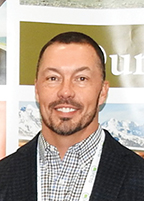
Atlanta Hardwood Corporation Partners With Oy Lunawood Ltd
Atlanta Hardwood Corporation and Oy Lunawood Ltd recently announced the formation of a joint venture, Lunawood LLC. This new entity will oversee the procurement, production and sales of ThermoWood® and other thermally modified products across North America.
Under this joint venture, Lunawood LLC will build a production facility at Atlanta Hardwood Corporation’s plant in Cleveland, GA. The plant will be dedicated to producing thermally modified timber products from locally sourced hardwood for the North American market, with additional global distribution. Lunawood is the first Finnish company in the mechanical wood industry to establish production in the U.S.
Lunawood, a pioneer in thermal modification of Finnish Pine and Spruce since 2001, was instrumental in developing the patented ThermoWood® process. The joint venture combines Lunawood’s expertise in thermal modification, production, quality control and commercialization with Atlanta Hardwood’s market knowledge, logistics and moulding facilities. Lunawood LLC will stock the full range of Lunawood products for sale within North America at Atlanta Hardwood’s facilities in Cleveland, GA, and Clarksville, TN.
According to Hal Mitchell, President of Atlanta Hardwood Corporation, and brand manager for AHC Hardwood Group, “This joint venture will allow Lunawood to become the world’s leader in thermal modification in both North American and Nordic species. We are excited to offer volume production of these quality-tested, sustainable and durable products to the North American market. Scaling the manufacturing of U.S. lumber has been a dream since our first thermal modification kiln was installed 10 years ago. This joint venture allows us to accomplish that goal.”
The growing demand for thermally modified timber in the U.S. is driven by the increasing demand for sustainable building materials for both indoor and outdoor applications and a strong trend toward green building construction. Demand is especially strong in design applications, as architects and builders seek durable, sustainable alternatives to chemically treated wood or exotic hardwoods.
Atlanta Hardwood Corporation has operated from its base in the metropolitan Atlanta area since the mid-1950s and is doing business as AHC Hardwood Group in Cleveland, GA, and Clarksville, TN. Atlanta Hardwood Corporation also offers domestic trucking as AHC Logistics, which specializes in the transportation of lumber and building materials.
For more information, visit www.hardwoodweb.com.
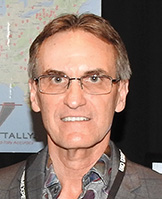
MO PAC Lumber Co. Installs New Solar Power Generation System
MO PAC Lumber, located in Fayette, MO, recently installed a 515 kW-DC solar power generation system, manufactured by Artisun Solar, which is located in Overland Park, KS.
“This solar power generation system will decrease our overall energy cost for the next 20 years and beyond,” said Bucky Pescaglia, president of MO PAC. “We want our customers to know that we prioritize using green energy to manufacture the products that they are buying from us. So, whether the energy is coming from our new solar generation system, or from the sawdust and chips that we use to fire the boiler system, we are looking for sustainable energy sources.”
MO PAC Lumber Co. started in 1980 as a sister company to Pekin Hardwood Lumber Co. located in Pekin, IL. MO PAC Lumber produces 3.5 million board feet annually of 4/4-16/4 Walnut lumber in a variety of widths, lengths and grain pattern sorts. About 60 percent of the company’s sales are export and 40 percent are domestic. They are able to offer full loads or can ship smaller volumes via LTL trucking.
For more information, visit www.mopaclumber.com.
Sundher Timber Products Expands With Great Western Lumber Acquisition
Sundher Timber Products expands its global presence and market share with the acquisition of Great Western Lumber, boosting U.S. operations and custom processing services.
Sundher Timber Products is a British Columbia specialty wood products manufacturer and marketing company located in Surrey, B.C. They buy B.C. Coastal logs and manufacture them into lumber for sales in North America, Europe, Japan, China and India.
Their value proposition is to develop a customer base with unique or specific requirements not met by larger global forest products companies and to create manufacturing or sales programs to address those needs. Their commitment is embodied in the motto, “We strive for excellence.”
Sundher Timber Products manufactures and markets lumber from a full range of B.C. log species — Western Red Cedar, Yellow Cedar, Douglas Fir, Hemlock and Balsam — into a full range of product sizes and grades. They have established sales agents in two key markets, India and Vietnam, to provide closer customer service to their clients.
They have recently acquired Great Western Lumber in Everson, WA. This acquisition will enable Sundher Timber Products to expand its U.S. market share for Coastal Douglas Fir, West Coast Hemlock and Western Red Cedar, ranging from the highest clear grades to structural and utility grades. They will be offering custom processing services, including kiln drying and planing, to other companies.
For more information, visit www.sundhergroup.com.
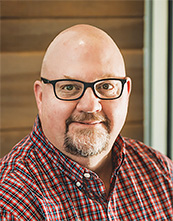
Hancock Lumber Named Three New Executives
Hancock Lumber, located in Casco, ME, recently repositioned itself as a ‘division-less’ organization. As the company continues to grow and evolve, this restructuring is designed to help meet current and future business demands, execute strategic initiatives, and foster collaboration and alignment companywide.
The company remains all-in on being a world-class White Pine manufacturer and adding value to those products, on servicing builders through its lumberyards and kitchen design showrooms, and on being a market leader in component manufacturing with trusses, wall panels, and Tiny Homes—but, above all, on honoring its mission to enhance the lives of the people who work at or are connected to Hancock Lumber. As part of this change, the company welcomed two new members to its executive team and announced a significant internal promotion.
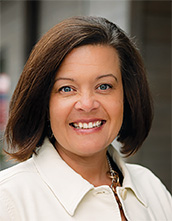
Mark Hopkins was named companywide chief operating officer. In this role, Hopkins has direct responsibility for all locations—including the company’s three Eastern White Pine mills—to help drive a consistent experience across culture, people, safety, sales and operations. Hopkins joined Hancock in 1996, working as a Counter Pro in Yarmouth. He went on to become an account manager until being named the Bridgton, ME, general manager in 2012. Hopkins transitioned to retail sales manager in January 2015 before being named Chief Operating Officer for retail in September 2015.
Hillary Roy was named chief people officer. Following over two decades and many leadership roles at Hannaford, Roy joined the executive leadership team in October 2024 as chief people officer due to an internal move in Hancock Lumber’s Human Resources department. In addition to overseeing 15 stores with direct responsibility for the employee experience, safety and talent development, Roy helped develop, launch and support scalable and sustainable people-focused programs across the entire Hannaford organization.
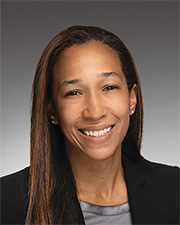
Rebecca Hatfield was named chief strategy and revenue officer. The chief strategy and revenue officer is a new role that was created to expand Hancock Lumber’s executive team’s capacity and help execute on strategy and revenue generation. Hatfield joins Hancock’s team with a career in finance, strategy, real estate development, construction services, property management and leadership—most recently serving as president and CEO of Avesta Housing.
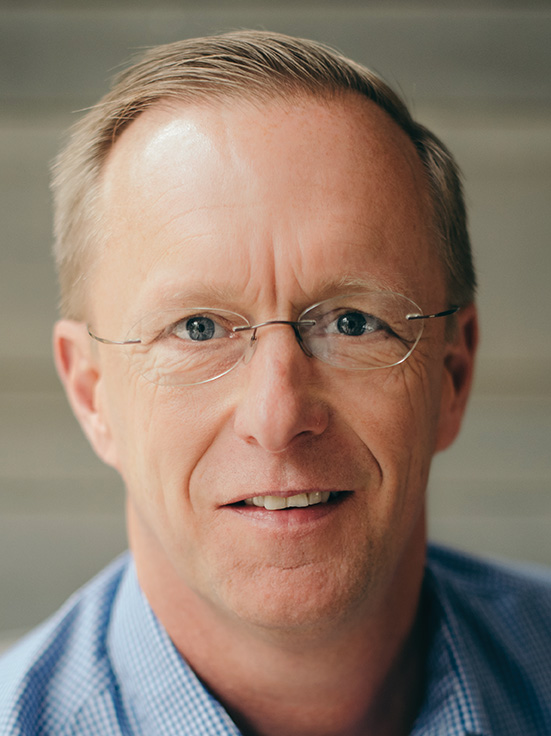
With this leadership transition, Mike Shane will be assuming a new role leading White Pine manufacturing operations overseeing Bethel, Casco and Pittsfield in conjunction with site general managers. Matt Duprey, chief sales officer – White Pine, will continue to manage the company’s White Pine customers and sales.
Hancock Lumber is a seventh-generation, family-owned integrated forest products company. The company operates high-efficiency White Pine mills, a network of lumberyards, truss and wall panel manufacturing facilities and full-service kitchen design showrooms. Team Hancock is led by over 700 employees.
For more information, visit www.hancocklumber.com.
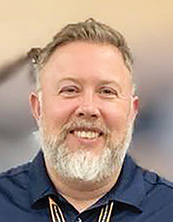
McDonough Manufacturing Welcomes New Sales
Representative
Troy Whitman recently joined McDonough Manufacturing’s BID Canada Division, as their new sales representative. Whitman is a sales professional with over 20 years of experience in building relationships, solving challenges and driving results.
As a key part of the BID Canada team, Whitman works closely with clients to deliver tailored solutions in the material handling industry. From belt conveyors to screws and bucket elevators, Whitman’s expertise ensures that customers get the right products and support to keep their operations running smoothly, said a company representative.
Whitman’s success stems from his ability to spot opportunities and stay ahead of industry trends. Certified by the Canadian Professional Sales Association (CPSA) and having completed Northwestern Kellogg’s Mastering Sales program, he brings a unique mix of formal training and hands-on experience to every project. He’s passionate about finding practical, effective solutions while keeping things straightforward and results focused, the company representative noted.
At BID Canada, Whitman is all about collaboration, whether it’s working with customers to solve specific challenges or supporting his team to meet their goals, he knows that success comes from working together. The company representative stated that his approachable style and commitment to building strong relationships make him a trusted partner in every interaction.
When he’s not on the job, Whitman keeps busy coaching hockey, where he instills values of teamwork and discipline in young athletes. He’s also an avid traveler and outdoors enthusiast who’s always up for a new adventure. Whether at work or play, Whitman brings the same energy, curiosity and problem-solving mindset to everything he does, making him a valuable part of the BID Canada and McDonough family.
For more information, visit www.mcdonough-mfg.com.
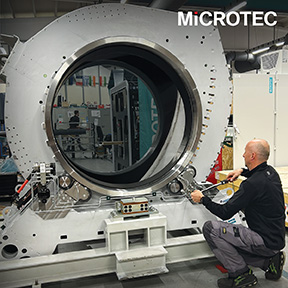
MiCROTEC And Real Performance Machinery Make Installations At Two Rivers Lumber
As part of a pioneering project in Alexander City, AL, Two Rivers Lumber, with MiCROTEC and Peak North America, Real Performance Machinery’s (RPM) parent company, is advancing the industry through a fully integrated greenfield mill that combines high-tech optimization with precision machinery.
Equipped with MiCROTEC’s CT Log and RPM’s ProDog machinery, this sawmill is redefining standards in quality, traceability and sustainability, maximizing lumber recovery with unprecedented accuracy.
The collaboration behind Two Rivers Lumber addresses the industry’s need for sustainable and profitable operations. By leveraging MiCROTEC’s advanced scanning solutions, Two Rivers Lumber makes high quality, data-driven decisions that reduce waste, improve product yield and minimize environmental impact. This technology is resilient in fluctuating markets, enabling mills to consistently maximize output and quality, and operate profitably through the cycle.
This project demonstrates how advanced technology, intelligent design and environmental stewardship can reshape the future of sawmilling. With the CT Log and RPM’s ProDog solutions, Two Rivers Lumber isn’t merely investing in innovation—it’s establishing a new industry benchmark focused on sustainable resource use, product quality and profitability, according to RPM.
By prioritizing high-grade, sustainable lumber processing, Two Rivers Lumber is paving the way for a smarter more resilient lumber industry ready to thrive under any market conditions, according to Two Rivers Lumber. This project serves as a model for sustainable success, proving that high-tech solutions and environmental responsibility can create a bright future for the industry, according to MiCROTEC.
For more information, visit www.microtec.us or www.rpmachinery.com.
Nyle Dry Kilns Completes Kiln Installation For Hammond Lumber Company In Belgrade, ME
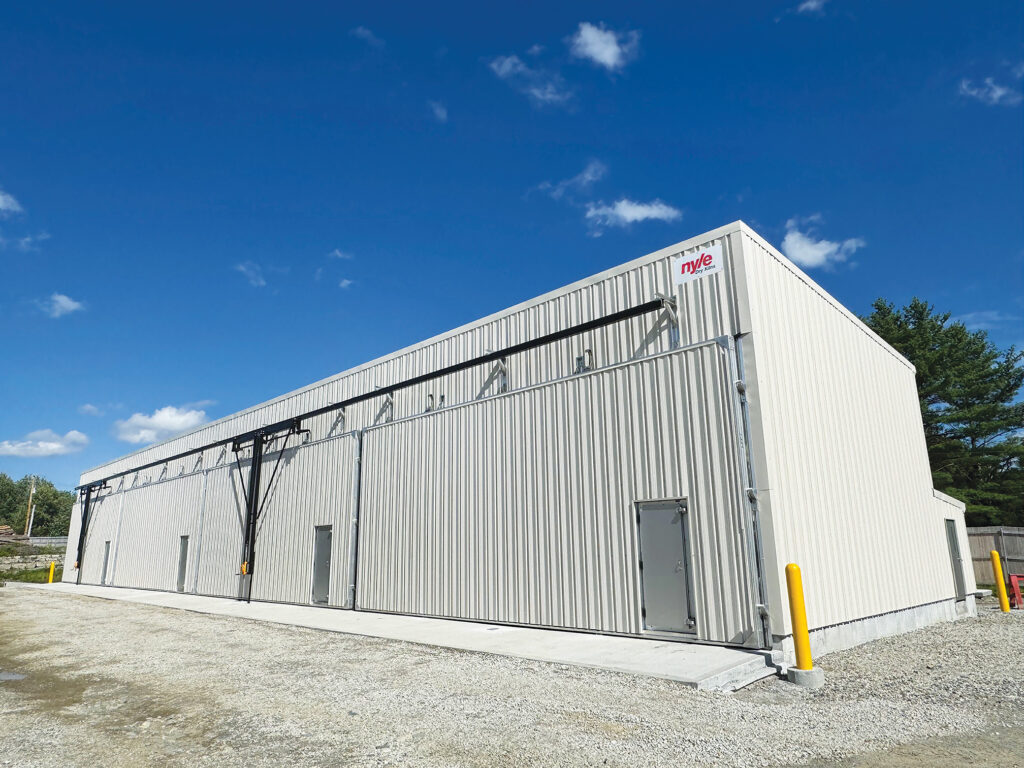
Nyle Dry Kilns recently completed the installation of a new state-of-the-art kiln system at Hammond Lumber Company, located in Belgrade, ME. This major upgrade is part of Hammond Lumber’s ongoing efforts to improve operational efficiency and maintain its position as a leading supplier of Eastern White Pine in the region.
The project involved the installation of four Nyle DH Forklift Kilns, each with a capacity of 40,000 board feet, totaling 160,000 board feet across the system. These kilns feature Nyle’s HT54 dehumidification system, which is designed to operate at high temperatures up to 160°F. With 600,000 BTUh LP gas preheat per chamber, this system is optimized for fast and energy-efficient drying, making it an excellent fit for Hammond Lumber’s requirements.
The kilns are designed specifically for drying Eastern White Pine and incorporate cutting-edge features like 36-inch reversing fans, electric-powered exhaust vents and Nyle’s advanced control system. The control system includes a cloud based interface, a 7-inch local control screen interface, digital readouts and remote access capabilities, allowing for seamless operation and monitoring. Additionally, the system’s cloud-based Kiln Connect Control allows for advanced data logging and analysis, ensuring efficient and consistent drying cycles across all four chambers.
Hammond Lumber’s new kiln setup is expected to significantly enhance its overall drying capacity while maintaining energy efficiency and sustainability in line with its commitment to environmental responsibility.
For more than 50 years, Nyle Dry Kilns, located in Brewer, ME, has been a leader in lumber drying technology, providing innovative solutions tailored to the needs of their clients. This latest project for Hammond Lumber Company underscores Nyle’s dedication to delivering high-performance systems that drive success for lumber businesses nationwide.
For more information on Nyle Dry Kilns or to inquire about their services, visit www.nyledrykilns.com.
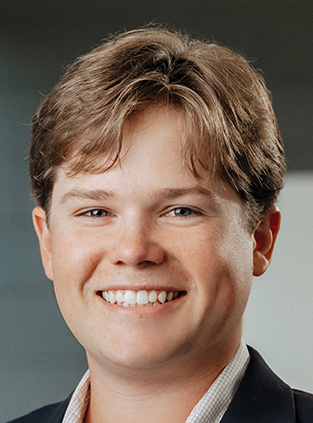
Continental Underwriters Welcomes Rollins Thompson
Continental Underwriters Inc., located in Richmond, VA, recently welcomed Rollins Thompson as their newest associate production underwriter. Thompson will help with the behind-the-scenes underwriting tasks with client-facing responsibilities. He will work directly with his colleagues to continue to build strong relationships within the industry.
Continental Underwriters Inc. is a Managing General Agency (MGA) and wholesaler providing the forest products industry in North America with a broad range of insurance and risk management solutions designed to safeguard against losses and protect the value of the businesses they insure. Their programs offer a portfolio of insurance coverages for the building materials, lumber, forest products and woodworking industries.
Thompson is an avid outdoorsman whose passion for hunting and fishing led him to pursue Forestry Operations and Business at Virginia Tech.
Outside of work, Thompson can be found hunting, fishing or golfing. His favorite quote from Heraclitus: “No man steps in the same river twice, for it’s not the same river and he’s not the same man.” His belief in constant growth and adaptability fuels both his personal and professional life.
Continental Underwriters is a member of Lake States Lumber Association, Indiana Hardwood Lumbermen’s Association, Appalachian Hardwood Manufacturers Inc., National Wooden Pallet and Container Association, Hardwood Manufacturers Association, North Carolina Forestry Association, Western Wood Products Association, Mississippi Lumber Manufacturers Association, Southeastern Lumber Manufacturers Association, Great Lakes Timber Association, National Hardwood Lumber Association, Virginia Forestry Association, West Virginia Forestry Association and Wood Products Manufacturers Association.
For more information, visit www.contund.com.

TechWood Joins Efforts To Rebuild Indiana Community Landmark With Protective Lumber Treatment
TechWood, a leading developer of protective lumber treatment solutions located in Ft. Pierce, FL, recently joined forces with industry partners to protect and secure a better future for a staple of a small Indiana community.
Located in the heart of Daviess County, IN, The Bargain Center, a family-owned grocery store, and a staple of the Daviess community, recently succumbed to a catastrophic fire which devastated the original structure and shook the community with an almost complete loss of the store and nearby warehouse.
No stranger to the devastating effects of fire, TechWood who provides three levels of lumber protection treatment solutions through TechWood 2200, 3300 and 4400, immediately offered to provide treatment of all lumber materials needed for the new construction. Specifically, its patented 3300 solution, which provides warrantied protection against mold, rot, decay and termites, and additionally offers Class A fire protection both during and post-construction.
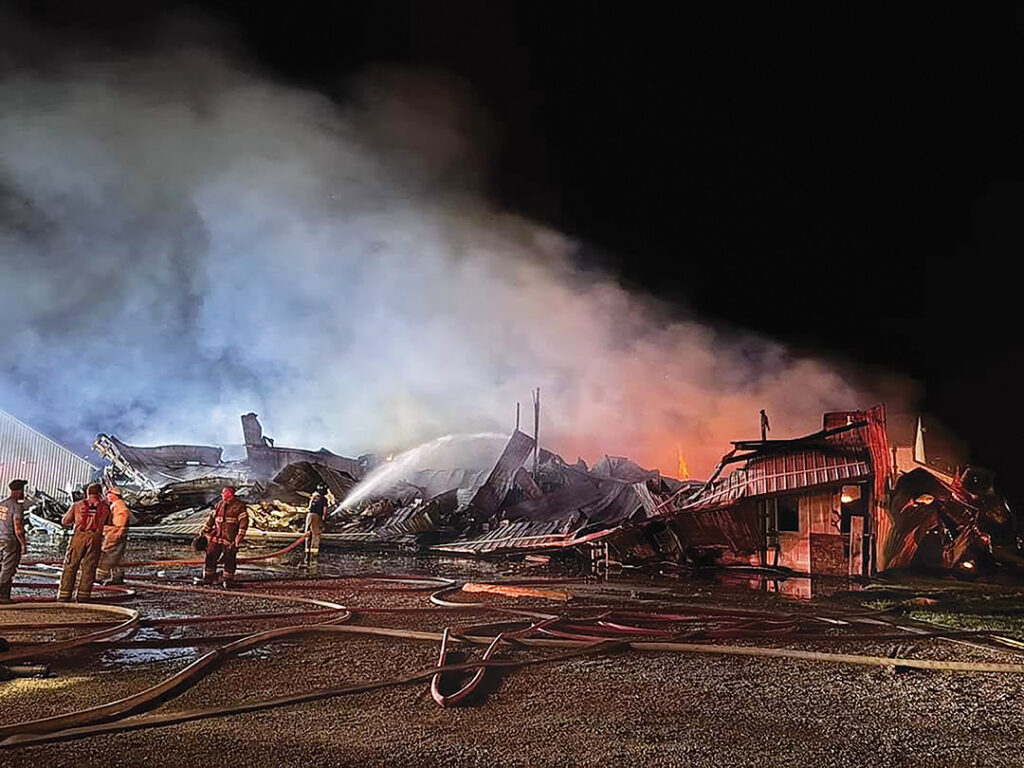
The Bargain Center, a family-owned grocery store, recently succumbed to a catastrophic fire.
Working together with K&K Industries, a leading manufacturer and builder of truss construction (as well as an industry distributor of the innovative TechWood products) the two teams banded together with local, community and corporate volunteers to treat over 44,000 board feet of lumber and help begin the construction of the new facility with essential fire protection for the future.
“This was an opportunity for us to provide our quality protection for a very special cause.” said Matt Visconti, senior market development manager for TechWood and its parent company Chemical Technology Holding Inc. “We are constantly aware and cognoscente of the risks of fire, both to existing structures and future construction. We wanted to ensure that The Bargain Store was protected properly for the future against all risks and to provide support for an amazing small business to flourish once again.”
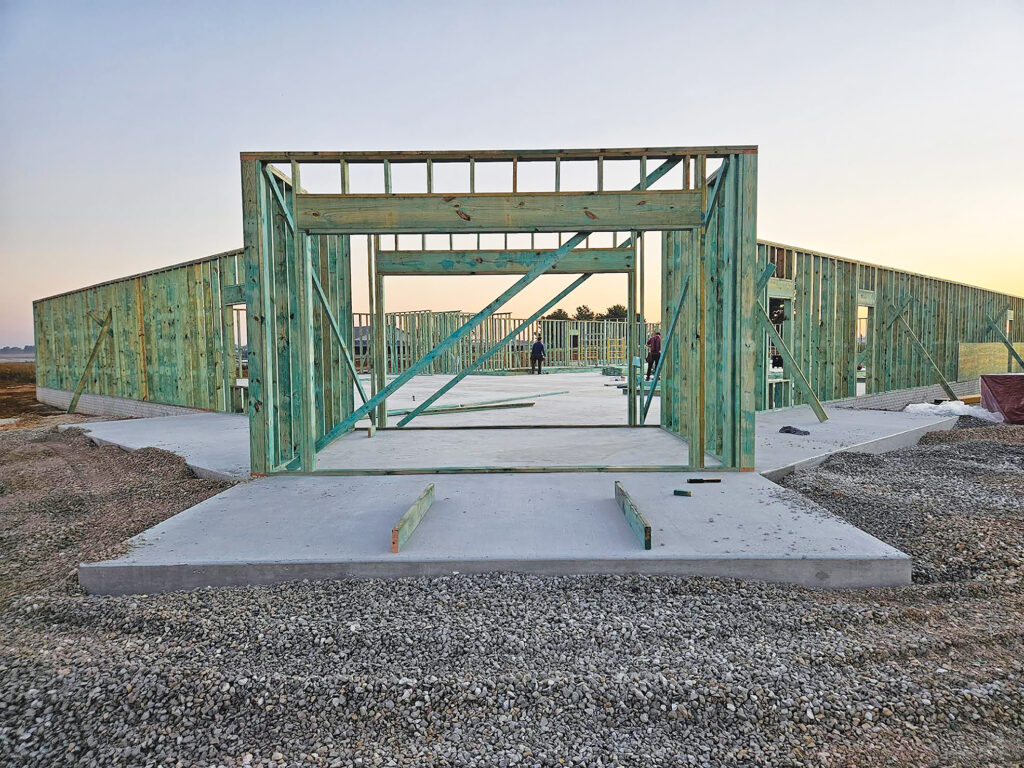
TechWood, along with volunteers, treated 44,000 board feet of lumber to help begin the construction of the new grocery store with essential fire protection.
TechWood provides treatment services to builders, engineers, architects and contractors nationally through their network of licensed applicators, as well as through their 16,000 square foot treatment facility.
For more information on TechWood and TechWood lumber treatments, contact them via email at connect@techwoodtreatments.com, call 772-577-3124 or visit www.techwoodtreatments.com.