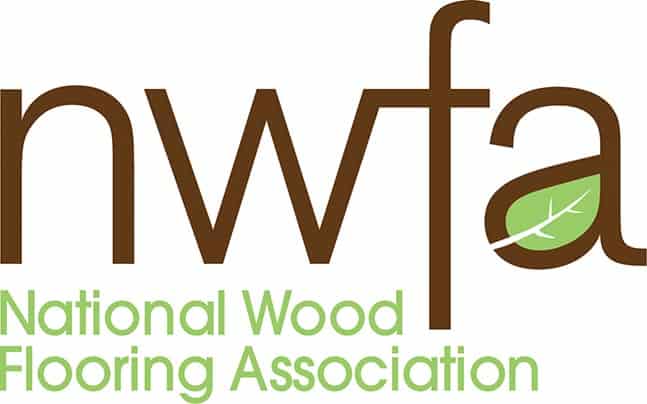
Engineered wood floors look similar to solid wood floors when in-use. Their construction, however, differs because they are manufactured using multiple layers instead of one. These layers include the top wear layer, the middle core layer, and the bottom backing layer.
The wear layer is made using a high-quality veneer produced from real wood. The core layer is made using multiple layers of wood veneers or composites. The number of layers in the core varies by manufacturer and by product. The backing layer also is made using a wood veneer or composite, but typically is a single layer. The wear layer is what determines the species of the product.
The layers are bonded together using adhesives. The grain of each layer is placed perpendicular to the layer above and/or below it, which makes engineered wood more dimensionally stable than solid wood.
Because of its multiple-layer structure, the milling process for engineered wood floors is different than for solid wood floors. It involves numerous steps that can vary significantly among manufacturers.
Veneers can be made three ways: sawn, sliced, or rotary peeled.
Sawn veneers are made using raw lumber. The cut is made by sawing straight through the lumber in much the same way as solid wood flooring. For this reason, sawn veneers have many of the same characteristics as solid wood, but the material produced is much thinner.
Sliced and rotary peeled veneers are made using raw logs. For these cuts, the logs must remain wet until they are ready to be used. Keeping the logs wet is important for the cutting process.
When the logs are ready to be used, the bark must be removed. Once this is accomplished, the logs are placed into a steam bath or pool of water. This process helps to soften the wood fibers, which makes them more flexible and easier to cut into veneers.
There is a different milling process for sliced and rotary peeled veneers, which affects the construction and performance of the veneer.
Sliced wood veneers are made by sawing the log into cants or flitches. The cant or flitch is drawn across an angled blade to produce veneers. Sliced veneers are similar in appearance to sawn veneers. For this reason, sliced veneers will have similar characteristics as solid wood. This method of cutting veneers has thickness limitations, and also can stress wood fibers, which can result in lathe-checks.
Rotary peeled veneers are made by placing the log on a large lathe and spinning the log against a sharp blade. This cut produces very wide and long veneers, with a distinct, repeating pattern. As a result, it does not have the same appearance as solid wood.
Next the veneers are cut to width, which varies by manufacturer and by product. Then they are sorted and stacked in preparation for kiln drying.
Once the veneers have reached the proper moisture content, they are ready to assemble with the other layers. Regardless of the number of layers or the materials used to make them, each layer is assembled perpendicular to the layers above and/or below it, with each individual layer glued together to form a multi-ply product. Placing the grain of each layer at a 90-degree angle helps to increase the dimensional stability of the final product. The top wear layer can be adhered to the core material in several ways: cold-press, hot-press, and nip roller. The assembled layers are called a blank.
Once the blanks are dry, they are ready to receive a final sanding. Next, the material is sidematched and endmatched. A bevel may be added as well, but this varies by manufacturer and by product.
The flooring then is delivered to the finishing line. The boards are lightly sanded to refresh the face before receiving several coats of finish.
After the finish has dried, the flooring is ready for packaging. Individual boards are sorted by length to meet the minimum square footage requirements per box. Each box then is labeled with the manufacturer, product name, species, and square footage per box.
Engineered wood floors have grown in both popularity and in market share during the past few decades, representing more than 50 percent of the total wood flooring market in the United States. This market share is projected to grow further in the coming years.
The National Wood Flooring Association has detailed information about engineered wood flooring available through NWFA University, an online training platform that is convenient and affordable. More information is available at nwfa.org/nwfa-university.aspx.