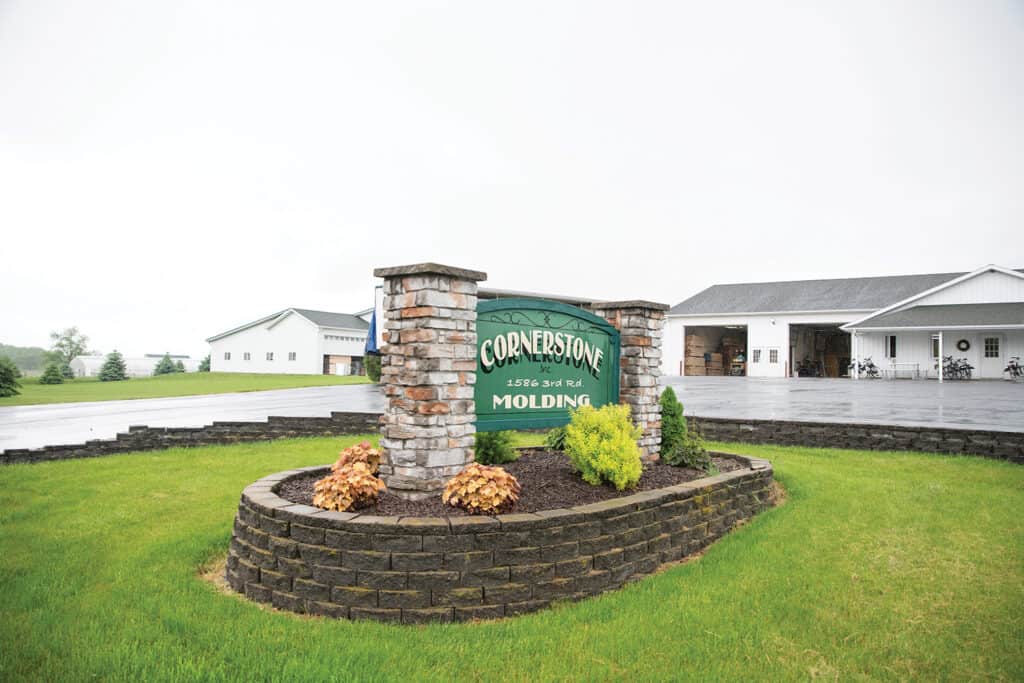
Photos by Cari Clark Photography
“When you run a clean operation, you get a quality product. It’s as simple as that. We strive on cleanliness and first impressions. We specialize in on-time delivery and, if the customer is expecting to pick it up, it’s ready when they get here. We try not to carry back orders; we always try to get the best quality wood so that we can have a good finished product offering.”
Daryl Yoder, Vice President and General Manager, Cornerstone Moulding Inc.
Bremen, IN–Cornerstone Moulding Inc., based here, manufactures residential mouldings and serves both the RV and cabinet manufacturing industries. The company purchases approximately 1.3 million board feet annually of Hard and Soft Maple, Red Oak and Poplar in 4/4 and 5/4 thicknesses (No. 1 Common and Better).
The company was established in 2004 by President Eddie Ray Borkholder and Vice President and General Manager Daryl Yoder. The two men saw a need for a moulding operation in their area and decided to fulfill it. “My brother-in-law Eddie Ray and myself had no prior experience in moulding and we met some challenges along the way,” Yoder explained. “We had to learn the trade from top to bottom. We knew if we learned the trade, the rest would come, and it did. Our father-in-law had moulding experience and he helped us get the company started by sharing his knowledge. We took training on the moulding end and had a technician from Weinig come down and teach us how to use the moulders. We’ve reinvested over the time we’ve been in business and we’ve seen positive results every time.” A family owned and operated business, Yoder said the brother-in-laws added a third brother-in-law to the team in 2006 when Sales and Customer Service Manager Fred Miller came aboard.
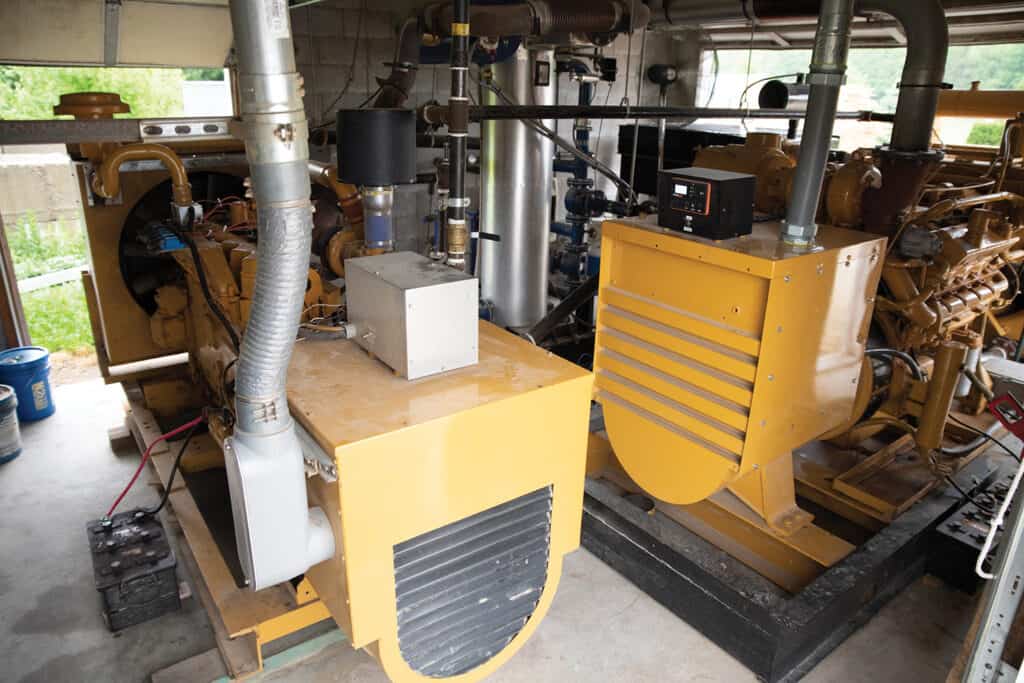
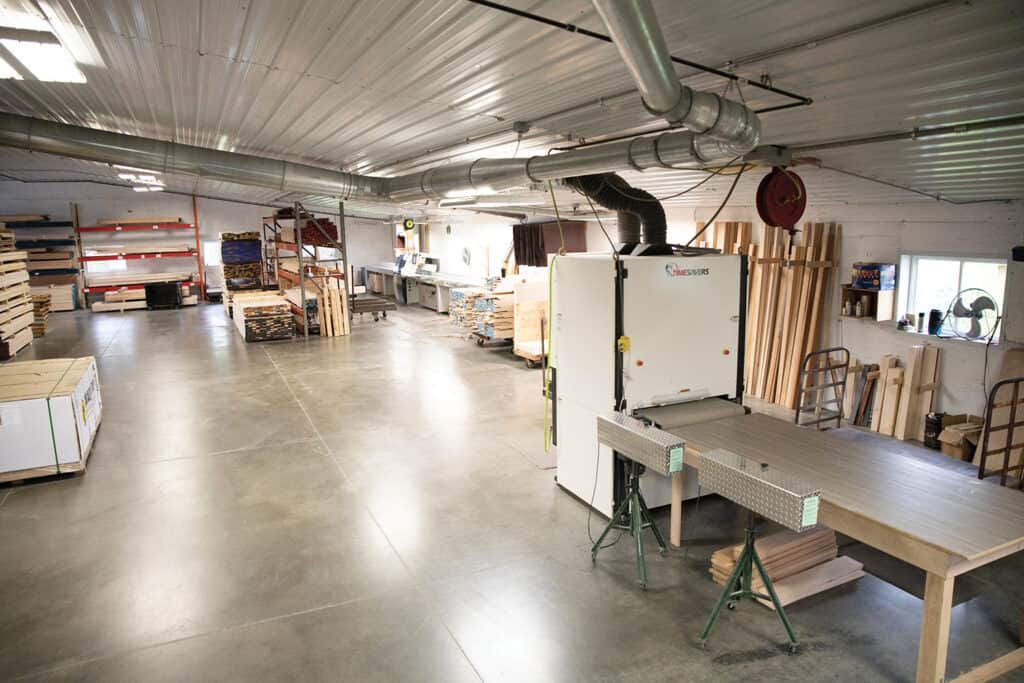
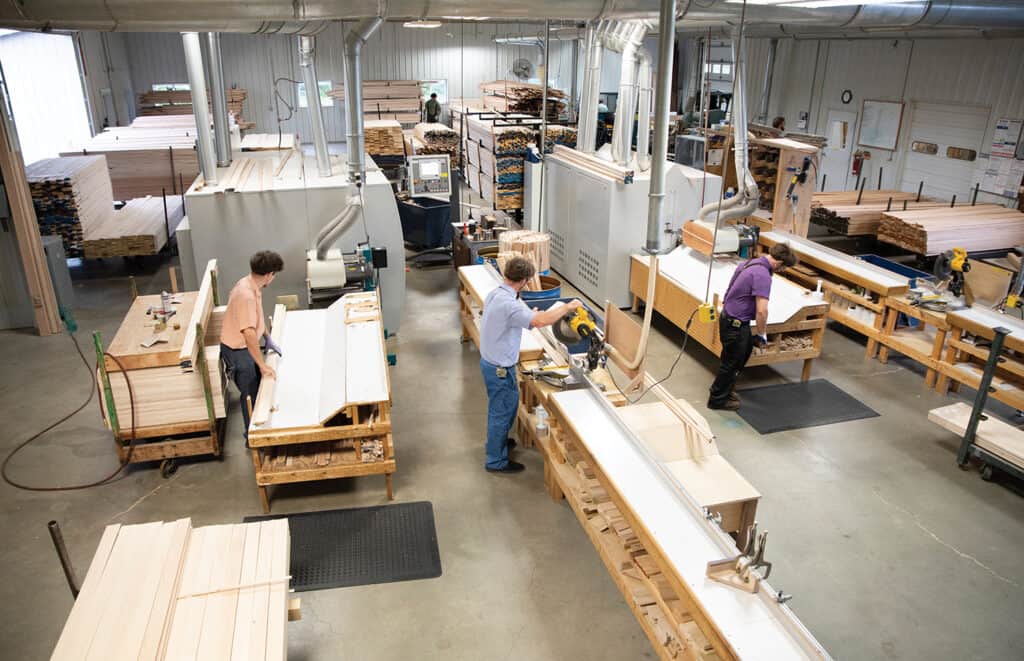
From a 31,000-square-foot facility, Cornerstone Moulding Inc. continues to reinvest in equipment to improve the manufacturing process. Yoder explained, “We started with an Ogam gang rip saw and we upgraded in 2007 with a Raimann rip saw with a movable blade. By 2015, we replaced that gang rip with another Raimann rip with two variable blades. We upgraded our moulders to a faster pace. We began with one Unimat Gold moulder and we added a second Unimat Gold in 2012. By 2016 we replaced the first Unimat with a Weinig P1200, which is twice as fast.”
Yoder said Cornerstone Moulding rips about 6,000 board-feet per day. “Six thousand feet is about an average day,” he continued. “We rip it and we mould it and then it goes into bundles and goes into the finish room where it gets hand-selected for orders. We do all orders on a day-by-day basis. After it gets finished or painted it goes into our drying tunnel, and after it comes out of the drying tunnel it goes into shipping and gets boxed. The packages are then put on skids and loaded into semi-trailers for shipment.”
The people at Cornerstone work diligently with precise attention to detail on each part of the process. Yoder said, “No single part of the process is overlooked. Our goal is to maintain excellence, quality and consistency for every order, every time. We keep operations clean and we move orders on a daily basis. Orders are processed immediately and ready for shipment or pick-up as soon as the next day or in some cases the same day, depending on the job.”
Yoder said the entire operation is powered by natural gas generators. “We have a 300kw generator, and we do all of our heating off the exhaust. The exhaust goes through a heat exchanger and it heats the water and, in exchange, we’re heating the entire complex for about $12 an hour for heat and electric combined. We’re very efficient in our energy and the resources that we utilize.”
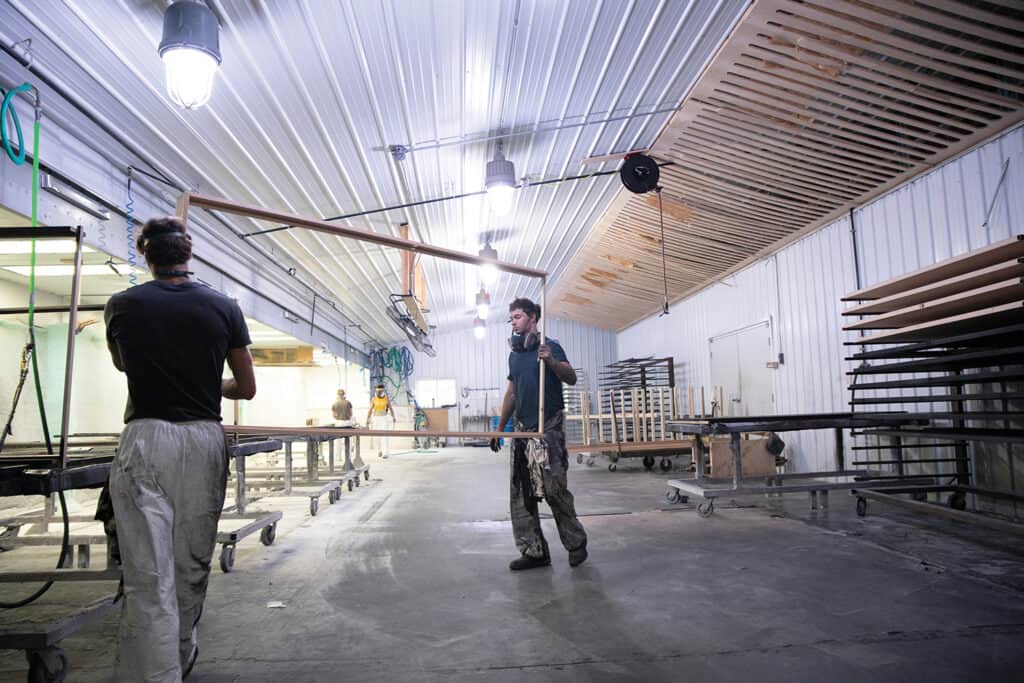
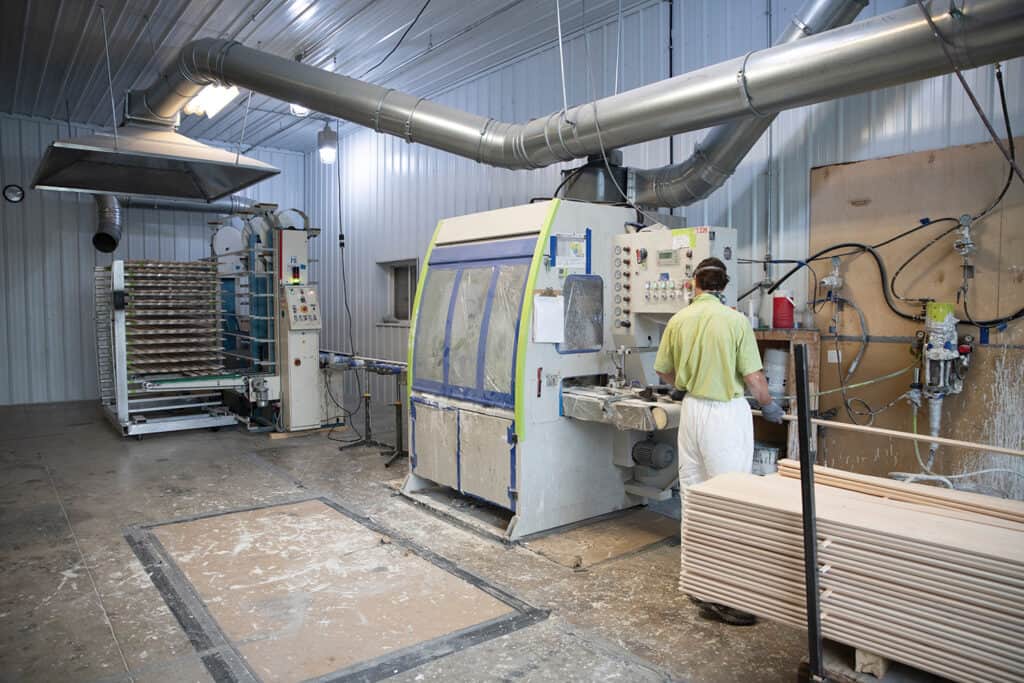
Cornerstone Moulding products can be found in some interesting places. Yoder said that while the installation was done by another company, Cornerstone Moulding’s products are in Notre Dame. “One of the most unusual requests that we have fulfilled was manufacturing rafters for looks alone.”
When asked about the various species utilized, Yoder said Cornerstone’s business previously consisted of mostly Oak products. “When we started in 2004 everything requested was mostly Oak,” he explained. “We’ve seen a turn in the market and now we are leaning heavily to the Maple’s. In 2019 we started running Hard Maple because Soft Maple wasn’t readily available.”
With a focus on quality, service and consistency, Yoder said one of the things their customers recommend Cornerstone Moulding for is their cleanliness. “When you run a clean operation, you get a quality product,” he explained. “It’s as simple as that. We strive on cleanliness and first impressions. We specialize in on-time delivery and, if the customer is expecting to pick it up, it’s ready when they get here. We try not to carry back orders; we always try to get the best quality wood so that we can have a good finished product offering.”
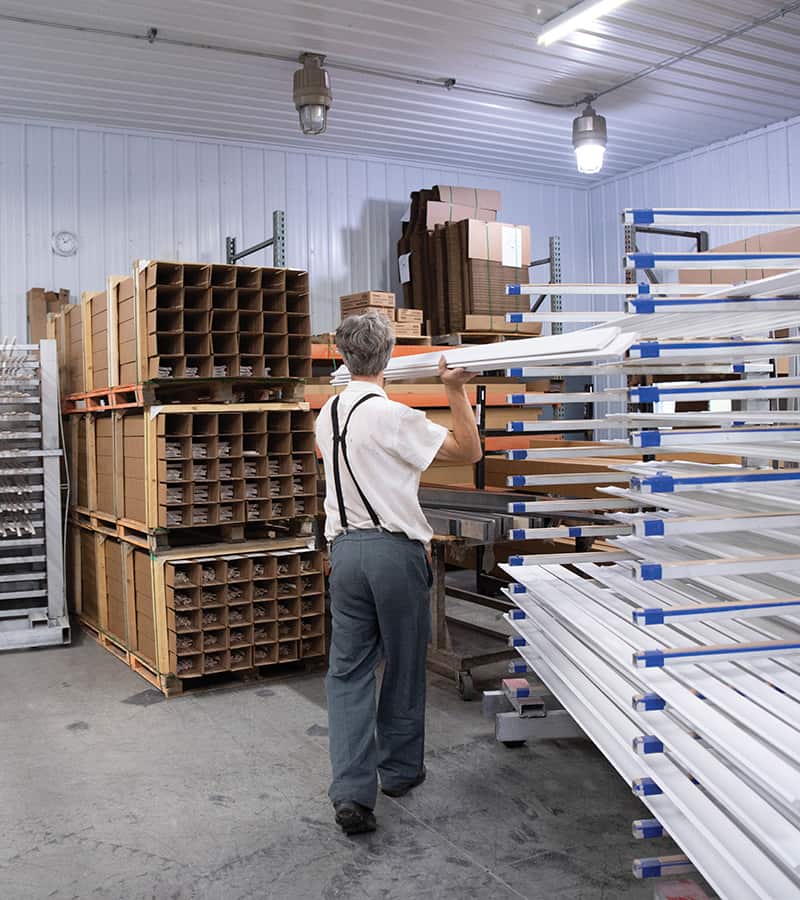
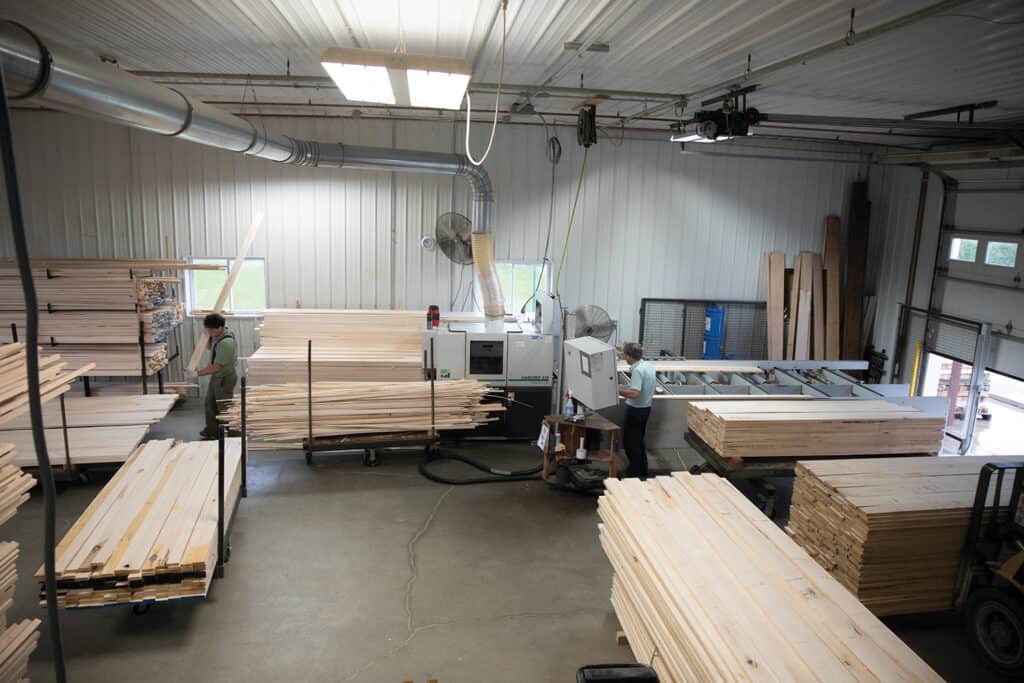
With 23 full-time employees, key personnel include President Eddie Ray Borkholder; Vice President and General Manager Daryl Yoder; and Sales and Customer Service Manager Fred Miller. Wyman Hochstetler, John Troyer and Jose Borkholder all have leadership positions that make it all happen along with the rest of the company’s dependable workforce.
The company would also like to thank their lumber suppliers and vendors for stepping forward and supplying them with a quality product at a fair price and serving with integrity at a time when things seemed out of control this past year.
For more information, contact Daryl Yoder at 574-546-4249 or FAX: 574-546-4211.