(Article Follows: Sawmill Safety: Addressing the Issues to Protect Your Business)
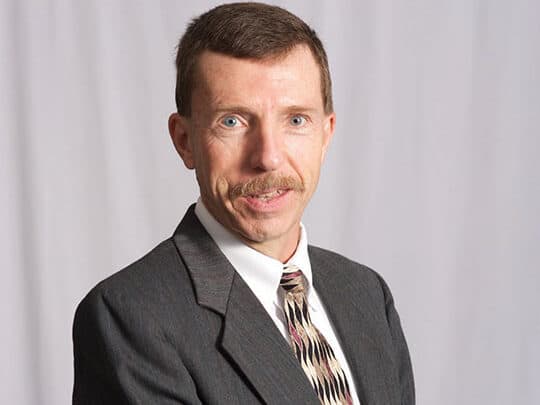
By Michael Culbreth, Loss Control Services Consultant,
Pennsylvania Lumbermens Mutual Insurance Company
Sawmills have been around for hundreds of years helping to build modern society and fuel our economy. While these institutions have long histories of keeping America humming, they also are no strangers to tragic injuries, deadly accidents and fires that have literally brought down the business.
In part one of this two-part series, we talked to you about risks related to poor housekeeping and maintenance, inadequate welding/hot work precautions and electrical issues at sawmills. We also offered tips to mitigate those risks. In this article, we’ll look at additional risks related to equipment, forklifts, lumber transport, general employee safety and more.
EQUIPMENT SAFETY
Unfortunately, the more comfortable we get with operating equipment – whether it’s a household toaster or an edger machine in a sawmill – the more likely safety rules are pushed to the back of the mind. Keeping safety concerns a priority for everyone is critical to operating a safe sawmill. This means both implementing equipment safety procedures and ensuring workers are properly trained in their daily work tasks.
Inadequate safety measures on or around equipment can lead to worker injuries, lost work time and costly workers’ compensation claims. To protect employees, ensure that machine guards are kept in place on equipment. Employees should also be sure to maintain a safe distance from moving blades and wear personal protective equipment including ear plugs, safety glasses, hard hats and proper shoes. Some may argue that the equipment is more accurate without these guards or operations move faster without the need for safety equipment, but the risk is certainly not worth the reward in this case.
Regular employee training is also critical for new and existing employees. This training should be designed to familiarize and reacquaint workers with the risks of a sawmill. Common sawmill accidents leading to workers’ compensation claims often stem from slips and falls, cuts and lacerations due to machine accidents and sprains, muscle and back injuries related to lifting and stacking lumber. More automated facilities tend to report fewer of these injuries as they have automated lumber sorters.
Further, if a worker notices a failing or inoperable machine, they should report it immediately so that the machine can be powered off and blocked from use. The machine should be locked out and properly tagged. Sawmills failing to implement a reliable lockout tagout program are often cited by the Occupational Safety and Health Administration (OSHA).
Forklifts/loaders are also a common source of accidents in sawmills. Anyone driving a forklift should be trained and qualified and should receive refresher training on a regular basis, at a minimum every three years. Following any accident, refresher training should be provided. When it comes to forklift operations, two types of training are necessary. Employees should be trained in general forklift safety and trained on the specific equipment they will be operating. Further, sawmill employees should be trained on industry specific tasks, including moving lumber around the yard, as well as in moving chips, dust and bark with a loader.
COMMERCIAL AUTO AND TRANSPORT RISKS
According to the National Highway Traffic Safety Administration, one in every 4,000 fatalities and more than 400,000 police-reported crashes involve heavy commercial vehicles. In recent years, insurance claims related to commercial auto accidents have been on the rise across all industries, including lumber.
What can make things particularly risky for sawmills is the fact that many don’t have a large fleet of commercial vehicles. This smaller fleet may lead to a more casual approach to commercial auto safety. However, these trucks are often busy transporting lumber, sawdust, bark and logs and without proper training, the drivers of these trucks may have less than optimal vehicle safety qualifications.
Aside from road safety and defensive driver training, drivers should also be trained in proper loading and unloading techniques. Drivers should be in a safe location while loading or unloading is performed (outside the cab and in a designated safe location if logs are being unloaded or any other material is moved overhead). Not knowing where a truck driver is when they are on your property can lead to a general liability risk.
Drivers should also be reminded repeatedly about the impact and dangers of distracted driving and instructed to never use their mobile phone while operating a vehicle. A good insurance partner, with experience in the wood niche, can assist policyholders with fleet safety resources including streaming safety training videos, continuous monitoring of driver MVR’s (Motor Vehicle Reports) and fleet telematics/vehicle camera technology.
Unfortunately, some commercial auto accidents are caused by unlicensed drivers or those who have been previously cited for DUI or aggressive driving. All businesses including sawmills should have a comprehensive driver safety program that incorporates driver training, qualifications, accident and incident reporting guidelines, vehicle use policies and more. Further, sawmills can consider motor vehicle record monitoring services and telematics to improve driver safety. With a good telematics program, managers will be able to learn more about employee driving habits like hard braking, hard accelerations, speed limit violations and other data. This creates a valuable opportunity to address and modify unsafe driving habits before an accident occurs.
PROPER IMPLEMENTATION IS KEY
A good sawmill safety plan should have many components but designing such a plan and implementing it doesn’t have to be difficult. As mentioned above, working with a good insurer who knows the wood niche, can significantly ease the burden. They can offer risk assessments, as well as loss control tips and programs. A simple professional risk assessment of the facility can go a long way. While your sawmill may have been operating without a significant incident for years, it’s always a smart decision to evaluate your risk and do what you can to reduce that risk exposure for the safety of your employees and the future of your business.
Michael Culbreth, Pennsylvania Lumbermens Mutual Insurance Company, is a loss control services consultant based in Inman, South Carolina who joined PLM in 2002. He protects businesses in territories including North Carolina and South Carolina. Michael can be reached at mculbreth@plmins.com or by phone at (267) 825-9146.