Hattiesburg, MS–Rainey Millworks LLC, based here, manufactures architectural casework, cabinetry and mouldings. Over 100,000 board feet of Oak, Poplar, Cypress and Maple are purchased each year in FAS grade, 4/4, 6/4 and 8/4 thicknesses. Sapele from Africa is also regularly purchased by the company.
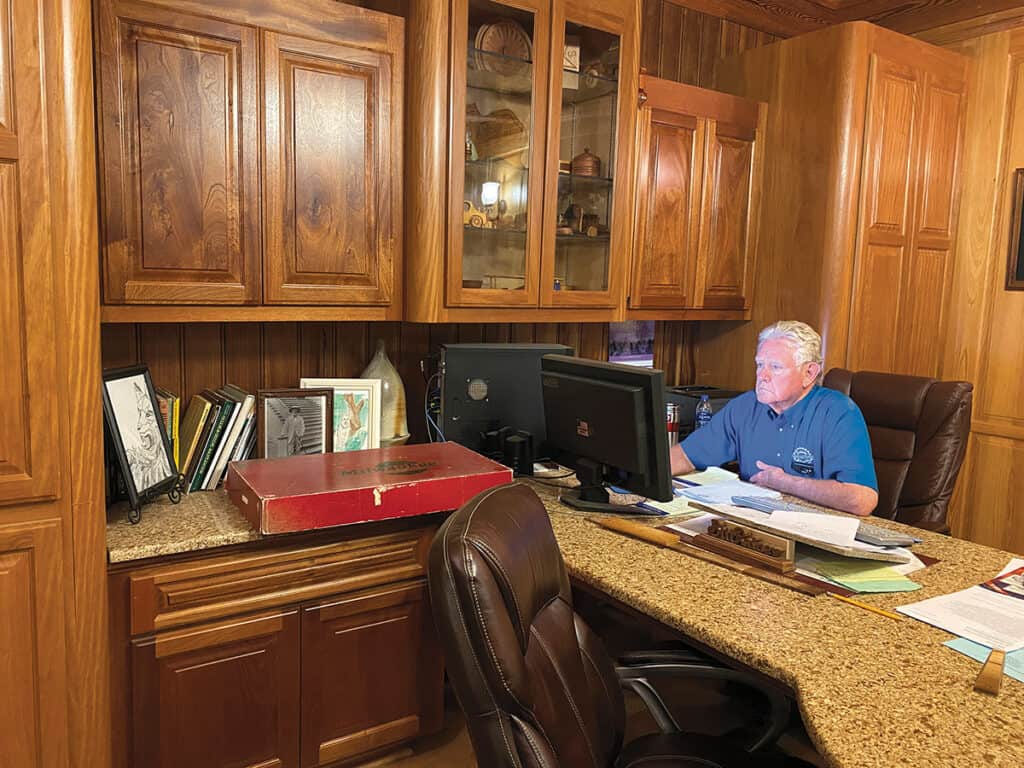
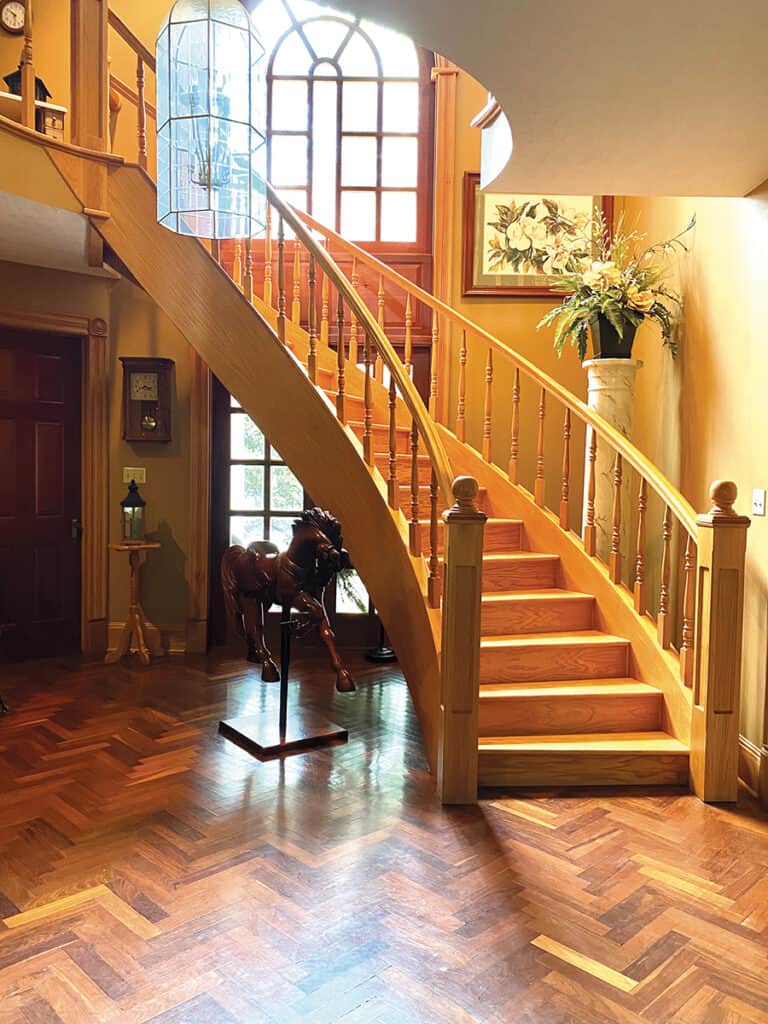
Rainey Millworks purchases mostly random widths with 14- to 16-foot lengths being predominant. Owner Bill Rainey said he primarily uses four-, six- and eight-quarter thicknesses. “We purchase lumber already kiln-dried, but in the rough so the lumber can be edged and planed using a CNC machine and 12-inch and 8-inch Weinig moulders,” he stated.
Approaching its 40th year as a manufacturer of custom cabinets and millwork, Rainey said quality workmanship and taking on projects other companies can’t do contribute to reaching this milestone. “We operate under a principle of taking on the projects that few other manufacturers can handle,” he explained.
Among specialty products are arched baseboards and crown mouldings, arched-top windows and doors and curved staircases. Rainey explained, “We do what nobody else can or will do. This includes a lot of radius millwork products. At Rainey Millworks, we pride ourselves on quality workmanship and customer satisfaction. Whether it’s custom cabinetry, doors or staircases, we can design, fabricate and deliver to customer specifications.”
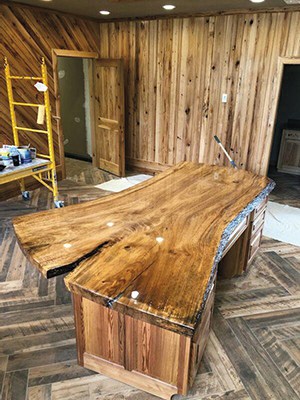
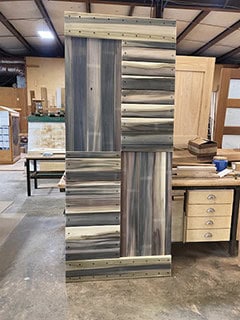
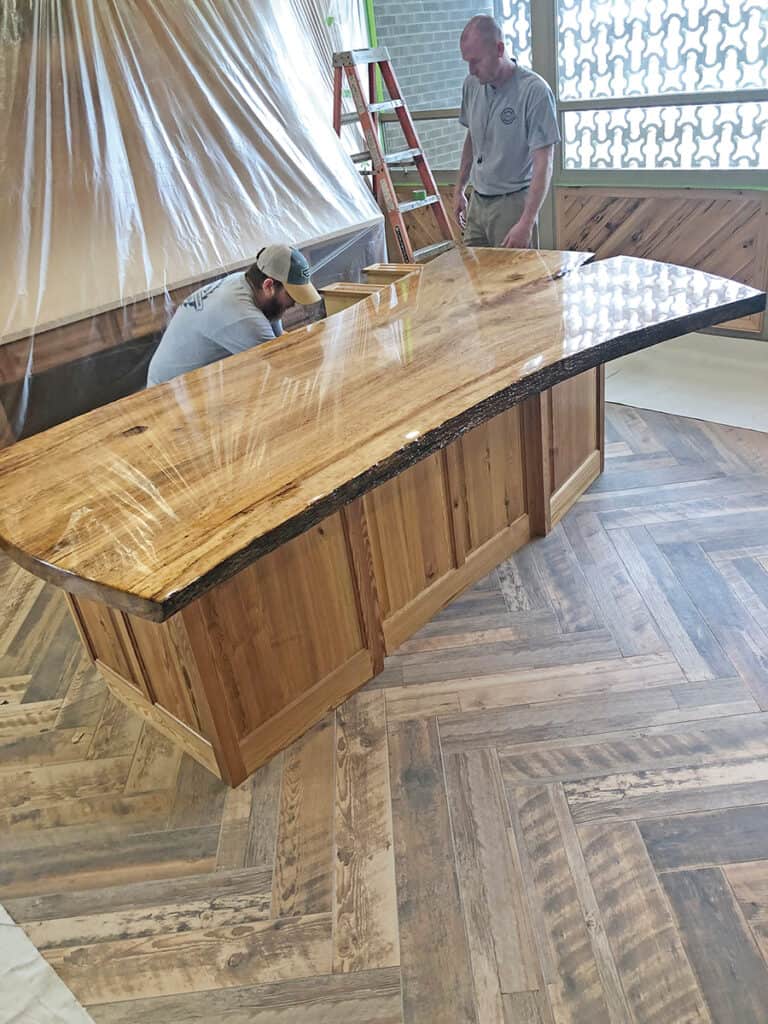
Rainey Millworks has grown since the early beginnings in 1984 when it was Rainey and one other man in a 1,200-square-foot building. Currently 12 employees work at the 24,000-square-foot facility, which consists of two buildings. “For a custom shop, that’s a good size,” Rainey noted. “The majority of our team members are craftsmen who have a particular skill they bring to the table. Each one of them can do two or three different things really well, though, which helps us better serve our customers. The goal here has always been quality, not quantity.”
Rainey’s sons, Darrell and Steve, became partners in the company as time went on. Rainey primarily handles sales, while Darrell runs the CNC machine and Steve operates the moulding machine. “They run the shop. I run the roads,” Rainey said. You’ll find him out of town calling on potential clients about 40 to 50 percent of the time.
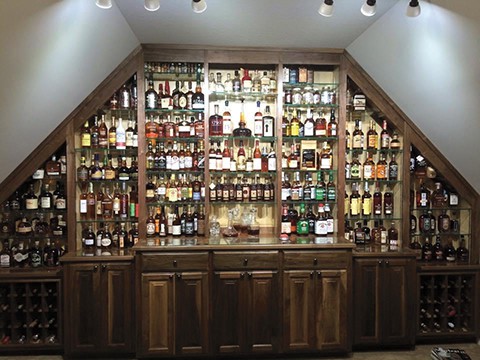
As for which species he prefers for specific millwork, Rainey said, “Imported lumber is mainly used for exteriors, and Maple is preferred for cabinets and cabinet doors.” Rainey said the reason for this decision is that Maple is harder and more stable than Poplar. “There’s not enough difference in price to justify a door possibly warping,” he explained. “Oak is used for cabinets, flooring and doors, while Poplar is favored for mouldings, baseboards and door trim. Oak is a good, stainable clear-cut wood. Poplar takes paint better and also handles machining better.” Rainey uses Sapele because it has the same rich reddish-brown hue as Mahogany, but is more easily available. “Today’s plantation-grown Mahogany doesn’t have the same rich red color that the native Mahogany does,” Rainey explained. “It’s more of a pale pink.”
Rainey said most of the millwork is sold to builders mainly in the Southeastern United States, with Rainey Millworks installing most cabinets and delivering the other products to the job sites. But there have been some exceptions to the rule. “Our cabinets, a kitchen island and countertops were installed inside a house in Edmonton, AB. Maple, Sapele and White Oak were the Hardwoods of choice for that job,” said Rainey.
Rainey Millworks’ products can be found in some unique places. One project that Rainey is proud of is a wine room that was crafted for a customer in Bay St. Louis, MS. Up to 1,700 wine bottles can be held by the 12-foot-tall shelves that are reachable by a 7-foot-tall library ladder that rolls around the room. Also notable is a pair of curved Oak staircases that were crafted for the mother of the late NFL great Steve McNair. A Birdseye Elm slab was transformed into a desktop for another customer.
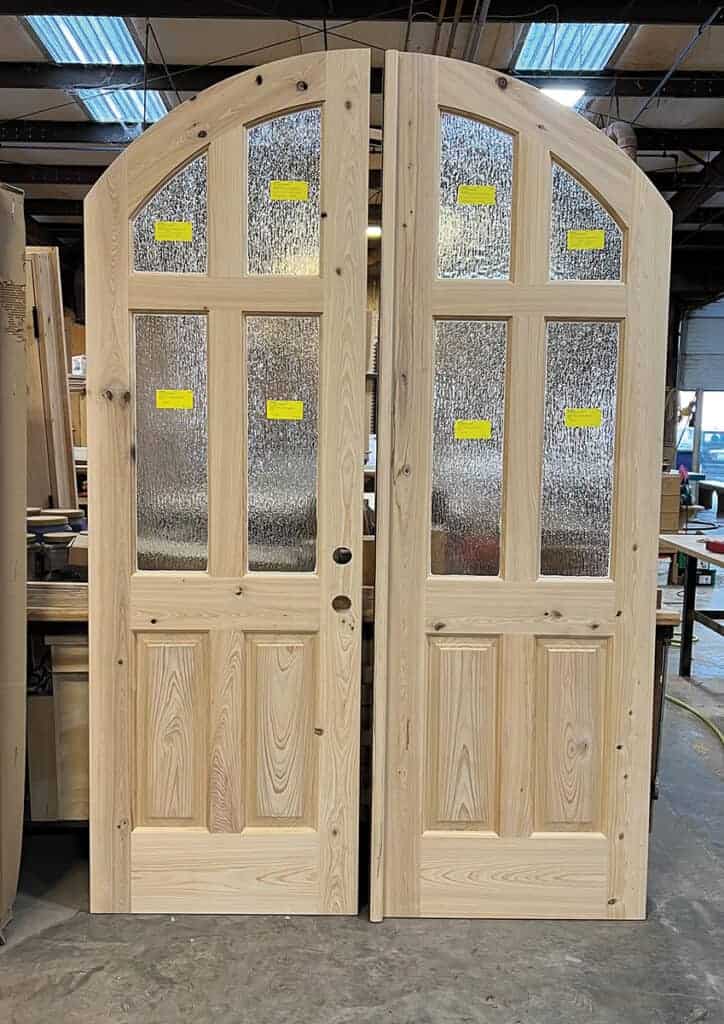

Rainey founded the operation after spending his childhood learning about the construction industry from his father, who was a general contractor. Rainey spent summers helping his dad on construction sites whenever a subcontractor needed a helper or when the crew was short-staffed for laborers. He learned roofing, bricklaying and drywall installation among other skills. The early training helped Rainey decide he wanted to be involved in the industry. Gaining experience in many segments of the industry, he said, “Building and installing cabinets and millwork is like the Cadillac of jobs in this industry. You’re never out in the sun and you never get rained on.”
For more information visit www.raineymillworks.com.