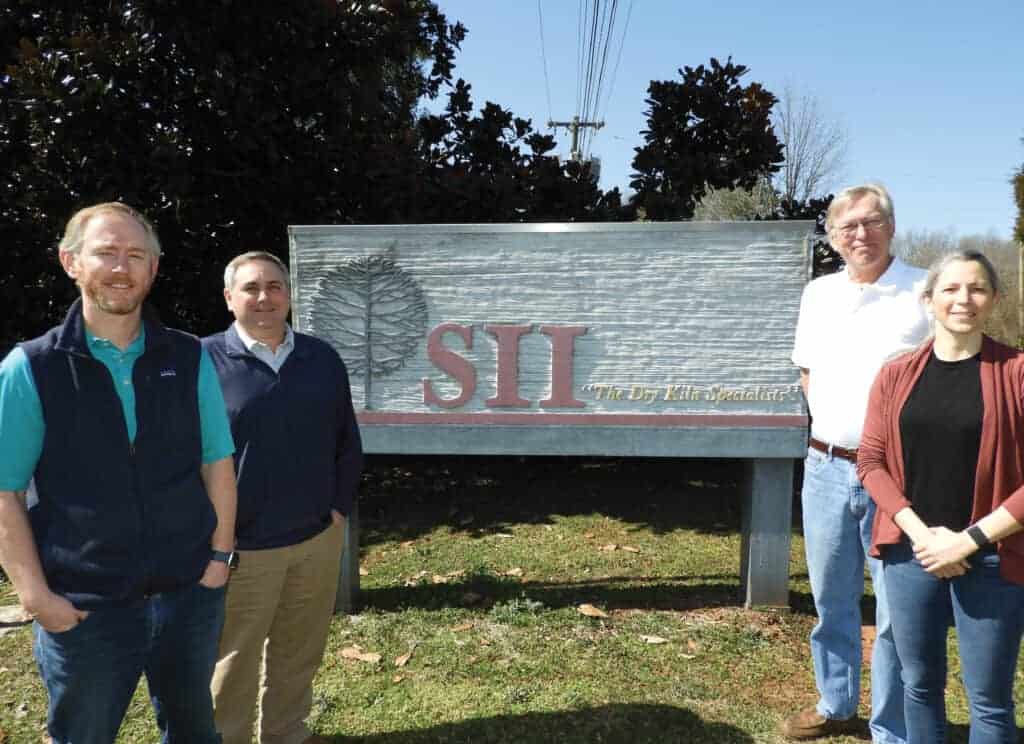
Lexington, NC—SII’s equipment can be seen producing high quality products for hundreds of lumber companies throughout America. While being a staple in the lumber industry, SII, headquartered here, has also cultivated hard-working principles that set them apart from all other kiln companies, according to a company spokesman. Since 1969, the company has remained a family owned and operated business by the Mathews and Turlington families. “We manufacture all of our products ‘in-house,’ which allows us better oversight of the fabrication process, and most field installation is done by our crews, who have decades of experience building drying equipment. We own it from beginning to end,” stated Brian Turlington, vice president. In addition to that, SII is versatile in the kinds of kilns they install, from conventional package-loaded and“SII-Design”-center-fan-wall Hardwood kilns to Dual Path Continuous, or DPK’s, and double or single track-loaded softwood kilns.
SII offers various alternatives to air drying lumber with fan sheds and multi-zoned pre-dryers for the Hardwood industry. “These products allow our customers to maximize their kiln throughput by minimizing the amount of kiln-time required to dry and condition the lumber,” stated Ben Mathews, also a vice president. SII provides complete kiln rehab and rebuild services including roofs and wall panels, doors, heating systems, fan decks and structural replacements. SII builds kilns as small as 10,000 board feet up to 250,000 board feet. Their kilns are tailored to the specific needs of the client.
President Dan Mathews recalled, “The company was started in 1969 by my father, Paul Mathews, and his partner, Jim Morgan. Dad handled the sales, and Jim was the hands-on expert. The company was strictly an installation company,” Dan Mathews continued. “My father sold for other manufacturers of kilns. Some of those manufacturers didn’t want to install the kilns, and that opened the door for a kiln installation company. That’s how the company really began,” Dan said, “and that’s where the name came from – Southeastern Installation Incorporated (SII).”
In the late 1970s, Paul’s son Tom Mathews came to work for SII, and, according to Dan, “He is the one that pushed for more manufacturing. So, that’s how we really got going into the manufacturing end of it.” In the late 1980s, the company began doing business as SII Dry Kilns.
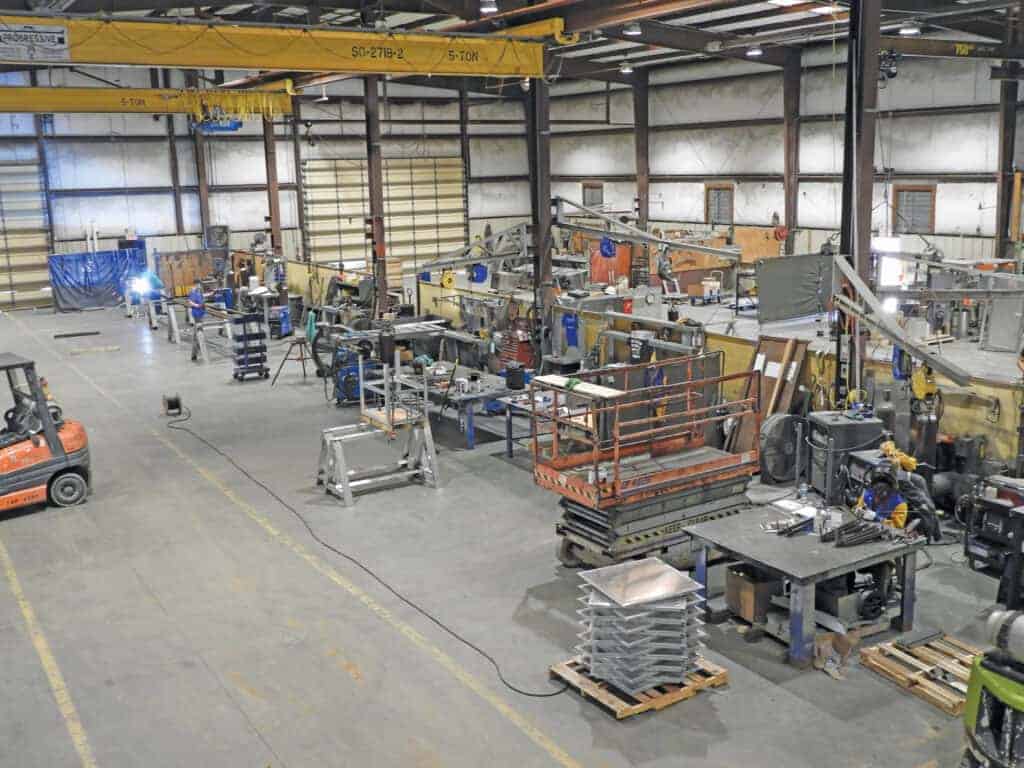
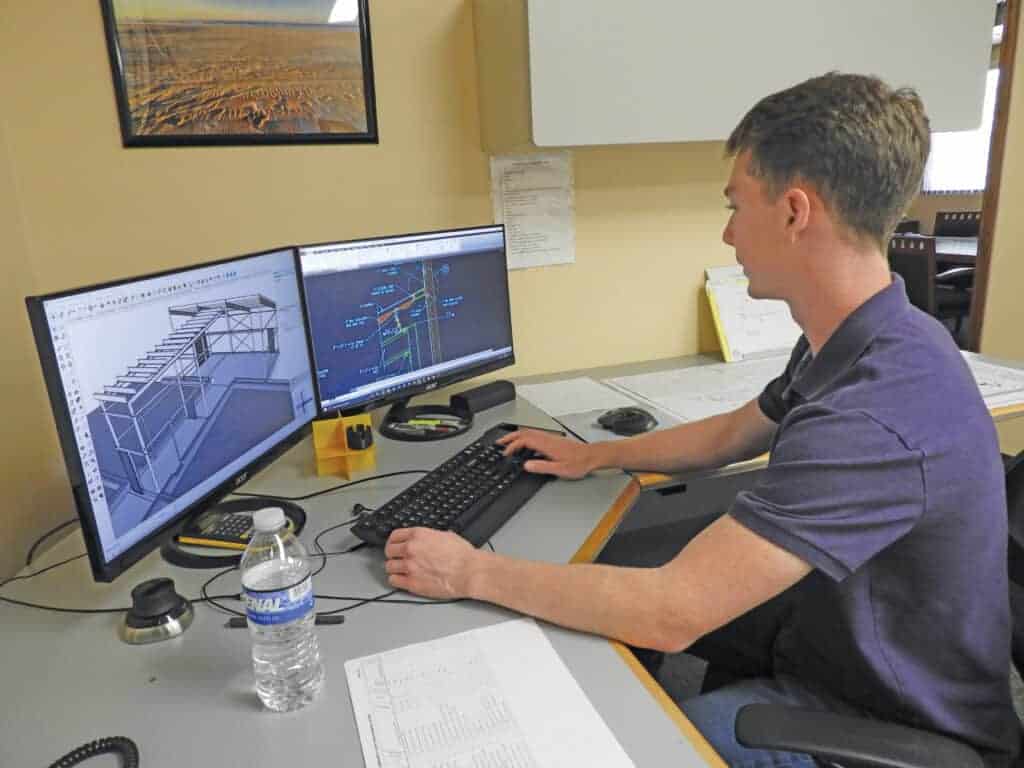
“We are definitely not cookie-cutter, and we are not boxed into certain types of designs. Everyone knows they get that backstage access to any of us – after the sale, and I think that is exceptional.”
Ben Mathews, vice president of operations, SII Dry Kilns
The first kilns built by SII were furniture-style kilns made with masonry walls with steel trusses overhead, Dan stated. “As SII began to grow and we did more installations and more manufacturing of components, it became more apparent that prefabricated construction of kilns with corrosion-resistant materials was the future rather than staying with masonry kilns.” That’s the point at which Dan became involved with SII. He left his architectural firm and came on board full-time, joining his father and brother, on Jan. 1, 1990. The next year, Paula Turlington, Dan’s sister, joined the company and worked closely with Paul in sales. She later became the vice president of sales for the company. With Paul’s wife, Dorothy Mathews, working in and out of the office, SII had developed into a complete family operation.
“We evolved through the 1990s, doing more and more manufacturing of the complete facility for the drying operation, whether that happened to be in kilns, pre-dryers, fan sheds or other types of equipment. That’s how we grew into more of a manufacturing company, rather than just installing or refurbishing of other manufacturers’ equipment,” Dan recalled.
In 1995, Tom Mathews, died of cancer. Also, in 1995, Brian Turlington came to work for SII. In 2002, Ben Mathews came on board. Mary Mathews came to work for her family’s company in 2012.
Today, Dan Mathews is President of SII, Ben Mathews is Vice-President of Operations, Brian Turlington is Vice-President of Sales and Mary Mathews oversees the inside sales/parts division. In sales, Ken Matthews services the Southeast and South Central, Jim Higgins works in the Midwest and Lake States and Bob Pope covers Pennsylvania to New England. The organization employs more than 60 people.
In the parts division, “We not only inventory over $200,000 of kiln components from valves to actuators, controllers, motors and fan blades for immediate shipment, but also we have lots of vendors that we have great relationships with,” Mary Mathews noted. “We can find the part when a client needs it. We are going to make sure that we get the part to them as fast as possible to avoid downtime,” she stated. “Taking care of our past customers and keeping everyone running smoothly is just as important to us as our new customers.”
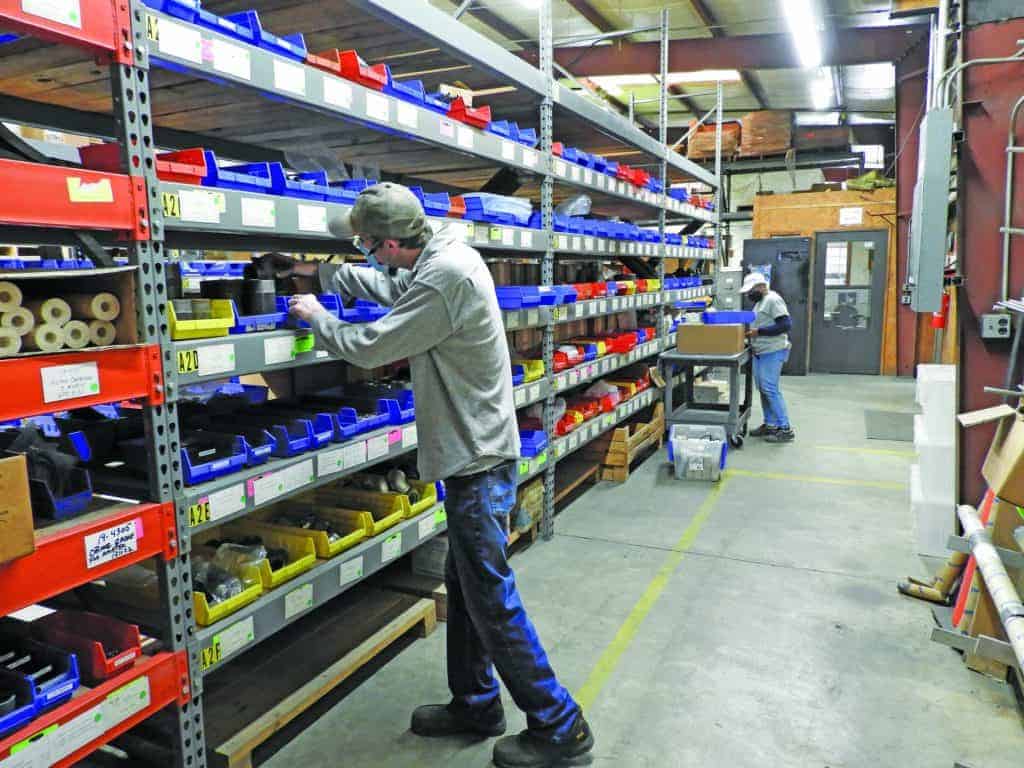
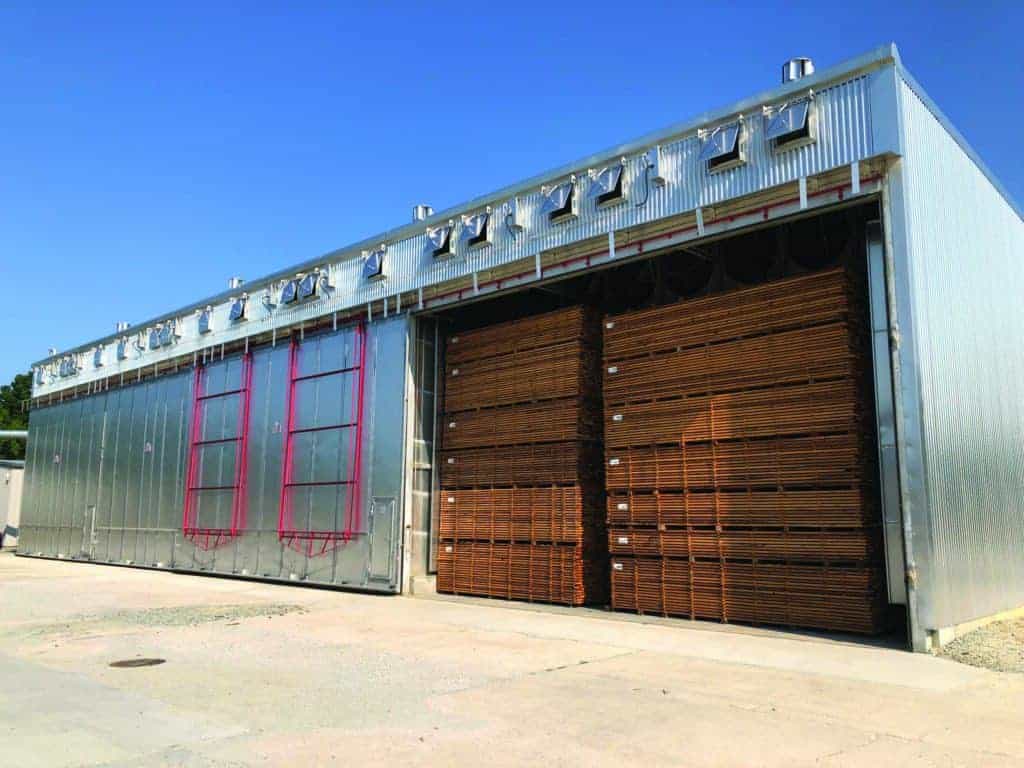
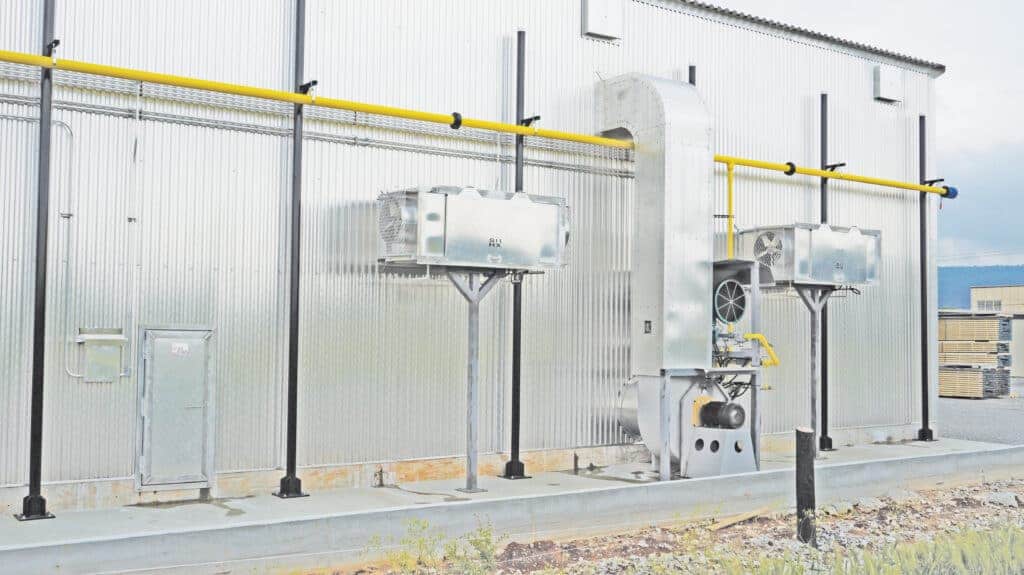
In the Hardwood industry, SII is known for offering a lot of options for their equipment. “We are definitely not cookie-cutter, and we are not boxed into certain types of designs,” said Ben Mathews. “Everyone knows they get that backstage access to any of us – after the sale,” he stated, “and I think that is exceptional.”
Brian Turlington added, “It’s a collaboration between the customer and our salespeople in which the customer knows – or has a good idea of – what they want, and then, we customize that for them.” SII provides drying variations for different species of Hardwoods, from the amount and type of heating required (steam, gas-direct or indirect) to the type and amount of venting (passive, powered, or heat exchangers) and, of course, the fan systems, which all utilize energy saving variable frequency drives (VFD’s).
In softwood, SII offers two primary types of kilns for customers.
Some softwood customers remain committed to “batch”-style kilns, while others prefer the continuous DPK-style kilns, which require 24/7 operation. Regardless of the type of track kiln desired, SII can provide the heating system that works best for the customer. From direct-fired gas or biomass systems to steam heated kilns, SII has done them all. Brian Turlington noted that such versatility is based on: “What will work best for the customer today and in the future?”
Ben Mathews commented, “We have seen our growth in softwood steadily increase, and today we do more and more softwood kilns every year.”
The controls department is second-to-none in the industry, the company points out. SII was the first American kiln manufacturer to introduce VFD’s to the industry in the mid-80’s and has been instrumental in developing the best known in-kiln weight-based computerized control system, “Sample Watch,” with over 400 systems in operation today.
According to Turlington, SII works as a partner with its customers. The firm gets over 80 percent of their sales as repeat business. SII can make acquiring a new kiln a turnkey operation or have the owner participate in the process at whatever level they prefer.
“We want to supply a quality product that’s long-lasting, regardless of whether it’s Hardwood or softwood,” Turlington stated. And SII welcomes any challenge. “We aren’t afraid of taking on any size project no matter how unique,” he said.
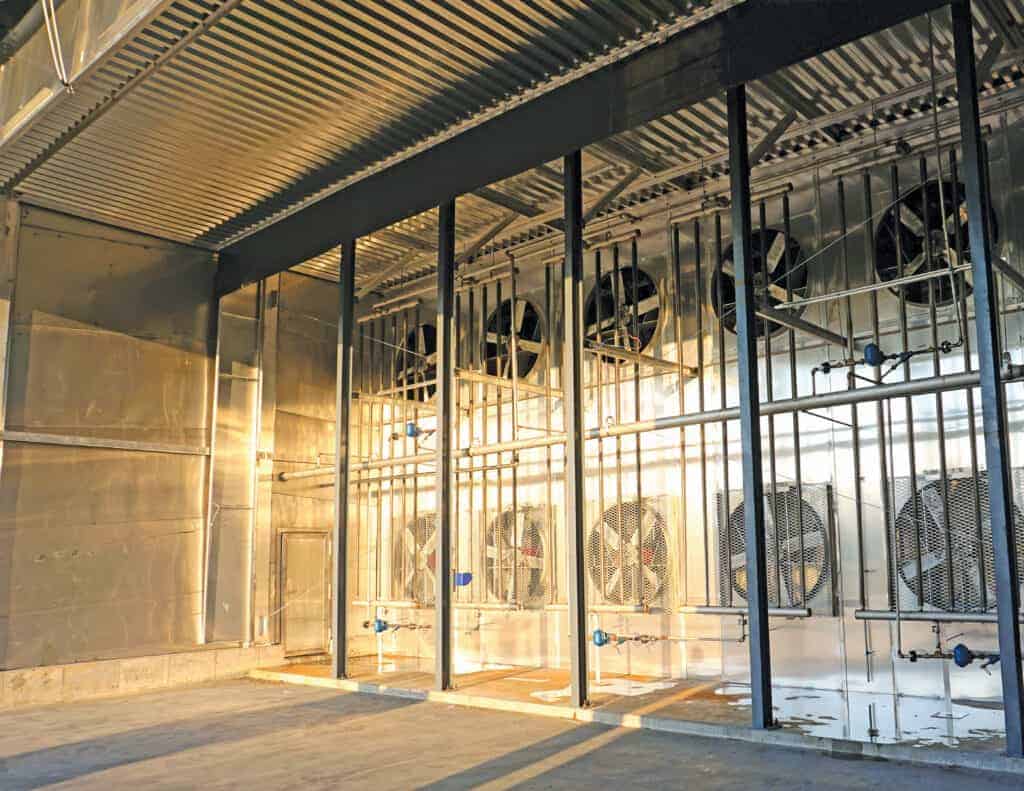
SII Dry Kilns believes very strongly in supporting industry associations and is a member of the National Hardwood Lumber Association, Southeastern Lumber Manufacturers Association, Hardwood Manufacturers Association, National Wooden Pallet and Container Association, Appalachian Hardwood Manufacturers Inc., Appalachian Lumbermen’s Club, Indiana Hardwood Lumbermen’s Association, Penn-York Lumbermen’s Club, Kentucky Forest Industries Association, Keystone Kiln Drying Association, New England Kiln Drying Association, Great Lakes Kiln Drying Association, North American Wholesale Lumber Association, Northeastern Lumber Manufacturers Association, Southeastern Dry Kiln Club, Western Hardwood Association and the New England Lumbermen’s Association.
For more information, go to www.siidrykilns.com.