By Rose Braden
President
Softwood Export Council
www.softwood.org
With the world’s attention now focused on making choices to reduce greenhouse emissions the forest products industry is positioned to become internationally recognized as the environmentally responsible material choice. Whether the ambitious commitments made at UN Climate Change Conference in Glasgow come to fruition, the fact remains that those in public and private sector are making decisions about material choices based on carbon emissions and renewability.
Construction materials and buildings play a significant role in either creating or reducing greenhouse gases. Residential and commercial buildings generate nearly 40% of annual global CO2 emissions. Of those emissions, building operations are responsible for 28%, while building materials and construction (referred to as embodied carbon) are responsible for an 11%. Just three materials – concrete, steel, and aluminum – are responsible for 23% of total global emissions, most of which is used in the construction sector.
Forests not only absorb and store carbon from the atmosphere as they grow, but after trees are harvested and processed into lumber and other wood products, approximately 50% of the dry weight of wood continues to be stored carbon. When forests are replanted, the cycle continues. U.S. Forest Service data show that U.S. forests reach their maximum capacity for sequestering carbon at about 80 years, after which the rate begins to decline. During the decades when trees are growing most rapidly, the carbon sequestration rate is fastest.
Wood – the Only Renewable Building Material
Wood is the only widely commercially used building material that comes from a renewable resource. Life cycle assessment studies show that wood is better for the environment than fossil fuel-intensive materials such as steel or concrete in terms of embodied energy, air and water pollution, and other environmental impacts.
For example, one study compared the environmental impacts of wood-frame and steel-frame homes in the cold climate of Minneapolis, Minnesota (U.S), where the average winter temperature ranges from -20°C to -9°C, and wood-frame and concrete-frame homes in the hot and humid climate of Atlanta, Georgia (U.S), where the average summer temperature regularly exceeds 32° C. Wood performed better than steel and concrete in terms of the energy required to produce the material, air emissions, and greenhouse gas emissions, and in particular:
- Embodied energy – The wood-frame homes had 17% and 16% less embodied energy, respectively, than the homes framed in steel and concrete.
Embodied energy is the sum of all the energy required to produce any goods or services, considered as if that energy was incorporated or ’embodied’ in the product itself.
- Air emissions – The wood-frame homes had 14% and 26% less emissions, respectively, than the homes framed in steel and concrete.
- Greenhouse gas emissions – The wood-frame homes performed 26% and 31% better, respectively, than the homes framed in steel and concrete.
Life cycle assessment studies also show that wood buildings require less energy during their entire life cycle—from resource extraction through manufacturing, distribution, use, and end-of-life disposal, and they are responsible for far less greenhouse gas emissions than fossil fuel-intensive materials such as steel or concrete. As shown in Table 1:
- Building a wall with kiln-dried wood studs, oriented strand board (OSB) sheathing, and vinyl siding instead of concrete with an exterior stucco coating results in 6.8 kilograms (15 pounds) of avoided CO2 emissions for every square foot of wall area.
- Using engineered wood I-joists with an OSB sub-floor rather than steel joists and OSB sub-flooring results in 9.97 kilograms (22 pounds) of avoided CO2 emissions for every square foot of floor area.
These differences are significant and applying this analysis to an entire building makes a strong case in favor of using wood to reduce carbon emissions. A five-story wood frame condominium building was found to store 3,970 metric tons of CO2 e (carbon dioxide equivalent) in its lumber, panels and engineered wood products. Another 8,440 metric tons of greenhouse gas emissions (CO2 e) were avoided by using wood instead of steel or concrete. Combined, this is equivalent to the annual greenhouse gas emissions generated by 2,300 passenger cars or in the operation of 1,000 average-sized U.S. homes.
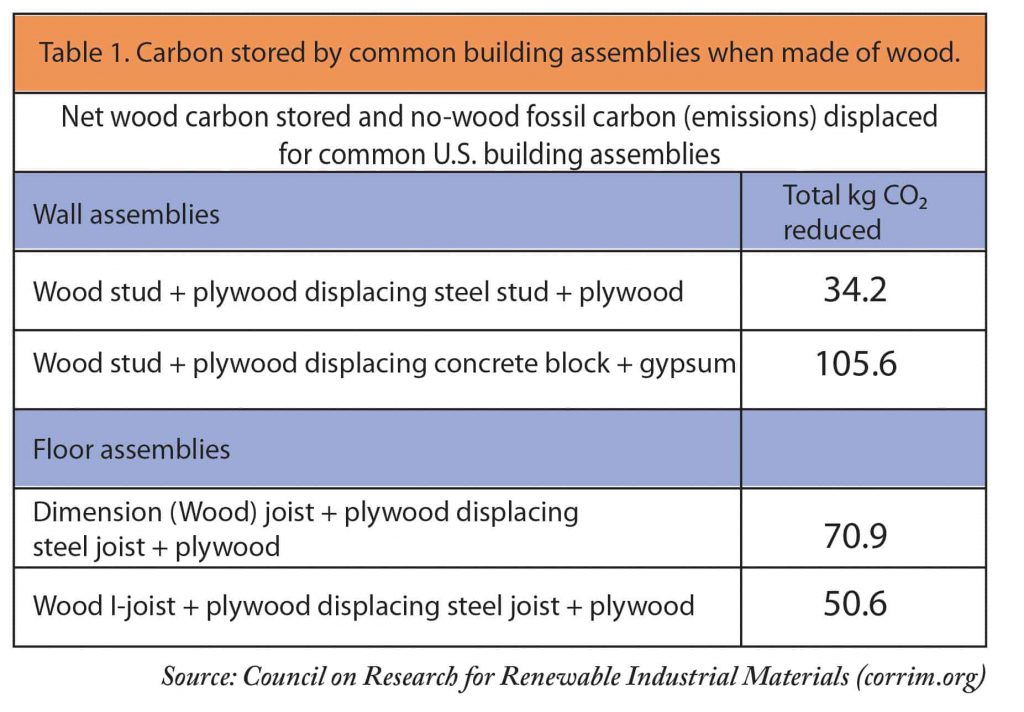
Wood Products also use Significantly Less Fossil Fuels to Produce than Concrete and Steel
Manufacturing wood into lumber and engineered wood products requires far less energy than other construction materials, and most of the energy used to fuel manufacturing comes from renewable biomass. While manufacturing typically accounts for the largest proportion of embodied energy and emissions associated with the life cycle of any building product, it is also an area where wood consistently outperforms steel and concrete.
For lumber, processing is straightforward – bark is removed, logs are sawn, edges are trimmed, lumber is cut to desired lengths, dried, and then planed. Manufacturing engineered wood products requires more processing to achieve structural performance requirements, which requires more energy. For example, glued laminated posts and beams are bonded with durable, moisture-resistant adhesives – however, embodied energy associated with engineered wood products are still significantly lower than steel or concrete. In the lumber industries’ quest to reduce waste and increase efficiency, state of the art processing equipment has helped create an industry where waste is an almost obsolete term. Remaining sawdust and bark are used to fuel the processing operations. According to Dovetail Partners Inc, which provides information about the impacts and trade-offs of environmental decisions, the North American lumber industry is 50-60% energy self-sufficient.
Comparatively, the global steel sector has a massive carbon footprint, contributing more than 10% of global carbon dioxide emissions. Manufacturing virgin steel from iron ore is energy intensive. Basic oxygen furnaces (BOFs), the norm in most developing countries, require coke—a purified version of coal—to extract the iron from the ore and alloy it with carbon. The result, pig iron, is then refined into mild steel, which incorporates about 25% recycled iron and steel scrap. Manufacturers are experimenting with ways to replace coal and coke with non-fossil agents like hydrogen and electrolysis in BOF mills, yet the industry remains largely dependent upon greenhouse gas-producing fuel in its manufacturing processes. The American Institute of Steel Construction does estimate that 98% of structural steel from demolished buildings is recovered and recycled into new steel products, which is a more resource-efficient material than virgin steel.
A five-story wood building stores 3,970 metric tons of carbon dioxide. Combined, this is equivalent to the annual greenhouse gas emissions generated by 2,300 passenger cars.
Concrete, the world’s most widely used construction material, contributes 6-11% of global carbon dioxide emissions. Most of those emissions come from the production of its binder, Portland cement, which comprises about 10% of the concrete mix by weight, on average. Producing aggregate—sand and crushed rock, which may constitute 70% to 80% of the mix, on average—also requires energy, but much less so. Sand mining can damage river and coastal ecosystems.
When comparing the embodied effects of wood, steel, and recycled steel a second study compared two post and beam systems built of wood and steel. The study also modeled a recycled steel building. While recycled steel manufacturing requires approximately half the energy as it does to refine virgin steel from iron ore, recycling still uses considerably more energy than is required to manufacture wood products. As shown in Figure 1, wood is superior to virgin steel in all categories and to modeled recycled steel in all categories except air pollution and resource use.
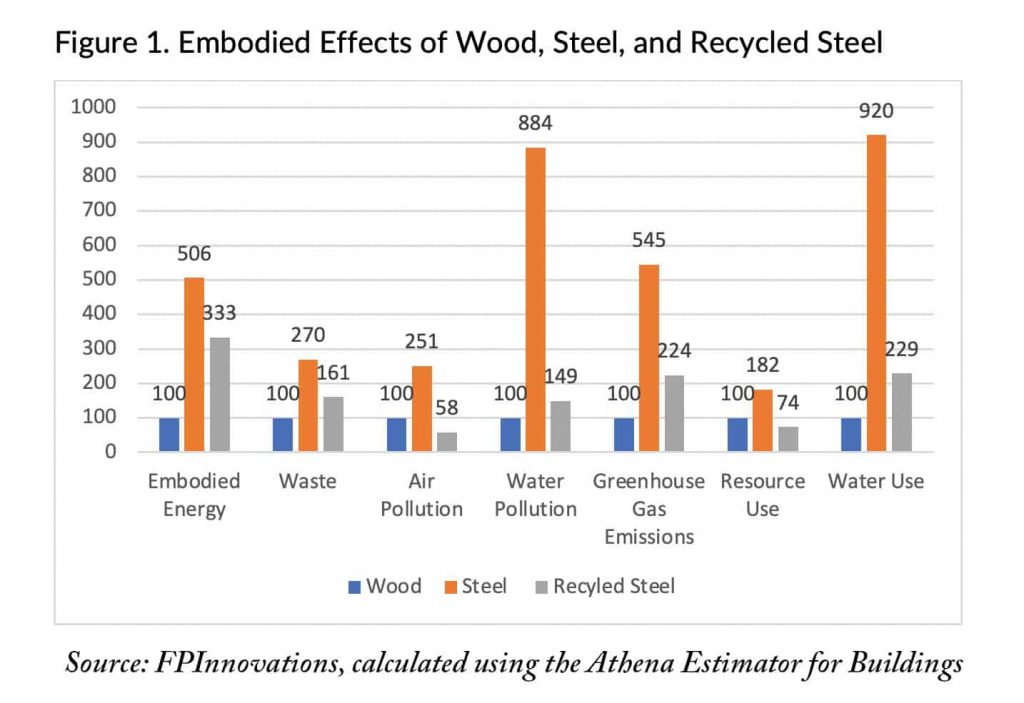
As global leaders and end users look for ways to reduce greenhouse gas emissions and select building materials that are good for the environment, forest products grown in sustainably managed forests offer a solution.