Industry News – March 2025
Mike Schulke Joins Granite Valley Products
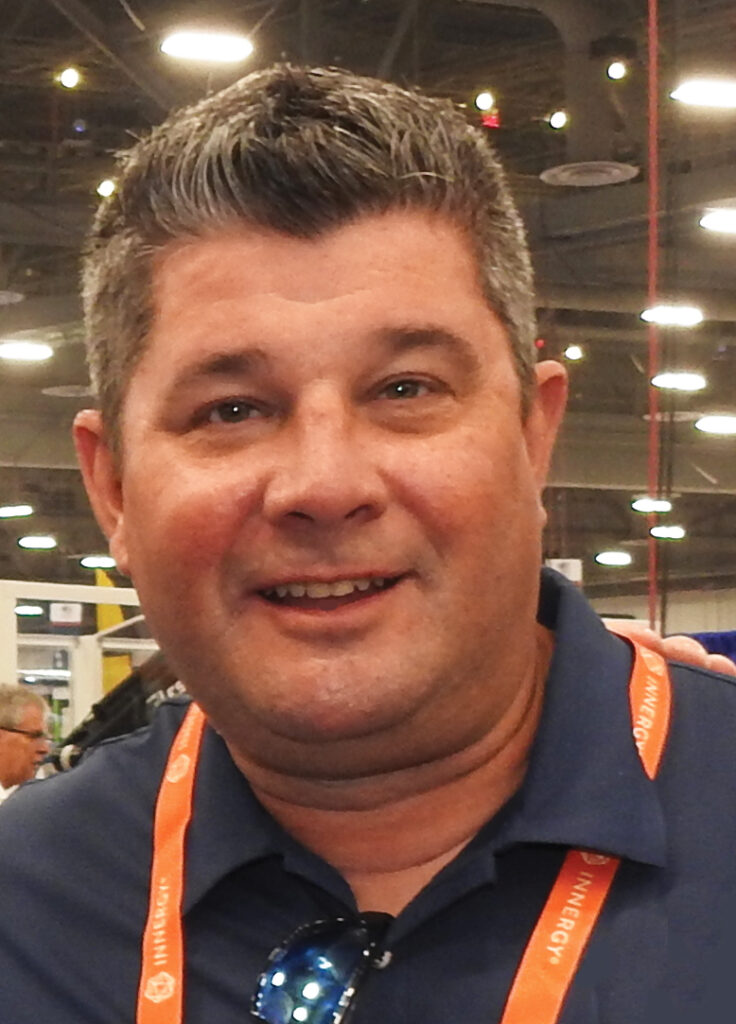
Granite Valley Forest Products, located in New London, WI, recently welcomed Mike Schulke to their sales/purchasing team. With over two decades of experience in the hardwood and lumber industry, Schulke brings his expertise and a customer-focused approach to the team.
Schulke began his career in the lumber industry in 2004 as a lumber grader after earning a vocational degree in NHLA Grading Rules. Over the years, he has held various roles in sales and management, contributing to business growth and strong client relationships. Most recently, Schulke served as sales manager at Tigerton Lumber Co., where he worked on strategic plans and expanded market opportunities. He also worked for Ort Lumber Inc., Wolf River Lumber Inc., Flambeau Inc. and Derby Plastics Ltd.
Schulke holds an associate’s degree in marketing from Fox Valley Technical College and a Plastics Technician Degree from Milwaukee Area Technical College, alongside his NHLA certification.
In his new role, according to a statement from the company, Schulke will focus on strengthening client relationships, enhancing sales strategies and supporting Granite Valley’s commitment to offering the best kiln-dried hardwood lumber to its valued customers.
“I’m excited to join Granite Valley Forest Products and contribute to their ongoing success,” said Schulke.
Outside of work, Schulke is a board member of the Wood Products Manufacturers Association and the Great Lakes Kiln Drying Association. He enjoys skiing, golfing and traveling with his wife, Tina.
For more information, visit www.granitevalley.com.
Roy Anderson Lumber Company, Inc. Installed New AI Grading Solution
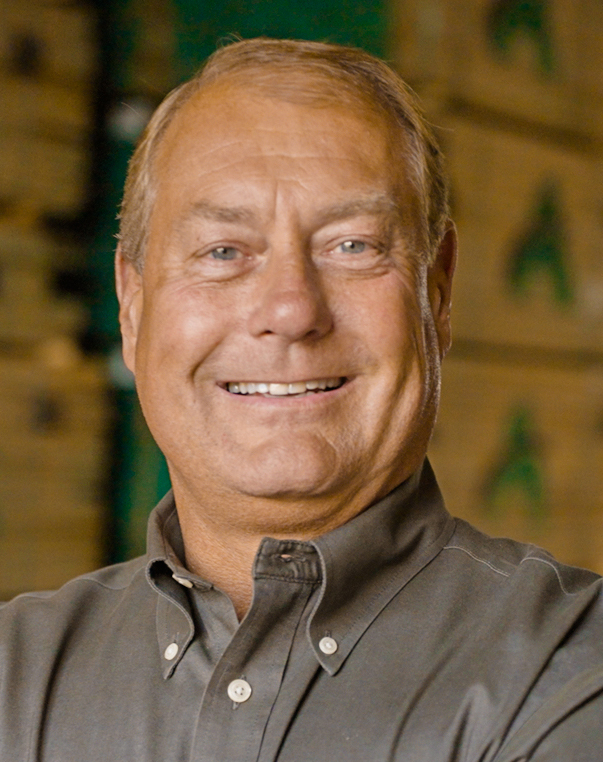
Roy Anderson Lumber Company, Inc., located in Tompkinsville, KY, recently installed a new AI Grading Solution.
Roy Anderson Lumber Company produces 50 million board feet of green and kiln-dried hardwood lumber. They offer their customers rough, straight-line ripped and reclaimed lumber, as well as cross ties, pallet cants, mulch, chips and dust.
“Through our partnership with Neural Grader, we will be implementing a new grading solution at our green sorter over the next several months with the new AI Grading Solution,” said David Anderson, owner of Roy Anderson Lumber Company. The AI Grading Solution will allow Roy Anderson Lumber Company to increase their throughput at their green sorter.
Roy Anderson Lumber Company is also finalizing the addition of a new sawmill, which they plan to be fully operational in 2025. They anticipate that this will add between 7 and 10 million board feet to their production capacity.
Roy Anderson Lumber Company, Inc. was founded in 1950 by Roy Anderson. The company operates two facilities in Tompkinsville, KY, and Eubank, KY, and supplies customers both domestically and internationally.
For more information, visit www.ralumber.com.
Cleereman Makes Installation At Westbury Lumber
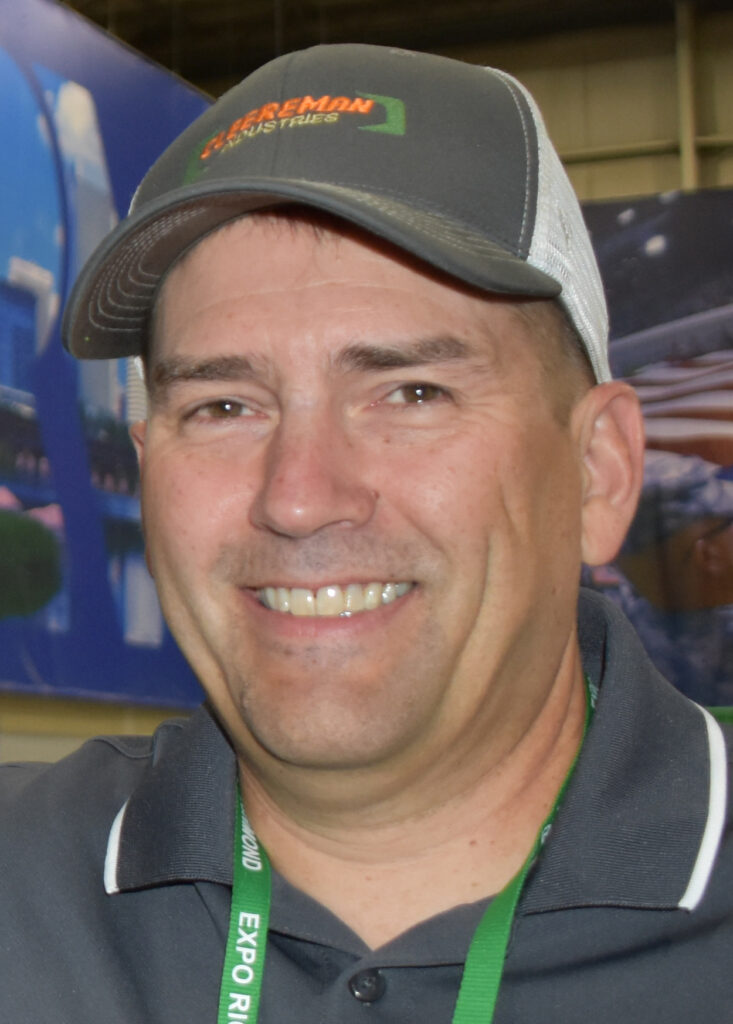
Cleereman Industries, located in Newald, WI, recently made installations at Westbury Lumber in Red Creek, NY.
Jason Smith of Westbury Lumber oversaw the new installations at the sawmill. Smith purchased a Cleereman LP-42 Lumber-Pro carriage along with a Cleereman Controls 3-D Scanning system.
Cleereman Industries sent four technicians out to remove the old carriage and install the new LP-42 Lumber-Pro carriage.
This project started on Monday morning and had everything ready to go on Thursday afternoon. Cleereman Controls engineers showed up on Thursday afternoon and commissioned the new 3-D Scanning system and the mill dispatching. The mill was ready to run production the following Monday morning.
Dan Tooke a senior engineer from Cleereman Controls did sawyer training. According to Smith the new scanning system has greatly increased his production and the yield out of his logs.
For more information, visit www.cleereman.com.
Comact Introduces Hybrid Sawline
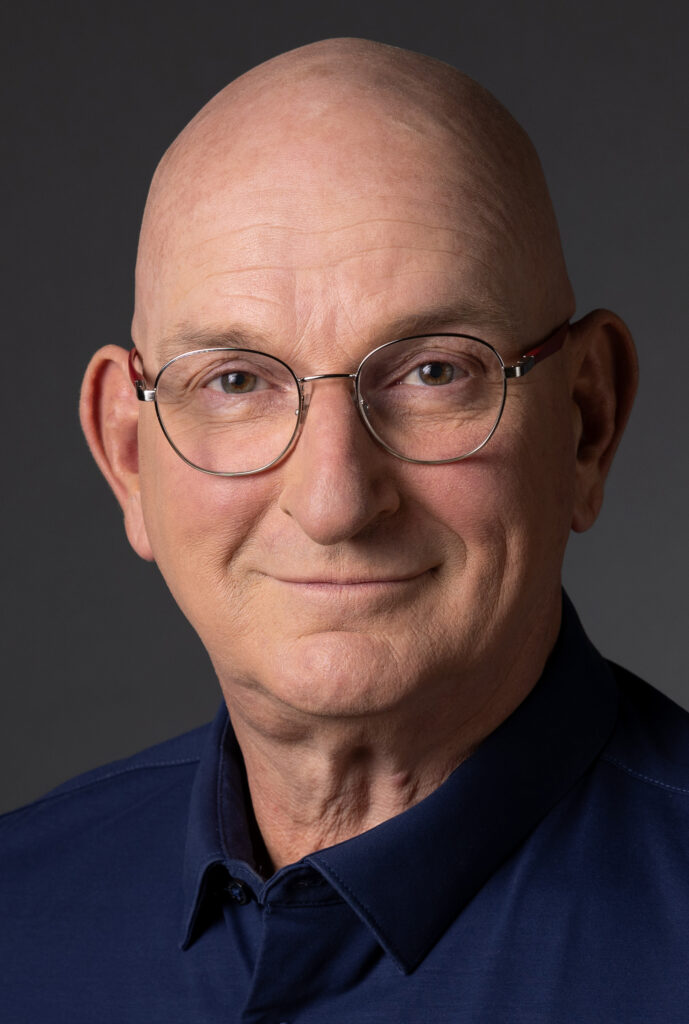
Comact, a global leader in wood processing solutions, proudly announced the launch of its new hybrid sawline. The hybrid sawline combines circular saws, bandsaws and advanced smart technologies, the system sets a new benchmark for speed, flexibility and operational efficiency in handling a wide range of log diameters.
Comact’s hybrid sawline is a transformative solution, particularly for Southern USA mills, where a broad range of log diameters and highly flexible operations are critical to maximizing results. The sawline’s ability to seamlessly integrate multiple cutting modes including double profiling, quadruple circular cutting, and sideboards splitting—enables mills to produce diverse lumber products on a single line, optimizing recovery and reducing costs.
“We strongly believe that this new sawline design will be a game changer, especially for our Southern USA customers,” said Simon Potvin, Comact’s president and CEO. “These mills face unique challenges in processing a wide range of log diameters. The new hybrid sawline provides the flexibility to handle all log sizes on a single line.”
The hybrid sawline is further strengthened by Comact’s Smart Vision system, powered by artificial intelligence. This advanced technology optimizes log feeding to ensure a smooth and consistent production flow. Complementary features like the Primary Breakdown Closed Loop Smart Tool enhance precision and value recovery, offering sawmills greater efficiency and automated quality control.
The introduction of the hybrid sawline underscores Comact’s commitment to driving progress in the wood processing industry. This launch reflects a century-long dedication to providing solutions that empower sawmills to overcome challenges and achieve sustainable growth.
For over 100 years, Comact has been a leading OEM in high-caliber wood processing equipment, digital technologies, cutting solutions, project services and aftermarket support.
For more information, visit www.comact.com.
PLM Introduces New Leadership
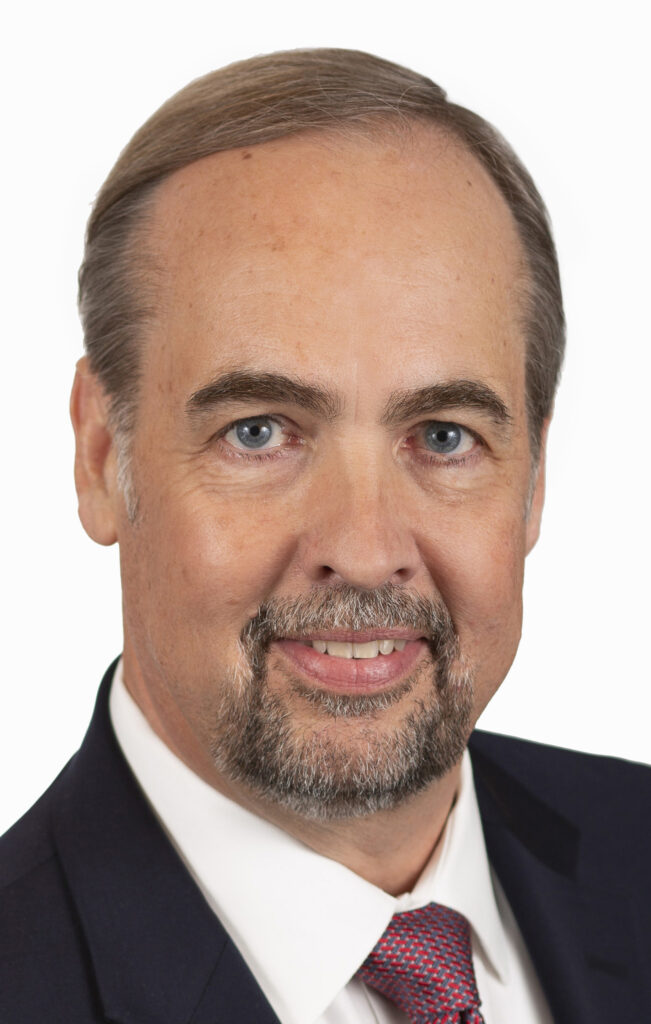
Pennsylvania Lumbermens Mutual Insurance Company (PLM), the largest mutual insurer dedicated to wood-related businesses, announced several leadership changes and promotions within the company’s executive staff. The changes are part of PLM’s strategy to enhance the organization’s profitability and growth and prepare for the future, while recognizing the changing complexity of the business of insurance.
A PLM veteran for more than two decades, Steve Firko, chartered property casualty underwriter (CPCU), will assume the role of executive vice president (EVP) and chief operating officer (COO) overseeing all front-line customer-focused operating departments including underwriting, field operations, claims, loss control, marketing, customer service and operations as PLM continues to evolve to meet the market demands of the future.
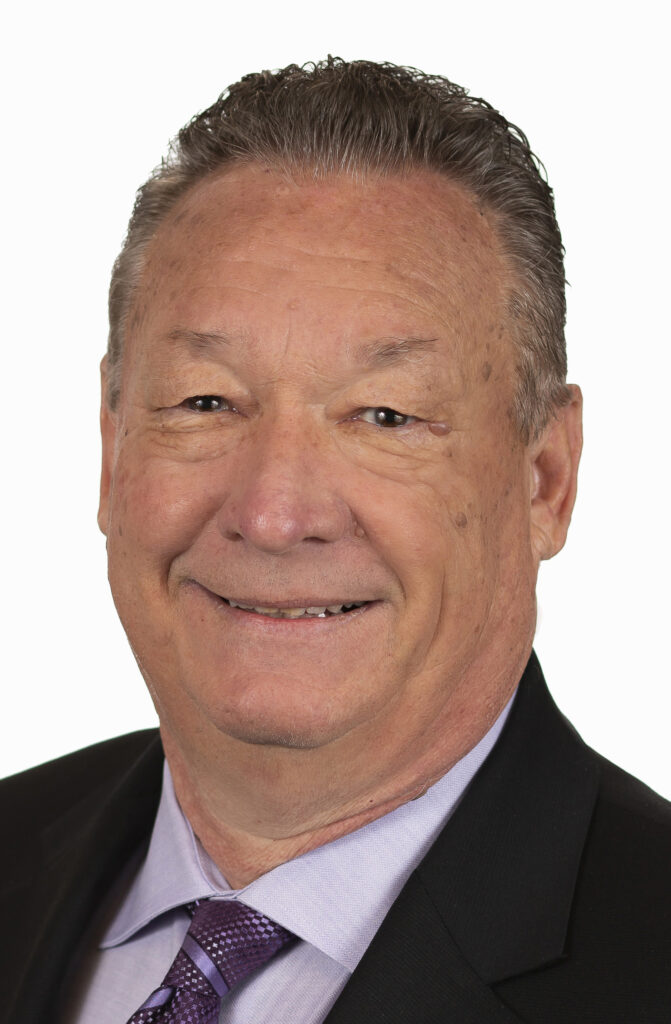
Firko most recently served as senior vice president (SVP) of business development, loss control and customer service at PLM. His notable career spans nearly 40 years in the industry, including professional and management-level positions at several multinational insurance companies, and board and committee responsibilities at the Pennsylvania Association of Mutual Insurance Companies and the National Association of Mutual Insurance Companies.
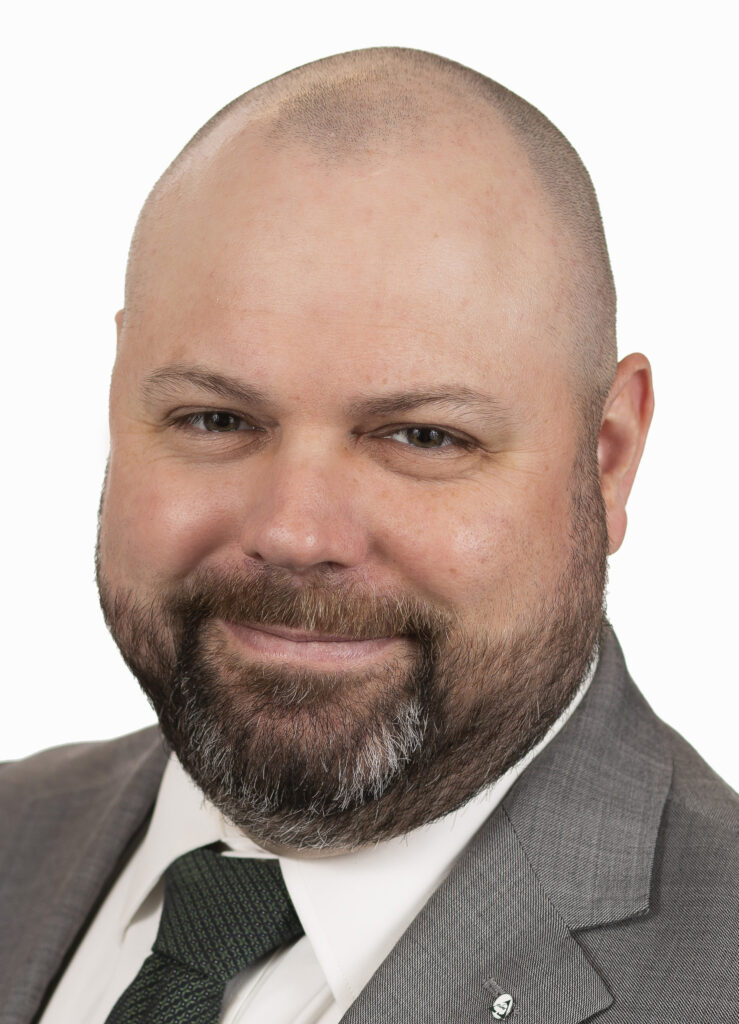
Rich Hall, formerly SVP of underwriting, has been appointed as EVP and will assume responsibility for regulatory and government affairs, as well as for special projects critical to PLM’s future growth and profitability.
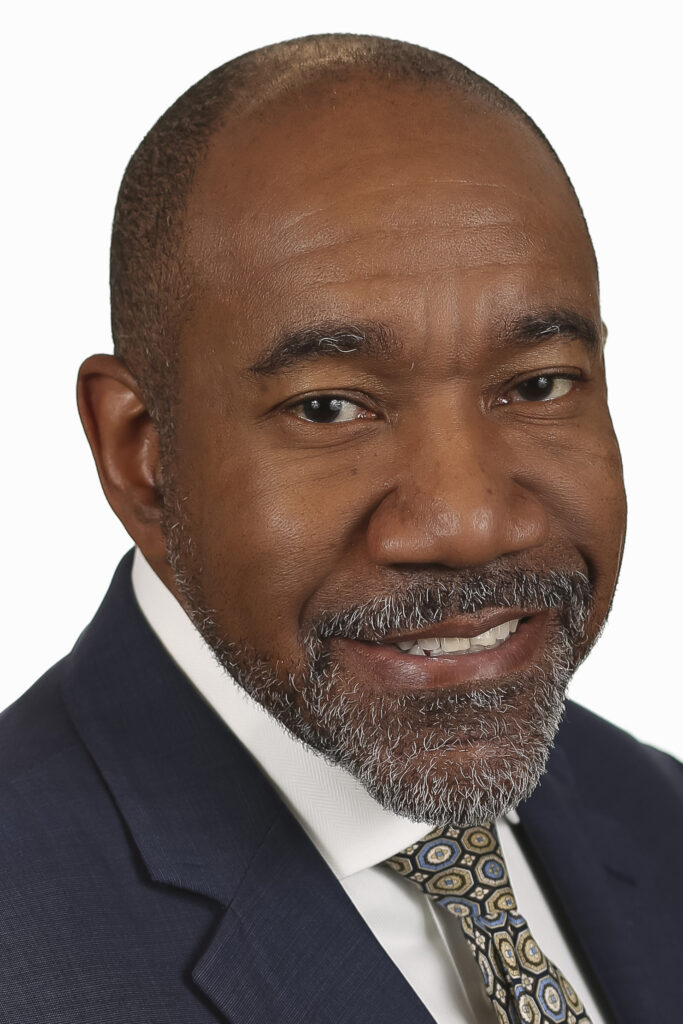
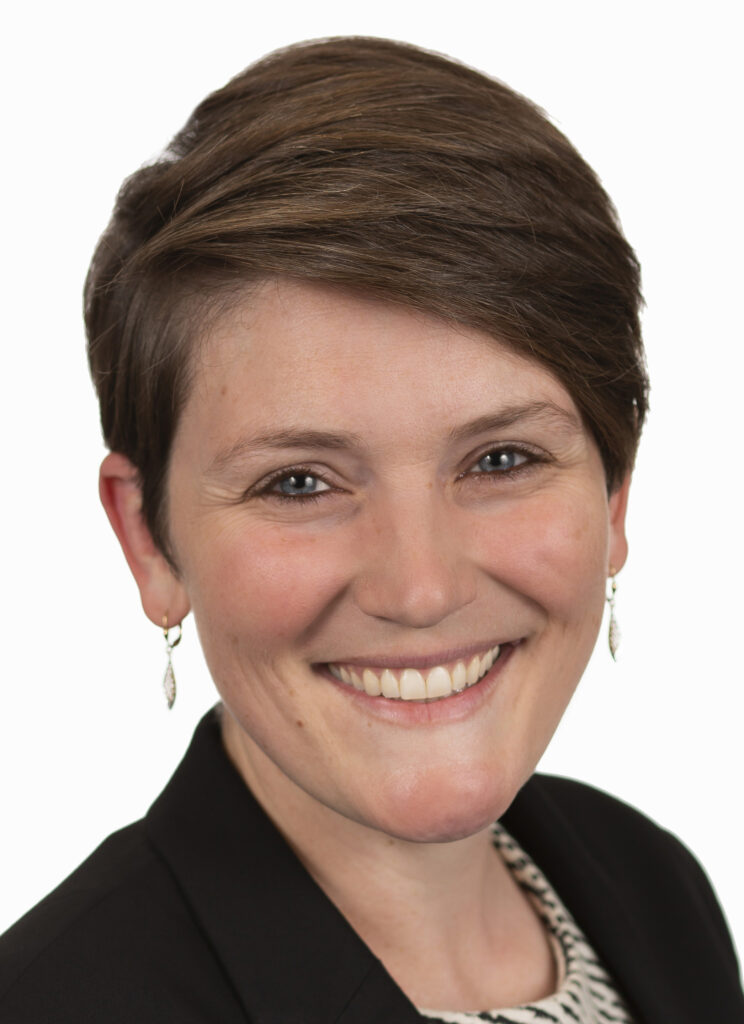
Steve Hicks, CPCU, formerly assistant vice president (AVP) of underwriting, has been appointed as vice president (VP) of underwriting.
Lindsey DiGangi, CPCU, formerly AVP of marketing, has been appointed as VP of field operations.
Sean Briscoe, formerly AVP of underwriting, has been appointed as VP of loss control.
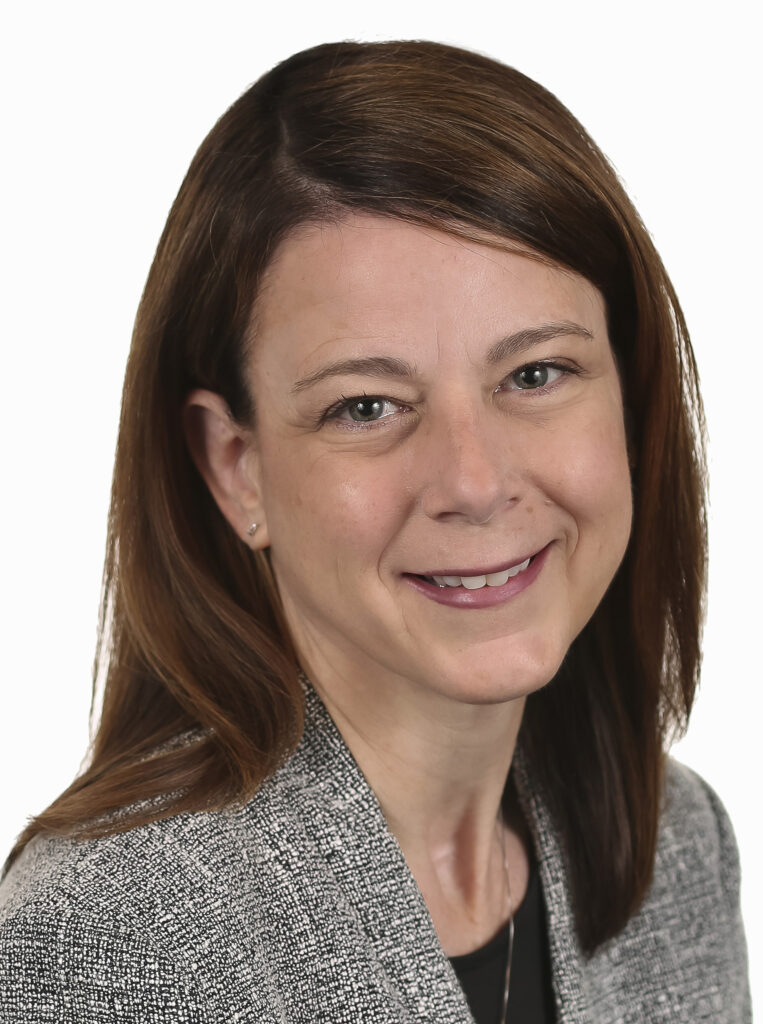
Erin Selfe, CPCU, formerly VP of information technology, has been appointed as SVP of information technology.
Harold Jamison, JD, CPCU, formerly, SVP of government and regulatory affairs and human resources, has been appointed as general counsel.
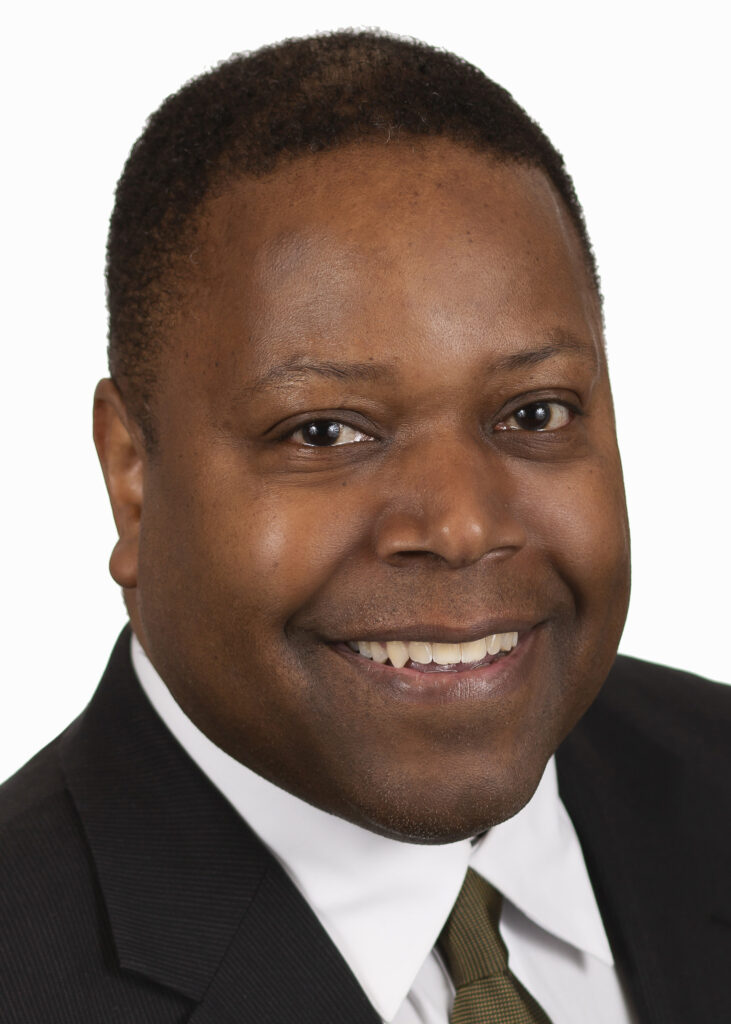
PLM is a nationally recognized property and casualty insurance carrier serving the lumber, woodworking and building material industries. Backed by 129 years of experience, the Philadelphia, PA-based company protects over 5,000 businesses nationwide with property, general liability, inland marine, business automobile, commercial excess liability and equipment breakdown coverages.
For more information about PLM, please visit www.plmins.com.
Thos. Moser Furniture Acquired By Chenmark
Thos. Moser, an iconic name in handcrafted American furniture, has been acquired by Chenmark, a family-owned holding company based in Maine.
This new chapter marks the continuation of a legacy rooted in craftsmanship, heritage and a deep commitment to excellence, Chenmark said in a release.
According to Chenmark, Thos. Moser will continue to operate with the same team and dedication to artisanal craftsmanship, collaborative spirit and design excellence that has defined its work for decades. The skilled artisans and craftspeople who bring the company’s designs to life remain at the heart of the organization, ensuring the highest standards of quality and artistry.
Thos. Moser’s furniture is built from Cherry, Hard Maple, White Oak and Walnut in grades FAS and Nos. 1 and 2 Common and in thicknesses of 4/4 through 12/4.
Thos. Moser was founded more than 50 years ago with the intent of “restoring the lost art of making furniture well.” This transition represents the next phase in the company’s history, as it moves from the stewardship by the Moser family to another Maine family who shares its “values of excellence, sustainability and community.”
Chenmark, a family-owned Maine-based business focused on nurturing and growing small businesses, said it is “honored to carry forward the traditions and mission that define Thos. Moser.” The Higgins family, founders of Chenmark, expressed their excitement about the opportunity to steward such an iconic brand.
For more information, visit www.thosmoser.com or www.chenmark.com.
NWFA Completes 78th Home With Gary Sinise Foundation
The National Wood Flooring Association (NWFA), located in St. Charles, MO, recently provided flooring for its 78th home in support of the Gary Sinise Foundation R.I.S.E. program (Restoring Independence Supporting Empowerment). The R.I.S.E. program builds mortgage-free, custom, specially adapted smart homes for severely wounded veterans and first responders. The home dedication for U.S. Army Staff Sergeant Dennet Oregon took place in Murrieta, CA. Flooring for the project was donated by NWFA member WD Flooring.
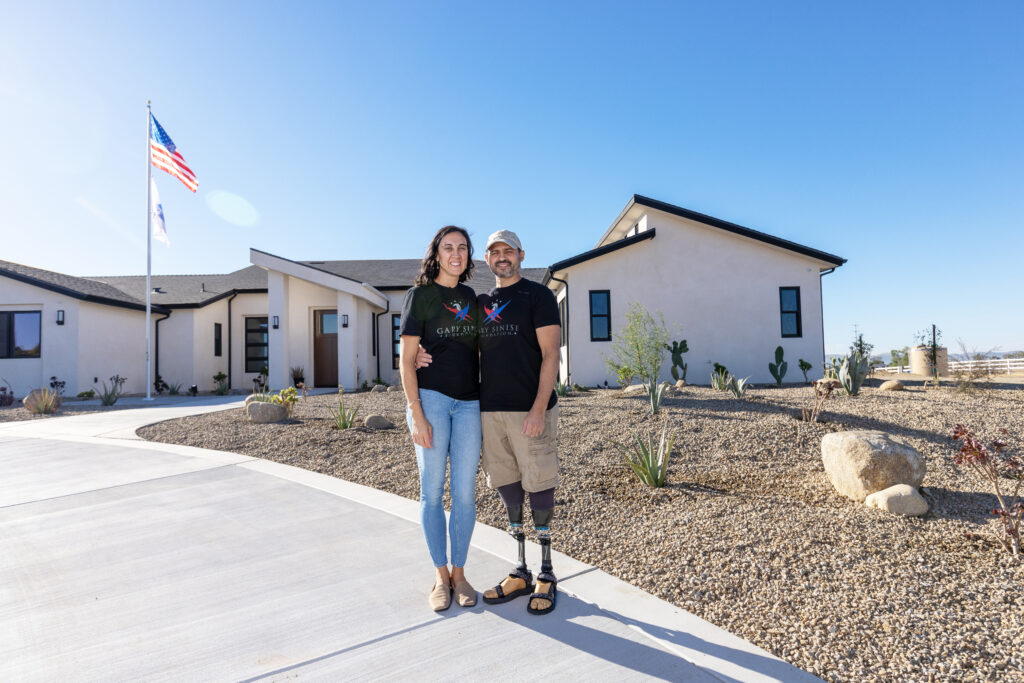
Staff Sergeant Oregon joined the Army the day after the 9/11 attacks. Four years later, while deployed to Afghanistan as part of Operation Enduring Freedom, he and his unit were returning from a five-day mission when they were struck by an improvised explosive device. The blast resulted in the loss of both legs below the knee.
In addition to the 78 homes already completed, NWFA currently is working with its members to source wood flooring for 16 additional R.I.S.E. homes in various stages of planning and construction. Currently, 157 NWFA member companies have donated product, logistics and installation services in locations throughout the United States, with a total value of more than $7 million. A list of all NWFA R.I.S.E. participating companies can be found at www.nwfa.org.
To learn more about the program, and how you and/or your company can get involved, contact the NWFA at 800-422-4556 or email them at anita.howard@nwfa.org.
The National Wood Flooring Association is a not-for-profit trade organization, with more than 3,000 member companies world-wide, dedicated to educating consumers, architects, designers, specifiers and builders in the uses and benefits of wood flooring. The NWFA is located at 14 Research Park Drive, St. Charles, MO 63304, and can be contacted at 800.422.4556 (USA and Canada), 636.519.9663 (local and international) or at www.nwfa.org.
New Study Projects Slowdown In Household Growth, Housing Demand
According to a recent study from the Joint Center for Housing Studies (JCHS) of Harvard University, household growth in the coming years is projected to slow significantly, which would have a notable impact on housing demand.
JCHS projections show household growth in the U.S. would slow to 8.6 million (approximately 860,000 per year) between 2025 and 2035, down from 11.2 million in the 2000s and 10.1 million in the 2010s.
If the trend continued, the projections show household growth between 2035-2045 would decline to just 5.1 million, which would be the lowest of any decade in the last 100 years. These projections are based on immigration levels remaining similar to those of the past three decades.
A major implication of the slowing growth would be declining demand for housing construction. Household growth is the largest source of demand for new homes. The projected slowdown would reduce demand for new construction from the current rate of 1.4 million homes to an average of 1.1 million per year between 2025-2035 and 800,000 per year between 2035-2045.
However, a key component of housing demand is the formation of households among young adults (aged 25-34). In early 2024, the National Association of Home Builders (NAHB) examined Census data that showed in the post-Covid period, the share of young people living with parents had been declining. As of 2022, that share had fallen to a decade low—a promising trend signaling sustained housing demand in the years to come.
Further NAHB analysis recently examined which areas of the country have the highest and lowest shares of young adults living with their parents. Although the overall shares show a decline, this demographic continues to face a myriad of housing affordability challenges, particularly elevated home prices and increased costs of living.
For more information visit www.jchs.harvard.edu or www.nahb.org.
(First published in the LBM Journal.)