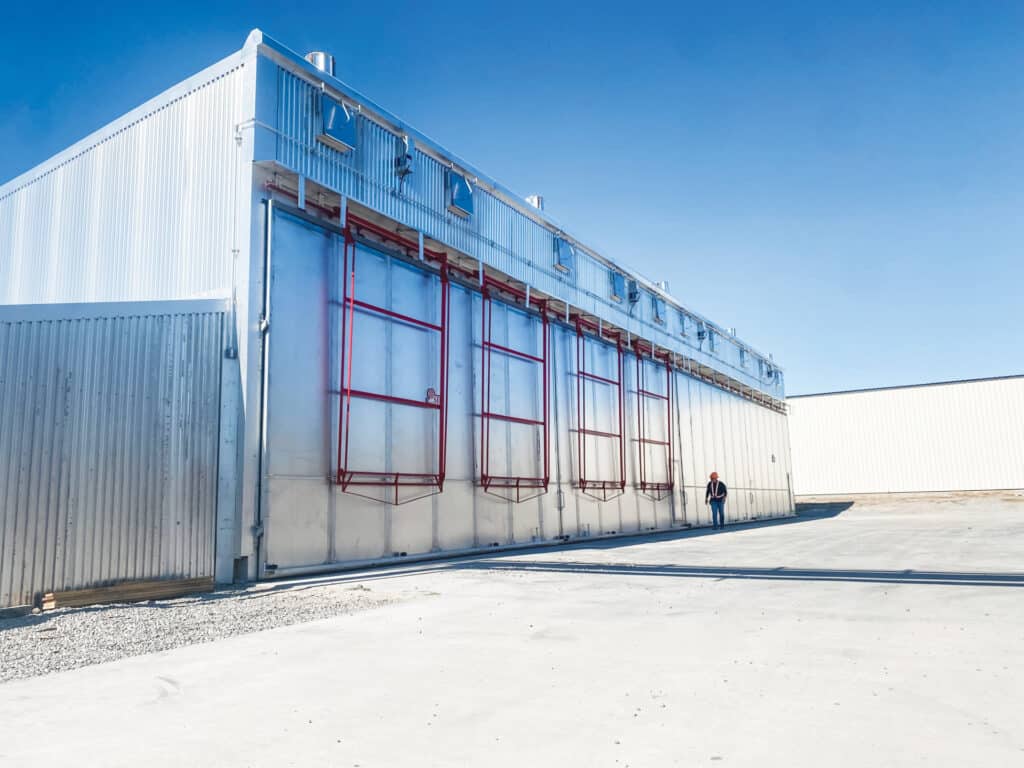
Gates Milling Inc. Recently Installed SII Package Dry Kilns
Gates Milling Inc., located in Gatesville, NC, recently installed two SII Package Dry Kilns, each with a capacity of 60,000 board feet. The addition of these two kilns has increased the company’s drying capacity by a third.
“We are already seeing an increase in weekly kiln rotations, shortened drying time and enhanced quality of certain items, expedited stick rotation and increased availability in kiln dried lumber. SII provided extensive training as well as timely support in any times of need. Our Dry Kiln Manager learned the SII operating system very quickly and has expertly transitioned the new kilns into our flow of operations,” stated Kelsey Kennedy, Vice President of Operations and Marketing.
According to Kennedy, the company is looking forward to continuing to reduce their lead time and increase the availability of kiln-dried items for their customers.
Gates Milling produces American Cypress™, poplar, Atlantic White Cedar, as well as other hardwoods. The company manufactures green lumber and timbers, kiln-dried lumber and finished profiles for interior and exterior applications. With 11 million board feet produced in the sawmill annually, they are able to process eight million board feet through their dry kiln operations per year.
Gates Custom Milling, Inc. was established in 1978 as a family-owned operation. First-generation founder, Brian H. Martin sought to remanufacture Atlantic White Cedar lumber into both interior and exterior products. Second-generation owners Mark and Nancy Tuck expanded the company under its new Gates Milling, Inc. name into a full-service, fully integrated operation, taking control of all aspects of the milling process from the log to the finished profile.
Today, with the addition of the family’s third generation, Gates has grown into one the largest producers of Atlantic White Cedar products in the country, as well as a high-quality producer of poplar materials and the highly sought after trademarked Gates product, American Cypress™.
For more information, visit www.gatesmilling.com.
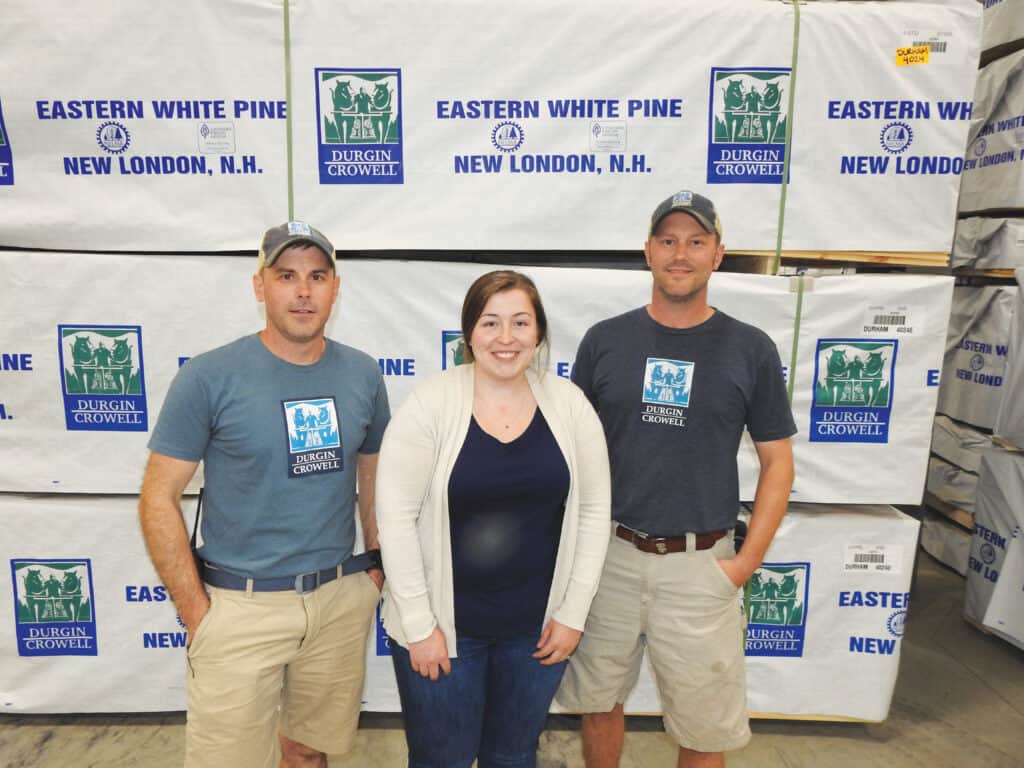
Durgin and Crowell Installs New
Bagging System
Durgin and Crowell, headquartered in Springfield, NH, recently added a BID Group AI upgrade to their Comact Grade Expert automated grading system. “The Comact works great, and has kept us on grade, since installation four years ago.” said Alex Darrah, sales manager for Durgin and Crowell. “When we purchased the grading system the AI function wasn’t yet available, as soon as it became available to us, we invested in it, to better detect the few defects that the grader struggled with.”
Durgin and Crowell also installed a second Premier Tech bagging system, which has allowed the planer mill to accommodate more orders. “Last year we had to turn away a fair number of orders because our existing system couldn’t keep up,” Darrah said. “With the addition of this second bagging system we can keep up with the planer mill’s full production capability.
Durgin and Crowell has a primary focus on sawing NELMA grade patterns in Eastern White Pine in S4S and rough lumber. They average 34 million board feet of lumber annually. Darrah and his brother Bryan Darrah handle Durgin and Crowell’s sales.
For more information, visit www.durginandcrowell.com.
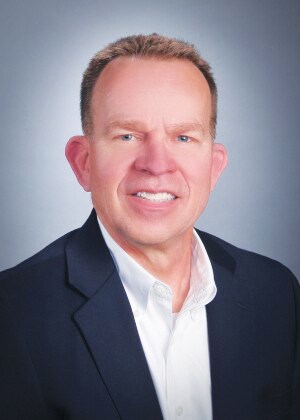
Boise Cascade Adds New
Distribution Warehouse in West Palm Beach, FL
Boise Cascade Company’s Building Materials Distribution (BMD) division, headquartered in Boise, ID, recently announced that it has completed the purchase of a new 120,000 square foot warehouse and distribution facility in West Palm Beach, FL.
The total property is 9.7 acres and will provide additional storage and service capacity for the Pompano Beach branch.
“This major expansion fits with our strategy of growing in the markets we currently serve to provide deeper depth of quality products along with dependable, consistent service for our customers,” added Jim Wickham, Vice President, BMD Eastern Operations.
Boise Cascade Company is one of the largest producers of engineered wood products and plywood in North America and a leading U.S. wholesale distributor of building products. For more information, please visit our website at www.bc.com.
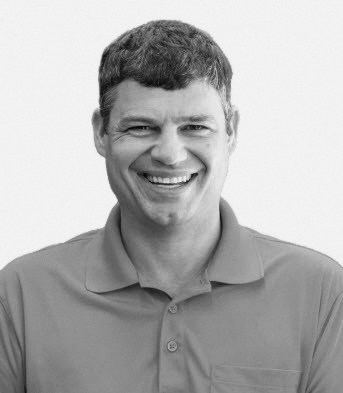
PotlatchDeltic Corporation Welcomes Ryan Daniels
PotlatchDeltic Corporation, located in Atlanta, GA, is pleased to announce that Ryan Daniels has joined their Wood Products division. As Director of Operations, Ryan Daniels is responsible for leading the manufacturing teams at the six lumber facilities and the St. Maries plywood mill.
Daniels joins PotlatchDeltic from Hood Industries where he had responsibility for leading manufacturing at four lumber and two plywood facilities. Prior to Hood Industries, Daniels was Vice President of Manufacturing at Coastal Forest Resources where he led operations of two plywood and one lumber facilities.
Daniels has a Bachelor and Master of Science degree in industrial engineering from the University of Arkansas.
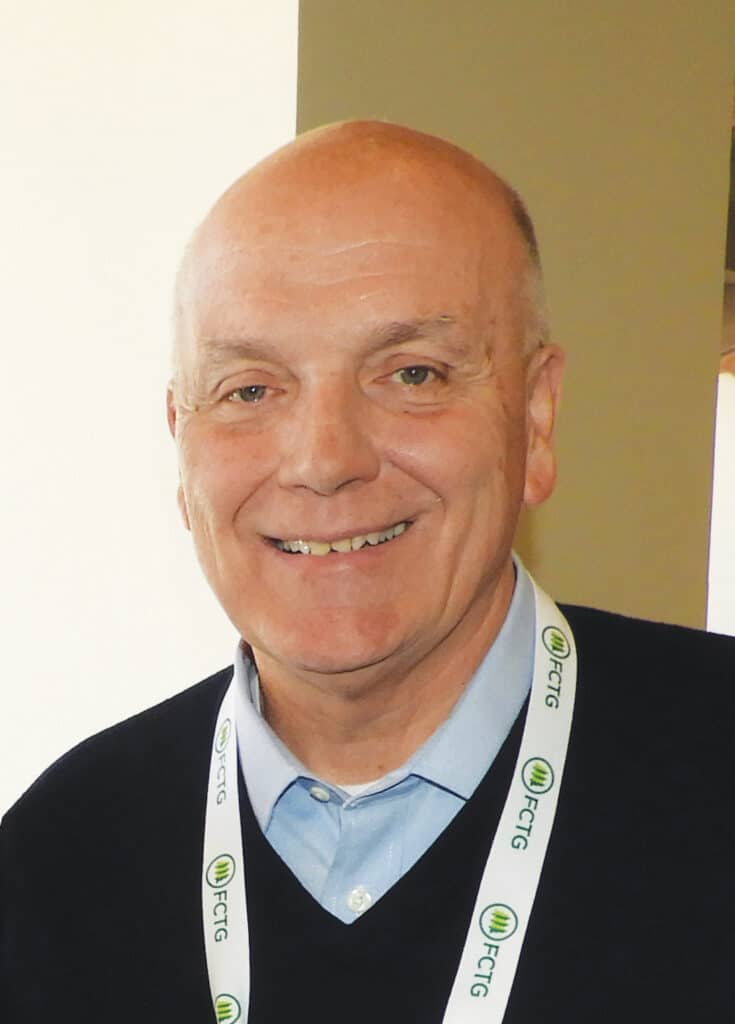
Woodgrain Acquires Trimco Millwork
Woodgrain, a leading millwork and building products company, recently announced the acquisition of Trimco Millwork. The transaction closed in December.
With the acquisition of Trimco Millwork, Woodgrain will increase its distribution center network to 35 locations expanding Woodgrain’s national footprint into the Rocky Mountain West. Trimco is a wholesale distributor of moulding, exterior doors, interior doors and other specialty building products with three locations in Boise, Idaho; Salt Lake City, Utah; and Denver, Colorado.
Kelly Dame, President and Chief Executive Officer of Woodgrain stated, “We at Woodgrain have admired Trimco for many years and acknowledge the Hoff family legacy, and are proud to continue that legacy as a family-owned company. We believe that we will be better together.”
Woodgrain is family-owned and one of the leading millwork and building products operations in the world with locations throughout the United States and Chile. With 69 years of quality craftsmanship and service, Woodgrain is a leading producer of moulding, doors, and windows, as well as a premier distributor of specialty building products.
Woodgrain, Inc. is headquartered in Fruitland, Idaho with six divisions and over 45 manufacturing and warehouse facilities in the United States and South America. For more information, visit www.woodgrain.com.
Specialty Building Products and James Hardie Building Products Expand
Distribution Partnership
Specialty Building Products, LLC (SBP), located in Duluth, GA, a leading distributor of specialty building products in North America, recently announced that it will expand its distribution partnership with James Hardie Building Products (James Hardie), the world leader in fiber cement siding and backerboard solutions.
SBP will now carry the entire range of James Hardie siding and trim products in its Oklahoma City, Kansas City and St. Louis distribution centers, increasing its number of stocking distribution centers to 14.
Specialty Building Products is at the core of the value chain for high value specialty building materials. Its operating brands – US Lumber, Alexandria Moulding, DW Distribution, Millwork Sales, Amerhart, and Reeb – provide sales, marketing, manufacturing, assembly, customization, finishing and logistics solutions that bring a wide range of high value, SKU-intensive, and logistically complicated specialty building products to dealers serving the repair and remodel (R&R) and new construction marketplaces.
SBP’s brands’ best-in-class operations are managed under a centralized strategy and informed by big data and analytics, serving the most respected manufacturers of the best and most innovative brands in the building products industry and local, regional, and national building material dealers, national one step distributors, national retail chains and industrial and OEM manufacturers.
More information can be found at www.specialtybuildingproducts.com.
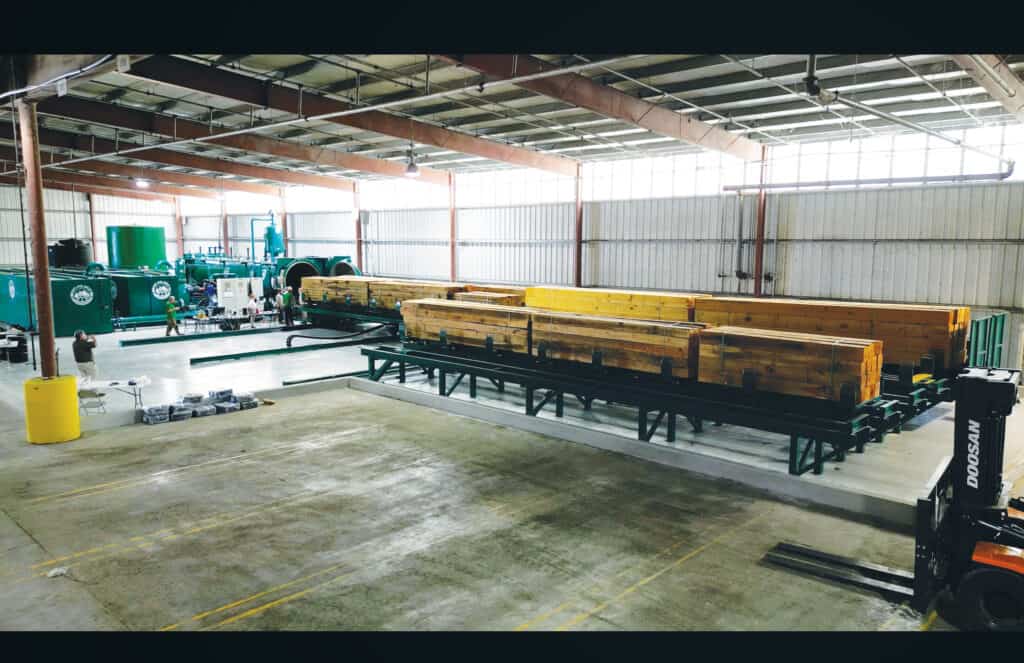
IWT-MOLDRUP Installs First CCA Turn-Key Plant In The U.S.
The first U.S. CCA turn-key plant was installed by 3rd generation supplier IWT-MOLDRUP, located in Vejle, Denmark, at LeMoyen Mill & Timber LLC. The CCA plant, the MOLDRUP T20, was up and running within a week and is integrated with a fully automatic system with a material handling, hold down clamps, tilting cylinder and tilt bays that can be safely operated by one man.
As the first U.S. CCA plant with the capability of wood impregnation, it is one of the highest possible work-safety and time-saving operations that can be delivered with fully integrated automatic material handling from the supplier of wood treatment equipment, MOLDRUP.
The MOLDRUP plant is equipped to work with several types of water-borne preservatives including an automatic flushing/cleaning system when changing between the preservatives.
It is a state-of-the-art plant capable of treating 8,500 board feet per cycle, and an automatic handling system that can handle up to 170,000 board feet per day and 47,600,000 board feet per year with just one plant operator.
“These new MOLDRUP treating plants have important technical features that cannot be gotten elsewhere,” said Lone Moldrup, CEO of IWT-MOLDRUP. “Another thing is that other suppliers are only dealing with the iron production whereas MOLDRUP has experience spanning over three generations that enables our company to have the know-how in process technology, machinery, wood species and have very good cooperation with the chemical suppliers.”
For more information you can contact IWT-MOLDRUP’s North American agent Claus Staalner, American Wood Technology, at 404-520-0239 or via www.americanwoodtechnology.com or www.moldrup.com.
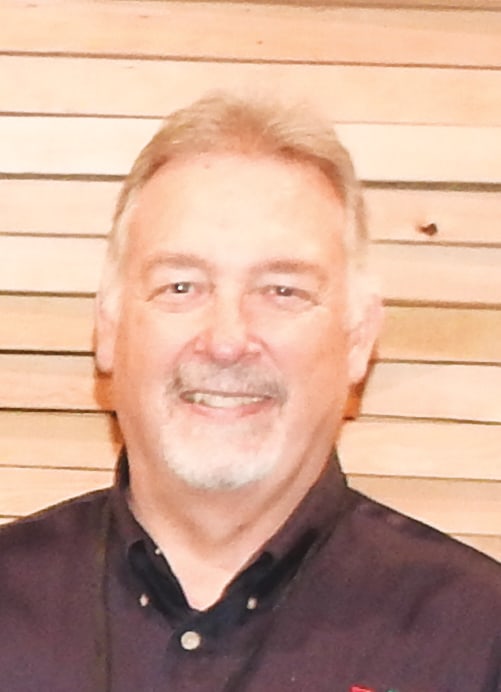
Bernhardt Named As
Executive Director For
Western Wood Preservers
Institute
Butch Bernhardt has been named as the executive director of Western Wood Preservers Institute (WWPI), located in Vancouver, WA.
Bernhardt has been with WWPI since 2014 and has held a variety of responsibilities within the Institute. He brings nearly four decades of experience and knowledge in the wood products and treating industries, holding positions at WWPI, North American Wood Pole Council, Western Wood Products Association and Western Red Cedar Lumber Association.
Bernhardt replaces Jeff Keller, who is no longer with the Institute.
WWPI represents preserved wood product producers, chemical manufacturers, wood manufacturers and others serving the wood infrastructure and building industry throughout western North America.
For more than 75 years, WWPI has provided services to the wood treating industry on legislative, regulatory, building codes and market issues aimed at sustaining healthy forests and ensuring critical infrastructure is safe.
For more information visit www.wwpinstitute.org.
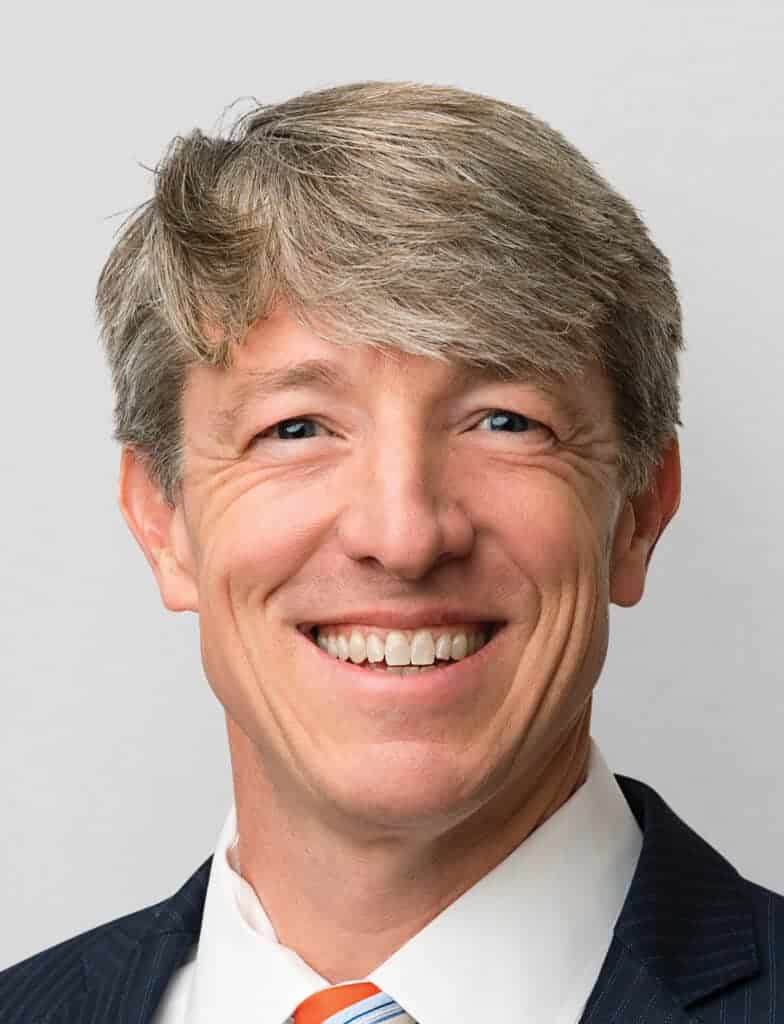
President & CEO of the American
Wood Council
Industry CEOs Warn of Dire Economic Consequences from Proposed NAAQS
Standards
Jackson Morrill, president and CEO of the American Wood Council, located in Washington, DC, recently joined leaders of over 70 other trade groups representing diverse businesses across the economy in urging the Biden administration to maintain the existing National Ambient Air Quality Standards (NAAQS) for fine particulate matter (PM2.5). In a letter to White House Chief of Staff Jeff Zients, the organizations warned that moving forward with the Environmental Protection Agency’s (EPA) proposed revisions would jeopardize American jobs and risk substantial economic harm.
The proposed revisions to the standard “would risk jobs and livelihoods by making it even more difficult to obtain permits for new factories, facilities and infrastructure to power economic growth,” the groups wrote. “This proposal would also threaten successful implementation of the Infrastructure Investment and Jobs Act, the CHIPS and Science Act, and the important clean energy provisions of the Inflation Reduction Act. Our members have innovated and worked with regulators to significantly lower PM2.5 emissions and further progress is being made as part of the energy transition investments.”
The letter emphasized the effectiveness of the current standards which have led to a 42 percent decline in PM2.5 concentrations since 2000, according to government data. In fact, the EPA reaffirmed only two years ago that the current standards are protective of public health and the environment. Now, without significant new health information, the agency is proposing revisions that will have dramatic effects on the U.S. economy.
A recent Oxford Economic analysis commissioned by the National Association of Manufacturers found that the proposed standard would reduce U.S. GDP by nearly $200 billion and cost as many as one million American jobs through 2031.
“Lowering the current standard so dramatically would create a perverse disincentive for American investment,” the letter reads. “EPA’s proposal could force investment in new facilities to foreign countries with less stringent air standards, thereby undermining the Administration’s economic and environmental goals.
We urge you to ensure EPA maintains the existing fine particulate matter standards to ensure both continued environmental protection and economic growth.”
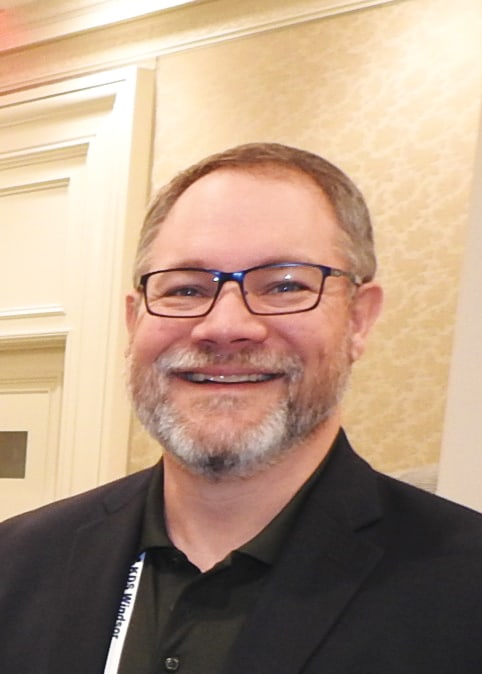
SFPA Visits Thailand For A Wood Seminar And Trade Opportunities
According to the Southern Forest Products Association (SFPA), with the loss of tens of millions of dollars in export sales to China, the U.S. wood industry is looking for alternative markets. That’s why Eric Gee, executive director of SFPA and Jerry Hingle, SFPA international consultant, traveled to Thailand recently for a wood seminar and trade opportunities mission.
Thailand is an attractive emerging market for Southern Pine as furniture manufacturers operating in China shift production to Thailand and elsewhere in Asia. Furniture production presents the best prospect for U.S. Softwoods in Thailand, as much of the production there is exported to the U.S., Europe and Japan, where buyers prefer Softwood furniture compared to tropical hardwoods that appear “heavy” and dark.
However, the sustainability and legality of tropical woods in Thailand can be dubious, so using U.S. Softwoods makes it considerably easier to prove sustainability and legal origin as the U.S. and Europe tighten regulations on wood components used in imported furniture.
Other end-use opportunities, include wood pallets, doors and flooring. While more homebuilders are embracing imported Softwoods for wood-frame homes, this is still considered a niche, as builders rely almost exclusively on concrete and steel. Manufacturers typically source logs for processing at their facilities rather than lumber, as low average wages provide little incentive for large, well-financed operations to outsource finished lumber.
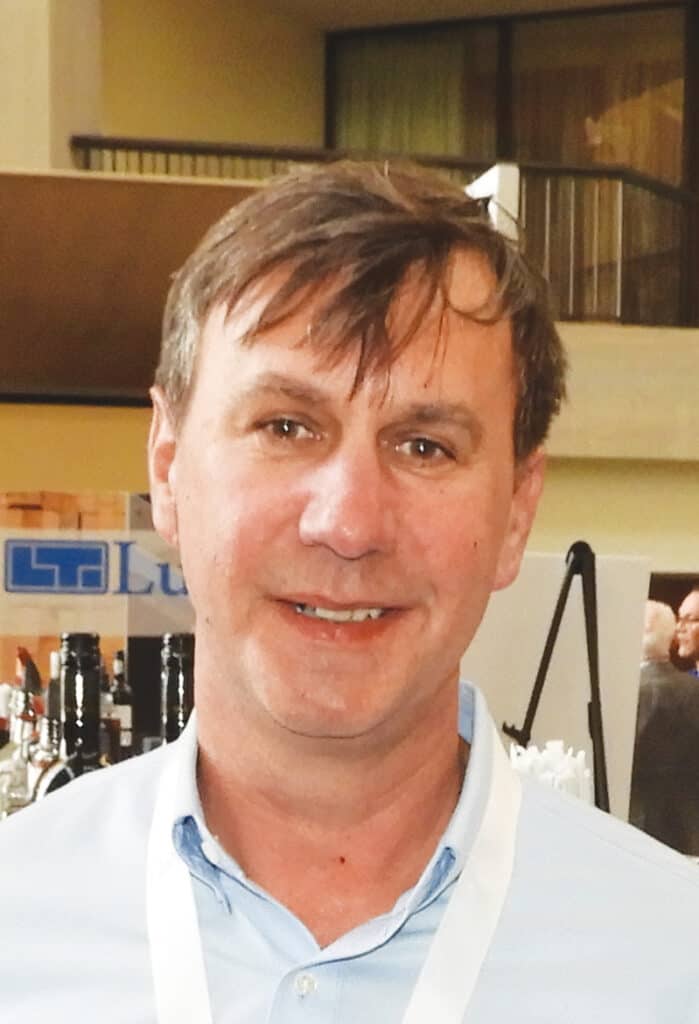
Lumber imports are growing, and what little Softwood lumber they source is primarily supplied by New Zealand, Canada and the U.S. Thailand imported $622,000 of Softwood lumber from the U.S. in 2022 but exports, including treated lumber, are up by 172 percent through September 2023 over the previous year.
This trip allowed Gee and Hingle to meet with prominent importers/traders for valuable insight into the current landscape of the wood industry, including learning about existing challenges and uncovering potential avenues for collaboration with SFPA.
They had productive and informative meetings with key lumber traders and specifiers at Interwood and CPD sawmill, BP Group Timber Processing Plant and numerous furniture purveyors. Numerous questions centered on lumber prices and the desire to procure logs instead of sawn lumber.
Gee and Hingle also hosted a seminar in Bangkok for 42 participants, which included lumber traders, architects and furniture manufacturers.
Gee spoke on Southern Pine lumber grades, sustainable forestry practices and why wood is a smart climate choice. Hingle presented on Southern Pine lumber characteristics, design considerations for areas prone to high wind and earthquakes, pressure-treated wood and termite prevention.
SFPA considers the seminar and one-on-one meetings to have been productive and informative. Going forward, SFPA will consider a more focused look at wood used in furniture manufacturing and less emphasis on wood-frame construction.
For more information visit www.sfpa.org.