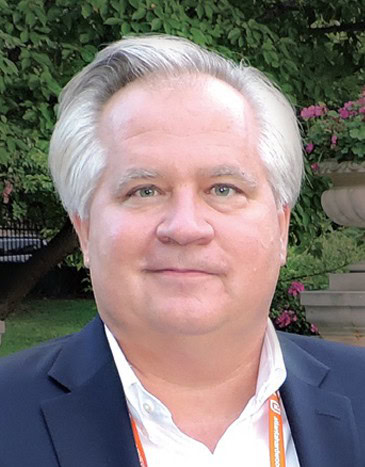
Executive Director
American Hardwood Export Council
Sterling, VA 703-435-2900
www.ahec.org
The seven-story structure, commissioned by commercial real estate firm The Office Group (TOG), lays out a roadmap for the office environment of today. In fact, architects Waugh Thistleton (WTA) say it demonstrates how all buildings of its type and scale could and should now be constructed. The focus is on combining technical performance, environmental ethos and functionality, while taking into account the changing way people are living and working and perceiving the workplace.
Well-being lies at the heart of the design. It’s about the materials used; what they are – predominantly bio-based – their aesthetic, how they’re perceived and how they make occupants feel. From the façade to the interiors, these are not just individual components of the building – they ARE the building. And structurally it’s an entirely wood solution.
The key structural elements include a CLT core, floor and wall panels, plus the glulam frame for the façades.
An eye-catching feature externally – and key contributor to the building’s energy performance – are the brise soleil fins in thermally-modified American Tulipwood. These are individually shaped using parametric modelling and are vertically or horizontally mounted according to the angle at which the sun strikes the building through the day. So they help maximize the building’s use of natural light, but break it up and control energy gain, minimizing the need for non-recyclable solar control coating on windows.
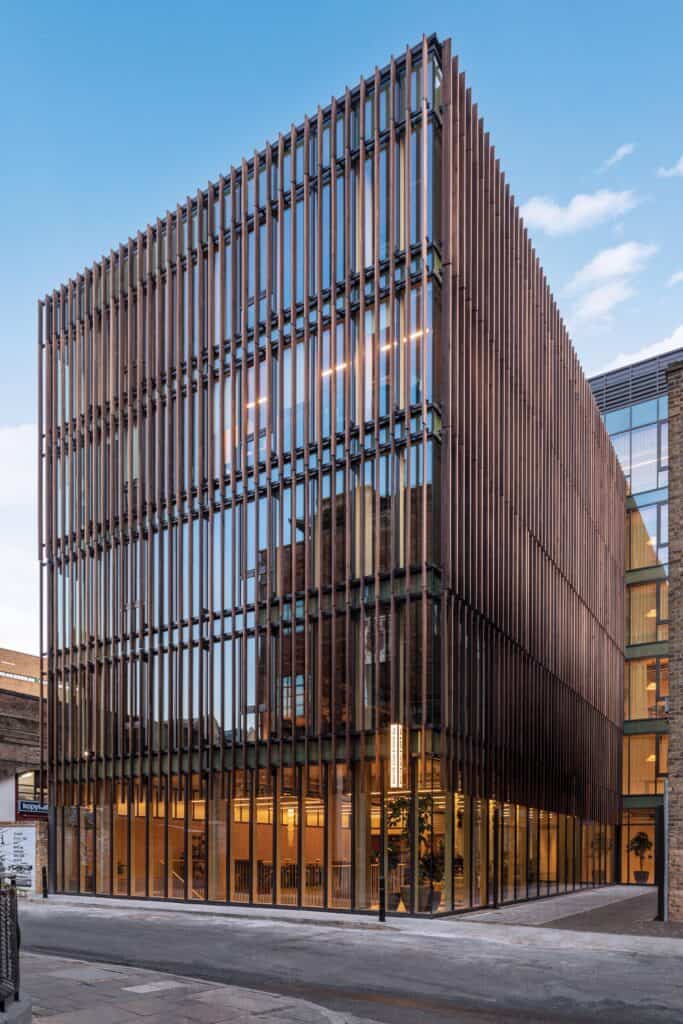
AHEC worked with Waugh Thistleton in a technical advisory role on the specification of Tulipwood. It was chosen due to its technical performance and sustainability, with the species comprising 7 percent of the overall U.S. hardwood forest. It has not been widely used thermo-treated, but where it has, such as in the Maggie’s Centre in Oldham and playground structures at Chisenhale school in London, it’s been shown to be durable, strong and stable in exterior use. AHEC-commissioned tests also showed it takes fire retardant treatment well.
Architect Andrew Waugh comments “on use of hardwood, we’d never specify one that is endangered or clearly unsustainably forested. But when it came to using U.S. Tulipwood for the Black and White building’s solar control louvres our collaborators at the American Hardwood Export Council explained that it’s in oversupply; growing faster than it can be harvested. So here we have a hardwood which is sustainable and suited to external applications.
We should consider the best solution for every use case. In this scenario, with this species, for this location on the building, a hardwood is the correct solution.”
AHEC EU Director David Venables adds, “the louvres cover approximately 40 percent of the elevation on a typical floor and we believe this is the largest installation of thermally modified Tulipwood as a façade anywhere. We think it can be very significant in helping define a viable new use for Tulipwood and Waugh Thistleton have a number of live and pending projects in North America, so we’ll continue to highlight the potential of the material.”
The end result is a structure comprising 1,330m3 of timber – including two containerloads of Tulipwood – that stores 1,014.7 tonnes of C02 and delivers a carbon emission saving over an equivalent concrete build of 37 percent.
It also works for the client – significantly it’s TOG’s first purpose-built office project – and it should be taken on board by planners as the way to build a successful, sustainable, safe workspace.