greg Sisson, who has served Taylor with dedication for 41 years. Matt Hillyer, vice president of manufacturing and engineering remarked, “Greg’s leadership, knowledge and unwavering commitment have left a lasting mark on our organization, and we thank him sincerely for his many years of service.”
“It’s an honor to be selected to continue the legacy that my great-grandfather began, and there are big shoes to fill. I look forward to being part of significant improvement driving quality and customer satisfaction into our products,” remarked Zach.
In his new role, Zach will oversee all aspects of operations across the Taylor company, continuing Taylor’s mission to deliver the highest quality material handling equipment in the industry. Zach brings extensive leadership in management and operations from his previous position as director of Taylor Power Systems in Clinton, MS. Zach provided successful leadership to Taylor Power for nine years serving in the roles of operations manager, quality manager and director. Zach is a member of the fourth generation in the Taylor family.
“We are confident in Zach’s ability to lead our operations team at Taylor Machine Works into the future with energy, vision and integrity,” stated Hillyer.
For more information, visit taylorbigred.com.
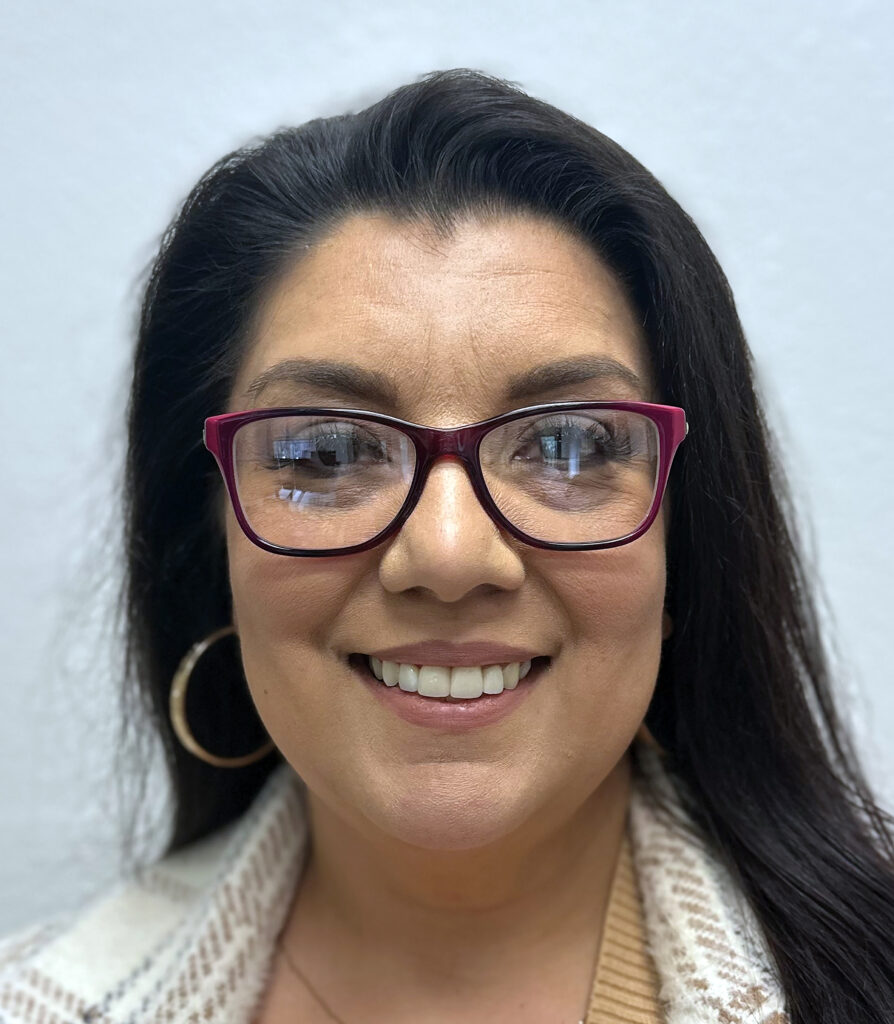
MiCROTEC Welcomes Maurita Maggard
Maurita Maggard
Maurita Maggard is the newest member of the MiCROTEC, in Corvallis, OR, sales team, bringing with her eight years of experience in the wood products industry. Prior to MiCROTEC, she held roles at Roseburg Forest Products – Engineered Wood Division as an inside sales manager and head of customer care and managed OEM national accounts with Timber Products.
MiCROTEC, a global leader in scanning and optimization technology for the industry, is known for cutting-edge solutions that increase production efficiency, product quality and resource sustainability. MiCROTEC has been setting industry standards since 1980, with operations in Corvallis, OR, and Vancouver, BC, serving North America, Australia and New Zealand.
Among the technologies Maggard represents are MiCROTEC’s CT Log and Goldeneye Transverse systems. The CT Log is the only computed tomography log scanner. It provides a full internal reconstruction of each log, enabling precise quality grading, optimized sorting and real-time cutting solutions for maximum value recovery.
The Goldeneye Transverse is a high-precision multi-sensor scanner that inspects lumber from all four sides— whether green, dry or planed. Integrating color and laser imaging, the system enhances production through accurate quality detection and fast, straightforward transverse installation.
A native of Oregon, Maggard studied Business Management/Administration at the University of Phoenix. Outside of work, she enjoys photography, catering and event planning, travel, muscle cars and football — especially the Denver Broncos. She and her husband, David, have been together for 15 years and are proud parents of five children.
MiCROTEC is a member of several major industry associations, including the National Hardwood Lumber Association, Southeastern Lumber Manufacturers Association, Southern Forest Products Association, Indiana Hardwood Lumbermen’s Association, Northeastern Lumber Manufacturers Association, Mississippi Lumber Manufacturers Association and Western Wood Products Association.
For more information, visit microtec.com.
Combilift Launches Two New Products Ready For Purchase
At LIGNA 2025 in Hannover, Germany, Combilift introduced two new solutions for timber handling that are made to increase safety, efficiency and decrease the environmental impact of long-load operations.
The Combi-FSE 8000, a heavy-duty electric sideloader for long loads, offers an eight-ton lift capacity for handling a variety of wood products in confined outdoor or indoor spaces. It has emission-free operation with the twin 18kw drive motors to provide the torque and responsiveness needed for heavy packs, in addition to all-electric performance suitable for indoor timber stores.
The steering and traction designed for muddy or uneven outdoor conditions are patented, while the under-deck battery position and glazing gives operators unimpeded visibility even when reversing in narrow racking aisles or busy sawmill loading areas. The quick battery change is, according to a company representative, “ideal for multi-shift operations in busy timber yards.”
Combilift also has the Combi-Connect, a telematics system created for “real-time machine performance tracking and maintenance planning,” stated the Combilift representative.
Combilift’s Combi Load Xtender, which is described as a “pantograph-style load extender that enables complete loading and unloading of trailers or rail wagons from a single side — a major advantage in timber yards where space is tight, or trailer access is limited.” With the Xtender, packs of timber can be loaded from only one side and its compact design allows for smooth motion and complete functionality below the height of a standard trailer without interference.
Martin McVicar, the CEO of Combilift, stated that the products, which are now available for ordering, were created as a response to what Combilift has been hearing from the timber industry- that customers have a need to transport bigger loads in smaller spaces with more safety and less emissions.
For more information about Combilift, visit combilift.com.
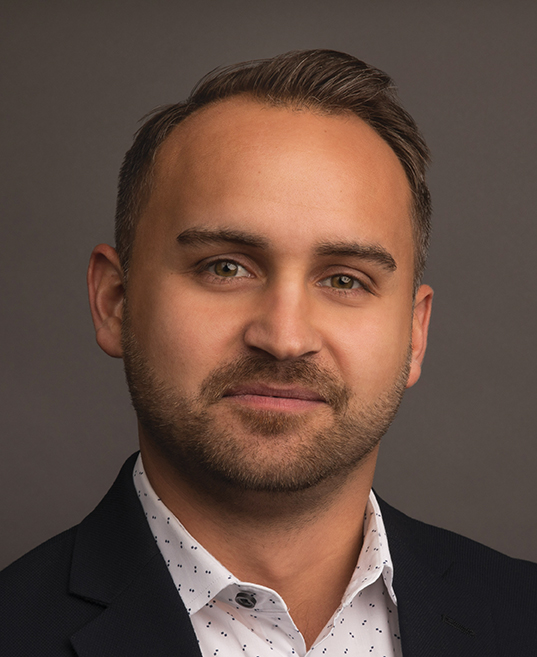
The AGL Group Acquired ADA Logistics Corporation
Steve Zambo
The AGL Group, an international and domestic logistics firm headquartered in Weymouth, MA, announced the acquisition of ADA Logistics Corporation, a domestic brokerage based in Ada, MI. This strategic acquisition strengthens AGL Group’s domestic logistics brand by adding valuable flatbed capacity and expanding its presence in the Great Lakes region.
Steve Zambo, CEO of The AGL Group, expressed enthusiasm about the acquisition, stating, “This is an exciting opportunity, as this will add strategic flatbed capacity to AGL’s growing domestic logistics brand, as well as a greater presence in the Great Lakes Region. ADA has grown a great brand over the years and we are excited to continue to service their clients as well as create a stronger offering to our current clients.”
ADA Logistics has built a strong reputation in the industry, specializing in domestic freight solutions with a focus on flatbed transportation. By integrating ADA’s expertise and customer relationships into AGL Group’s operations, the company aims to enhance service offerings, increase efficiency and deliver greater value to customers across North America.
The acquisition aligns with The AGL Group’s commitment to growth and excellence in the logistics sector. Existing ADA Logistics clients can expect a seamless transition, with continued high-quality service and expanded resources available through The AGL Group’s extensive network.
For further information about The AGL Group and its services, please visit aglgroup.com.
AWC Releases Updates to Connection Calculator And National Mass Timber AMM Guide
The American Wood Council (AWC), located in Leesburg, VA, released an updated version of its Connection Calculator. The Calculator supports users by calculating capacities for single bolts, nails, lag screws and wood screws based on the provisions of the 2024 National Design Specification for Wood Construction (ANSI/AWC NDS-2024).
Key updates include adding the design provisions for calculating fastener head pull-through for nails and wood screws and the addition of explicit lateral design provisions for smooth shank metal hardware nails and deform shank nails. The updated provisions for nails include Roof Sheathing Ring Shank nails and Post-Frame Ring Shank nails. The fastener head pull-through calculations were added to align with the required check in the side member where nails and wood screws are loaded in withdrawal from the main member.
An additional update includes the removal of the diaphragm factor for nailed connections in Chapter 11 as its effect on shear wall and diaphragm design values are already included in the 2021 Special Design Provisions for Wind & Seismic (ANSI/AWC SDPWS-2021).
The Calculator can determine both lateral (single and double shear) and withdrawal capacities and includes adjustment factors for temperature, wet service, varying load durations and end grain. Additionally, multiple types of connections including wood-to-wood, wood-to-concrete and wood-to-steel can be calculated using sawn lumber, glued laminated timber, cross-laminated timber and wood structural panels.
The updates to the Connection Calculator follow last year’s updates to the AWC Heights and Areas Calculator which is based on the provisions in the 2021 International Building Code. The updated version now includes the new Type-IV mass timber construction types and heights and areas specific to the 2019 California Building Code.
The Connection Calculator is available online or as an app on Android, iOS and Windows devices.
The AWC also recently released a national Mass Timber Alternative Materials and Methods (AMM) Guide for use with the 2018 International Building Code (IBC). This new resource is designed to support building code officials as they review, permit and approve mass timber projects across the country.
The AMM Guide is designed to help bridge the gap between the codes adopted in each state and the newer mass timber provisions in the 2024 IBC. Adopting the most recent edition of the Building Code, like the 2024 IBC, can be a slow multi-year process for states or jurisdictions. As a result, there is sometimes a gap between what is included in the currently adopted code in a state and what is allowable based on the latest available ICC I-codes.
The AMM guide serves to fill that space by offering code provisions for jurisdictions without mass timber specific guidance.
The guide follows last year’s release of AWC’s Florida Mass Timber AMM Guide which was tailored to mass timber projects under the 8th Edition of the Florida Building Code. The Florida-specific Guide was recognized by building officials in the state as a key resource for new building projects and also supports the potential adoption of mass timber codes in the state by increasing officials’ familiarity with mass timber provisions in newer I-codes.
The Mass Timber AMM Guide and the Florida AMM Guide are available on AWC’s website along with additional wood construction standards such as the AWC/ANSI National Design Specification for Wood Construction and the Fire Design Specification for Wood Construction.
For more information, visit awc.org.
Comact Expands To St. George, SC
Comact recently announced the expansion of its operations with the lease of a 48,000-square-foot facility in Building 2 at Port 95 Business Park in St. George, SC. This strategic move marks Comact as the first tenant in this state-of-the-art industrial park, positioning the company to better serve its growing customer base.
“We are excited to expand our operations in St. George,” said Simon Potvin, CEO at Comact. “The new facility at Port 95 will enhance our spare parts service offerings and support our customers with greater efficiency. Its strategic location near Interstate 26 and Interstate 95 benefits our manufacturing and distribution, being close to our plant and our southern USA clientele, in addition to allowing us to ship efficiently across North America. We are proud to support Dorchester County and align this investment with our core values of commitment to our clients.”
John Truluck, Director of Economic Development for Dorchester County, expressed his enthusiasm for Comact’s expansion, stating, “Janko/Peakline’s investment in new speculative buildings at Port 95 is a game changer for economic development in western Dorchester County, much like Comact has proven to be a pivotal asset for the community of St. George. The fact that the two have teamed up, as Comact becomes the first tenant at Port 95, is special. We look forward to seeing the continued positive impacts of that partnership.”
The expansion highlights Comact’s commitment to delivering top-tier facilities and exceptional service, reinforcing its mission to provide clients innovative solutions and superior support.
For over 100 years, Comact has been a leading OEM in high-caliber wood processing equipment, digital technologies, cutting solutions, project services and aftermarket support. Driven by innovation and excellence, the company is dedicated to helping their customers address their most pressing operational and business challenges in today’s industry.
Whether for brownfield or greenfield projects, Comact’s expertise provides wood processing facilities with the confidence that their investments will yield superior performance, throughput and ROI. This ensures they remain competitive and achieve sustained growth in an ever-evolving market. “Trust Comact to deliver exceptional performance every time,” stated a company representative.
For more information, visit comact.com.
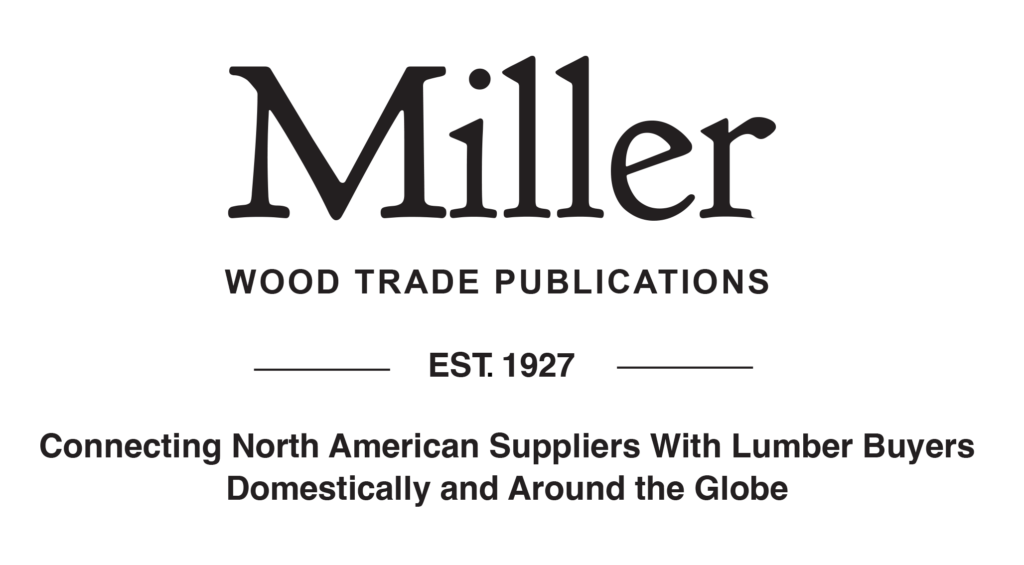