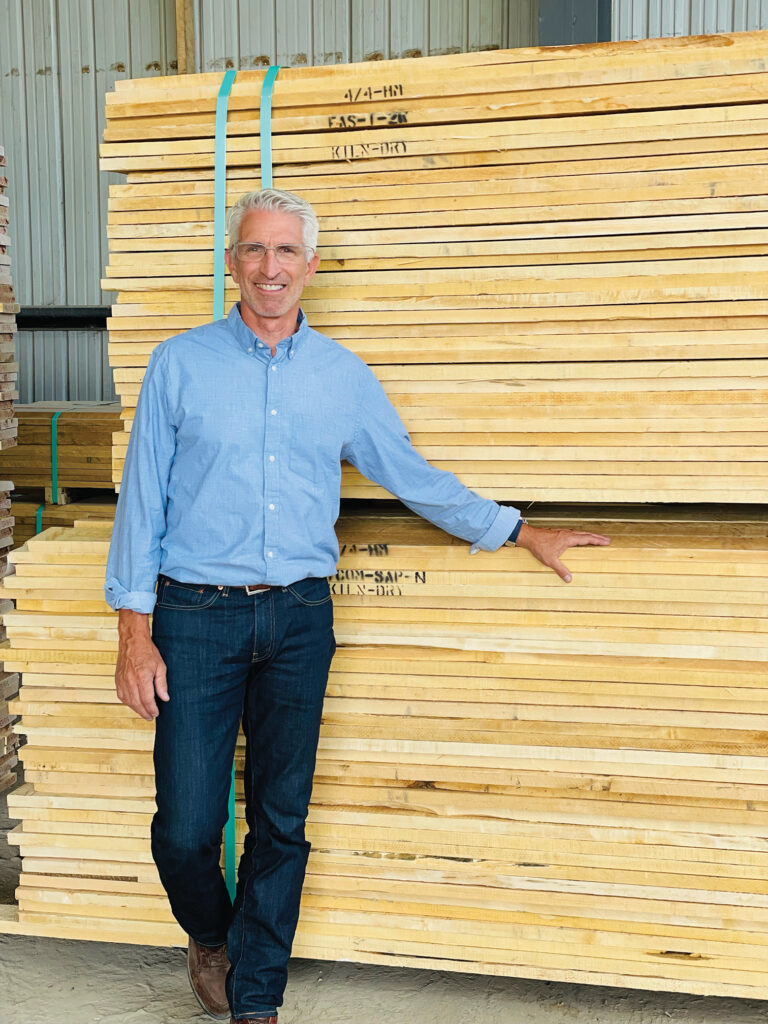
Portage Lake, ME – Maine Woods Company (MWC), located here, in the middle of 4.5 million acres of timberland, manufactures 14 million board feet per year with 60 percent Hard Maple, 25 percent Yellow Birch, 10 percent Soft Maple, 5 percent Ash, ranging in thickness from 4/4 to 9/4 in grade lumber and pallet cants. Over 800,000 acres of the timberland is privately owned by the Pingree family, who has been in the forest management business for over 180 years. The timberland is managed by Seven Islands Land Co. and is Forest Stewardship Council (FSC) and Sustainable Forestry Initiative (SFI) certified, with logs coming from a 200-mile radius of the mill. The plant, along with all other facilities combined totals 170 acres, with Scott Ferland as the General Manager.
Ferland has been the general manger at MWC for the past six years, and has been in the forest products industry, particularly the Hardwood sawmill side of it, for nearly 30 years, with his time spent between Turnquist Lumber Co., Inc., and Cersosimo Lumber Co. after he graduated from National Hardwood Lumber Association Inspector Training School in their 189th class. With his expertise, as well as the skill of their 55 employees, the Pingree family has a lot of trust in Ferland and his crew at the sawmill. As he says, “This mill is going on its 22nd year and there are many 20-plus-year employees. I know we all feel pretty much the same way, that it’s a unique commitment from ownership.”
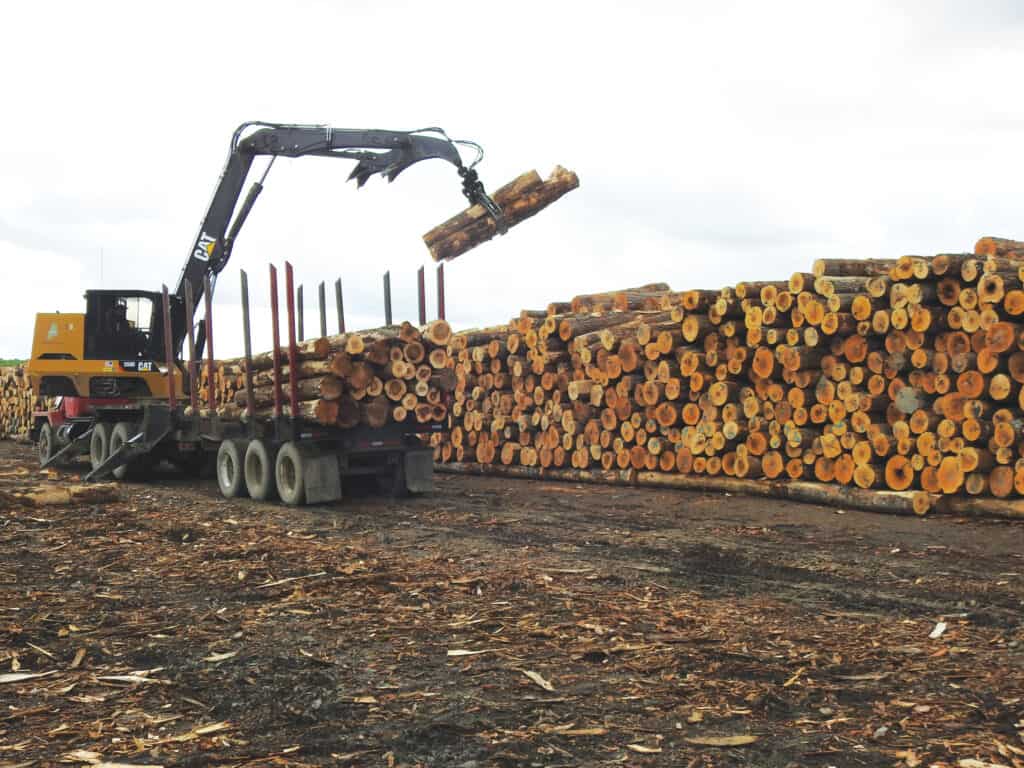
MWC’s products include KD and Green Hardwood lumber, both of which are double end trimmed and waxed with U-C Coatings’ Anchorseal prior to going into the kiln, and they use a uniform grooved sticker to eliminate sticker shadows. They have six American Wood Dryers with 500,000 board feet capacity, with enough storage and warehouse space to store 3 million board feet of dry lumber. MWC tarps all lumber that has been kiln-dried before it leaves the mill.
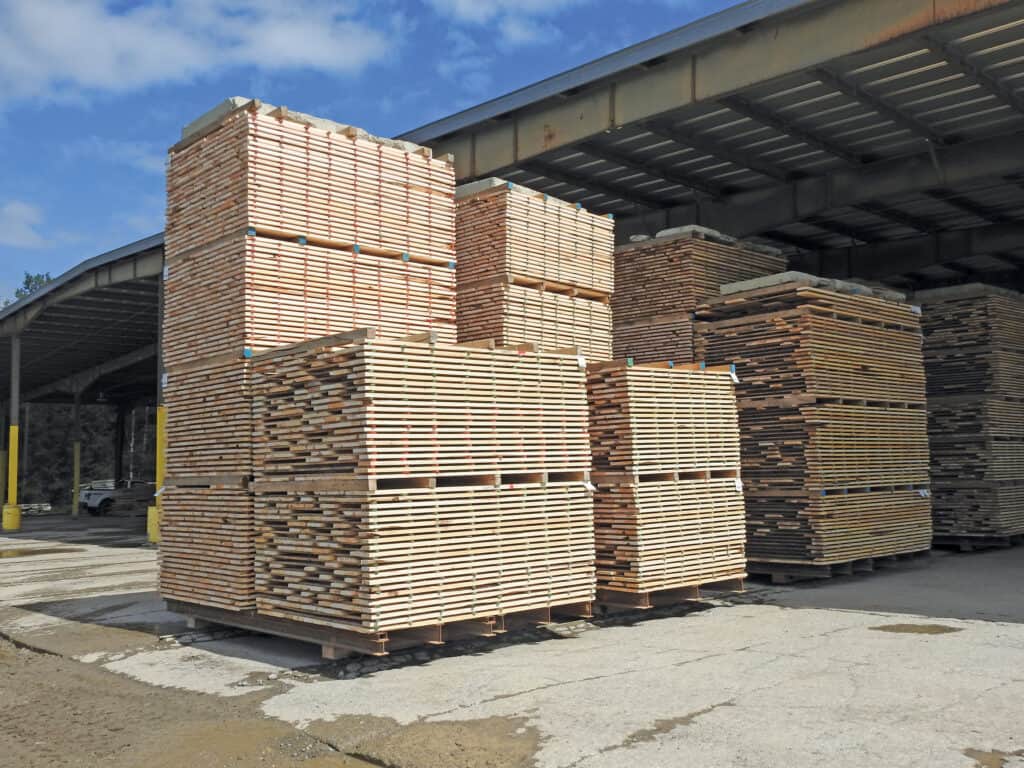
Recently they added a Newman 308 planer, which is a stand-alone operation, and has been incorporated into their grading facility. This allows them to dress the lumber as it is graded and enables them to be more efficient, giving their customers quicker turnaround times. Ferland said, “We are a typical New England mill, with our average length being a little longer than eight feet. We have decent diameters of our logs, with average width. We have flexibilities in our systems that we can put up lumber any way a customer would like. Any color designation, any width designation, length designation, special packaging, we try to be flexible with not only the forest product that we receive and how we must make good lumber out of it, but also on the customer’s end. If there are some needs that make their life easier, we will try to accommodate them,” Ferland remarked. “Should we need to do width sorts for our valued customers, we do it with a can do attitude!” he added.
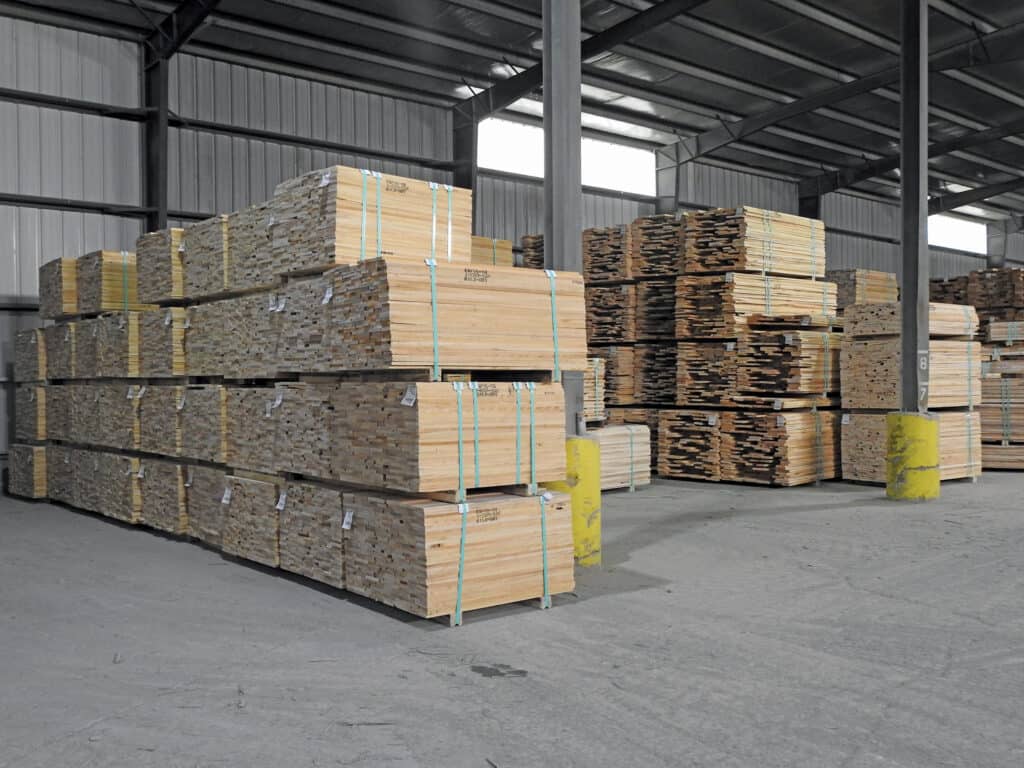
“Maine Woods has a diverse customer base by design which allows us to be flexible when deciding our sawing pattern for each species. We market our lumber to long-term customers who have come to rely on our consistency and quality for their needs while also keeping our eye on new opportunities that present themselves for potential new clients,” said Chris Castano, MWC’s sales and marketing director. “Since MWC only produces four different species, we are able to develop loads quickly and efficiently to the specifications that our customers need,” he continued.
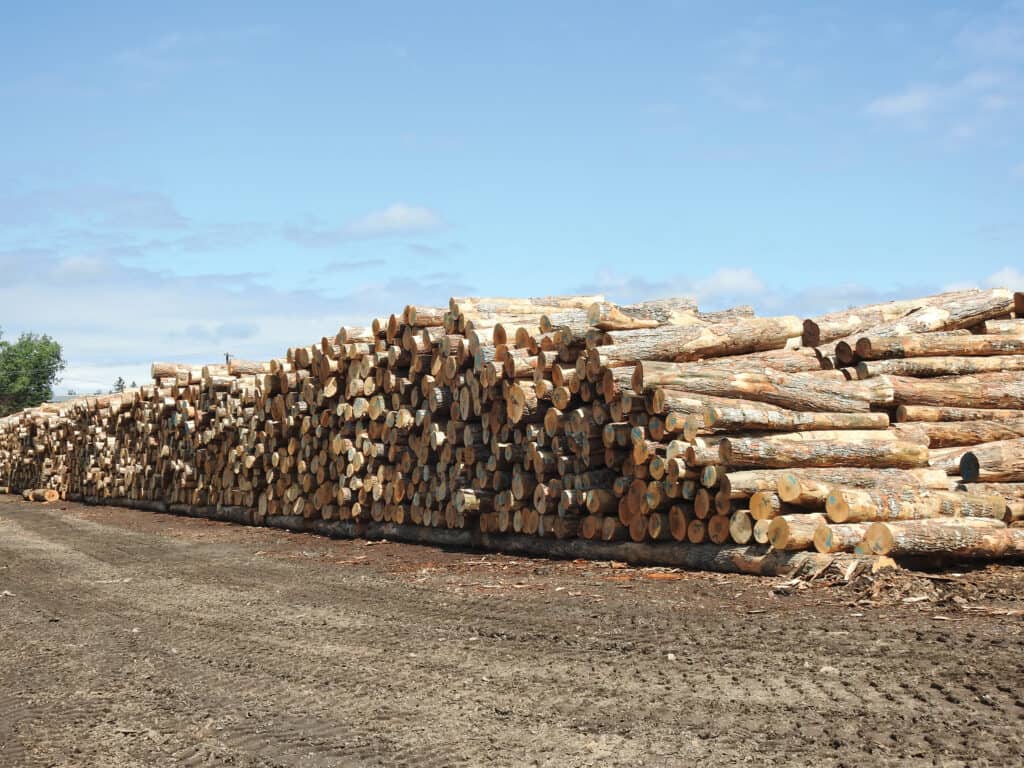
In order to provide their customers with consistency and allow them the ability to practically customize their lumber in the way they like, MWC uses a host of equipment: ring debarker by VK North America, a small diameter log break down by Maxi-Mill, a short log carriage by Sering Sawmill Machinery with a USNR scanner, a double cut slant carriage with a McDonough Manufacturing band saw, a Corley carriage with Lewis Controls scanner, a McDonough lumber re-saw, a Valley Edger with USNR optimization, an Autolog grading and sorting system, Piche Inc. grading and sorting system, Precision Lumber Inc. chippers, PHL stacker, Rawlings Manufacturing bark hog, and Caterpillar rolling stock.
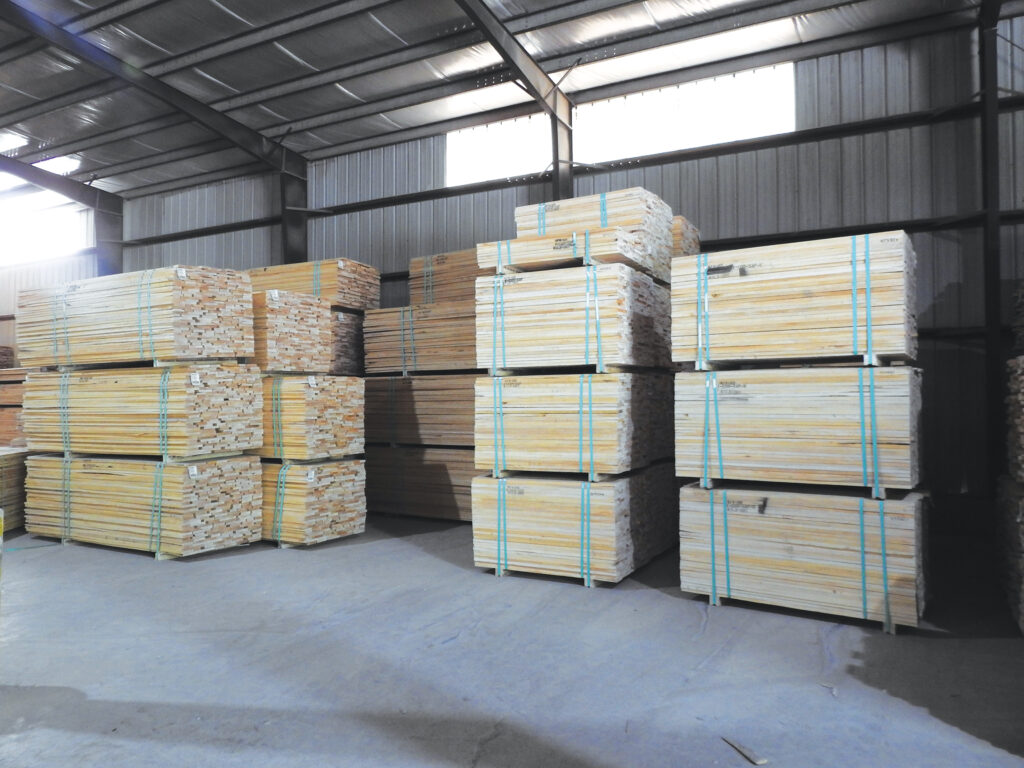
All this equipment allows them to produce 14 million board feet per year for their many customers that are secondary wood manufacturers in the furniture, moulding, cabinet, and flooring industries. Their lumber also is marketed to distribution yards throughout the United States, as well as to North American exporters that help distribute their product overseas. “We have a company policy of not directly exporting lumber, so we partner with reputable companies that do,” Castano noted.
While they currently purchase power from the grid, they have plans to install a generator within the next 18 months that will displace about 30 percent of the electricity that they purchase.
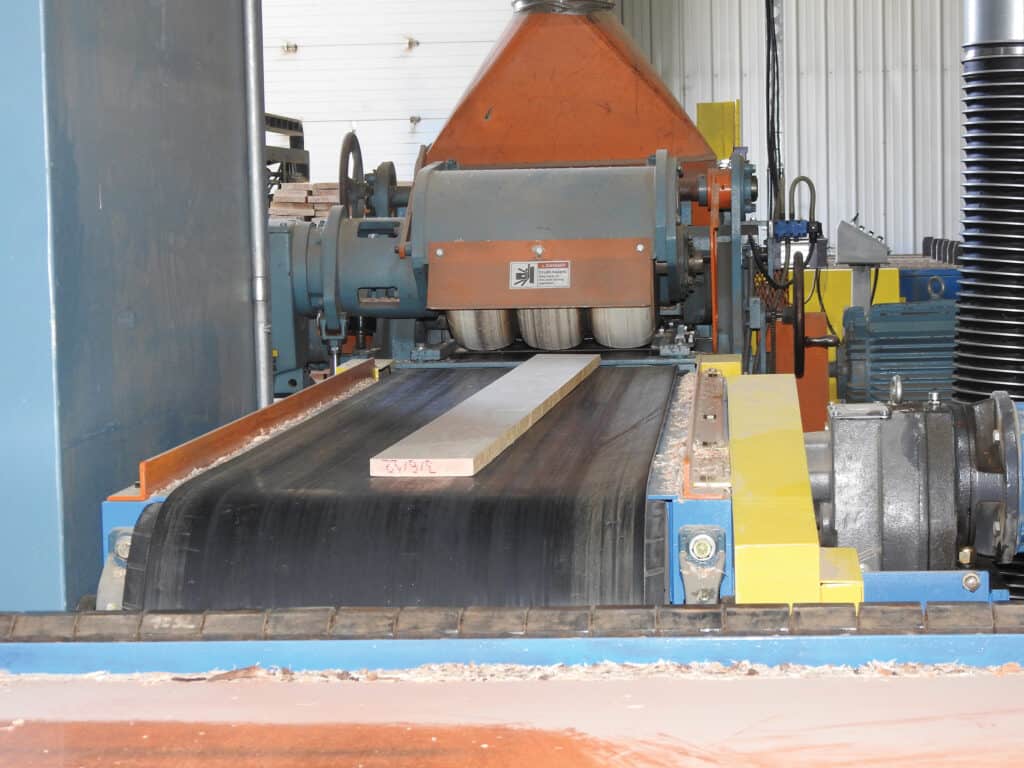
MWC’s processes to convert logs to lumber is efficient. They sort the logs after debarking, ranging between five to nine feet logs. They send smaller diameter, lower grade logs to a Maxi-Mill. All other logs go to a more traditional head rig. Maxi-Mill material goes to a gang edger, and cants are further processed at the re-saw. Mini-mill material will get sawn up on a carriage. Lumber is edged, then graded before trimming. After trimming, it is dropped into a sling sorter where they put it on sticks if it is going to the dry kilns. The industrial products are dead packed. The kiln-dried lumber is re-graded and trimmed, with the option of going through the planer before final packaging.
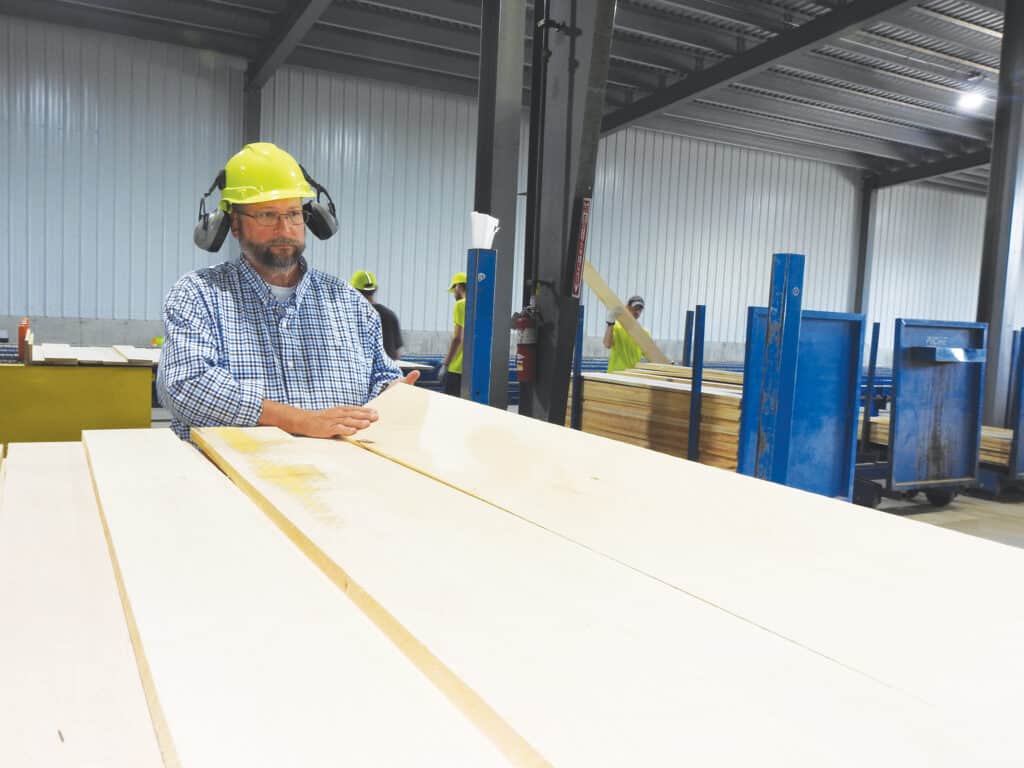
Ferland stated that it is a tremendous team that they have helping take care of the vast amount of acreage that supplies MWC. Seven Islands Land Co. has a team of about 20 for mapping, planning, forester operations, and contract negotiations, all of which have their forestry licenses. “In good times and bad we are going to continue to do what is right for the forest, something that Chris Castano lets our customers know, with some of our better customers being better customers for that reason,” Ferland stated.
MWC belongs to Hardwood Manufacturers Association, Wood Products Manufacturing Association, New England Lumbermen’s Association, Forest Stewardship Council, New England Kiln Drying Association, and Real American Hardwood Coalition.