Vaagen Bros. Upgrades Colville Mill With USNR’s Multi-Track Fence And VerifEye Systems
Vaagen Brothers Lumber, located in Colville, WA, recently improved their final board position and trim accuracy with the combination of USNR’s Multi-Track Fence and VerifEye fence verification system. These upgrades to
Vaagen Brothers’ system aim to drastically reduce the amount of starting and stopping, as well as improve the overall product.
The Multi-Track Fence offers a unique approach for Vaagen Brothers, acting as a “pusher-style” system. This utilizes the Fence Paddle to transfer lumber in the opposing offset.
Once the Multi-Track Fence accurately lines up the board, it’s sent to the VerifEye system to measure the board ends and compare their position accuracy with the optimizer’s solution, verifying the board’s end location is within error tolerance. The key to accuracy is in the laser array the VerifEye system uses, as opposed to a single point. It provides a better 3D image regardless of defects or sniped ends and produces a histogram along with the standard deviation and means for all trend data.
For more information, visit www.vaagenbros.com or www.usnr.com.
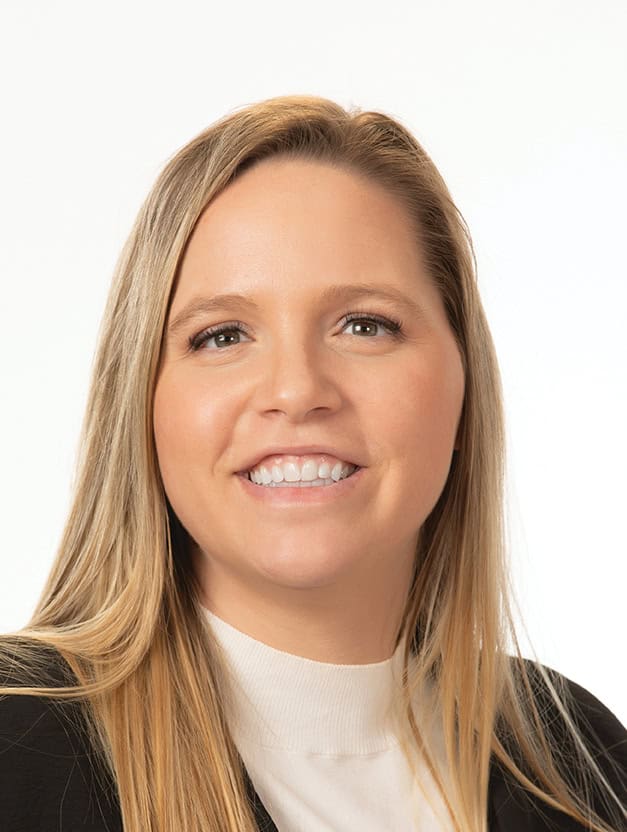
RoyOMartin Named Jennifer Forest Their New Chief Financial Officer, Strategic Action Leadership Team Member
Recently, Chairman and CEO Roy O. Martin III, announced that Jennifer Forest had been elected by the Martin Sustainable Resources (MSR) Board of Directors as the chief financial officer (CFO) of MSR and its wholly-owned subsidiaries, Martco L.L.C., which has multiple locations across Louisiana, and Martin Timberlands L.L.C., in Alexandria, LA. MSR has also appointed Forest to the organization’s Strategic Action Leadership Team (S.A.L.T).
Forest earned a Bachelor of Science in Accounting from Louisiana College in Pineville, LA, and a Master of Accountancy from Louisiana State University in Baton Rouge, LA. She became a certified public accountant soon after graduation. Forest joined RoyOMartin, located in Alexandria, LA, in 2014 as an internal auditor and soon after, she became a certified internal auditor. Most recently, she served as the controller of Martco L.L.C.
As CFO, Forest’s duties will be, first and foremost, protecting corporate assets in all ways. She will also oversee all financial operations of the company including oversight of accounting, budgeting, financial analysis and financial reporting of all Martco, Martin Timberlands and Martin Sustainable Resources L.L.C.
For more information, visit www.royomartin.com.
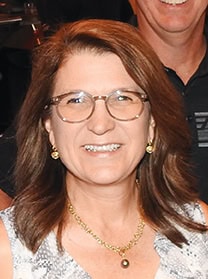
PotlatchDeltic Announces Waldo, AR, Sawmill Construction Completed
PotlatchDeltic Corporation has completed the planned downtime at the Waldo, AR, sawmill to tie-in equipment for the modernization and expansion project. The modernization project construction has been completed and the facility is beginning its ramp-up phase, and it is anticipated that it will take 6 to 12 months to reach the mill’s new dimensional lumber capacity of 275 million board feet per year.
The Waldo modernization and expansion project is a $131 million strategic investment that is expected to increase the mill’s annual capacity by 85 million board feet, improve recovery by six percent and reduce cash processing costs by approximately 30 percent. Once the ramp-up phase is completed, the mill is expected to generate approximately $25 million incremental adjusted earnings before interest, taxes, depreciation and amortization annually under a mid-cycle sales environment and an internal rate of return of approximately 22 percent in the company’s base case.
PotlatchDeltic has collaborated with Comact for this turnkey project. The project includes a new saw line, planer upgrade and a new continuous kiln. In addition, a Fulghum Industries, Inc. 170-foot 45-ton log crane was installed and commissioned as part of the modernization.
“I am very appreciative of the PotlatchDeltic and Comact team members for their relentless efforts and focus on safety during this project. The productive working relationship with Comact and the contributions by the suppliers and contractors on this project were an essential part of the on-time start-up,” said Ashlee Cribb, vice president of wood products at PotlatchDeltic.
PotlatchDeltic Corporation is a leading Real Estate Investment Trust (REIT) that owns over 2.1 million acres of timberlands in Alabama, Arkansas, Georgia, Idaho, Louisiana, Mississippi and South Carolina. Through its taxable REIT subsidiary, the company also operates six sawmills, an industrial-grade plywood mill, a residential and commercial real estate development business and a rural timberland sales program. PotlatchDeltic, a leader in sustainable forest management, is committed to environmental and social responsibility and to responsible governance.
More information can be found at www.potlatchdeltic.com.
Hancock Lumber Expands Manufacturing Capabilities With Tiny Homes Of Maine Acquisition
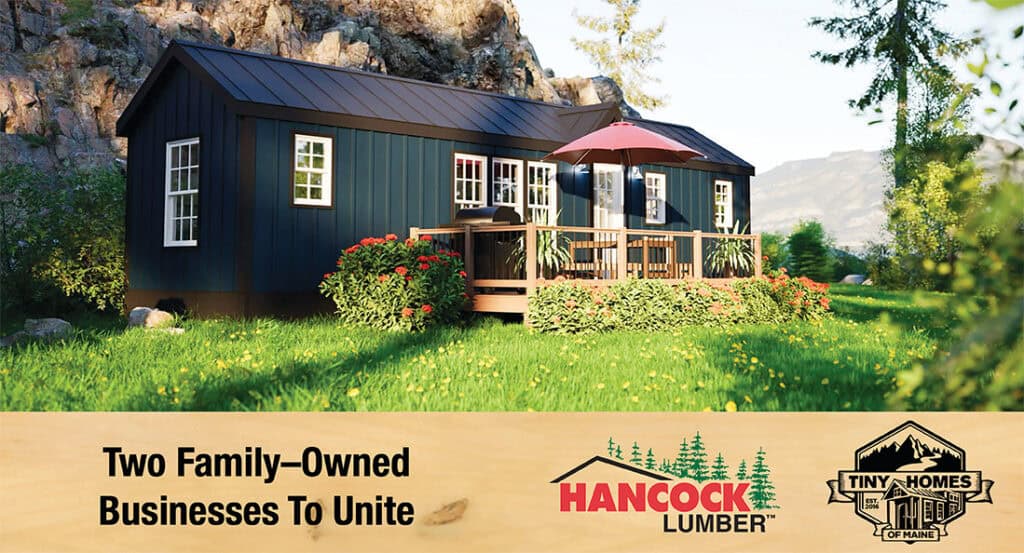
Hancock Lumber acquired Tiny Homes of Maine, an Aroostook County-based manufacturer of tiny homes on wheels, at the end of October.
The acquisition of Tiny Homes of Maine is a natural extension of Hancock Lumber’s manufacturing capabilities that includes Mainely Trusses roof and floor component manufacturing, wall panel production and their Eastern White Pine sawmills. An emerging segment of the housing market, tiny homes and accessory dwelling units help accelerate the building cycle and provide more affordable and flexible housing options. Together the teams will be able to leverage Hancock Lumber’s buying power, network of lumberyards and customers and manufacturing expertise to scale and grow the business while honoring Tiny Homes of Maine’s mission to make the tiny home dream attainable for more individuals.
A family-owned business established in 2016, Tiny Homes of Maine has built the business and brand designing, selling, manufacturing and delivering finished tiny homes, defined as movable structures that are 400 square feet or less. Current co-owners and co-founders, Corinne Watson and Tom Small, will plan to continue with Team Hancock and manage the Dyer Brook, ME, based manufacturing facility, daily operations and team.
Being in the lumber business since 1848 says more about Hancock Lumber’s commitment to the future than it does about their past, according to a company representative. Led by over 700 employees, Hancock Lumber has been named a ‘Best Place to Work’ since 2014, a testament to the energy and work they put into creating a culture that truly makes a difference.
For more information, visit www.HancockLumber.com.
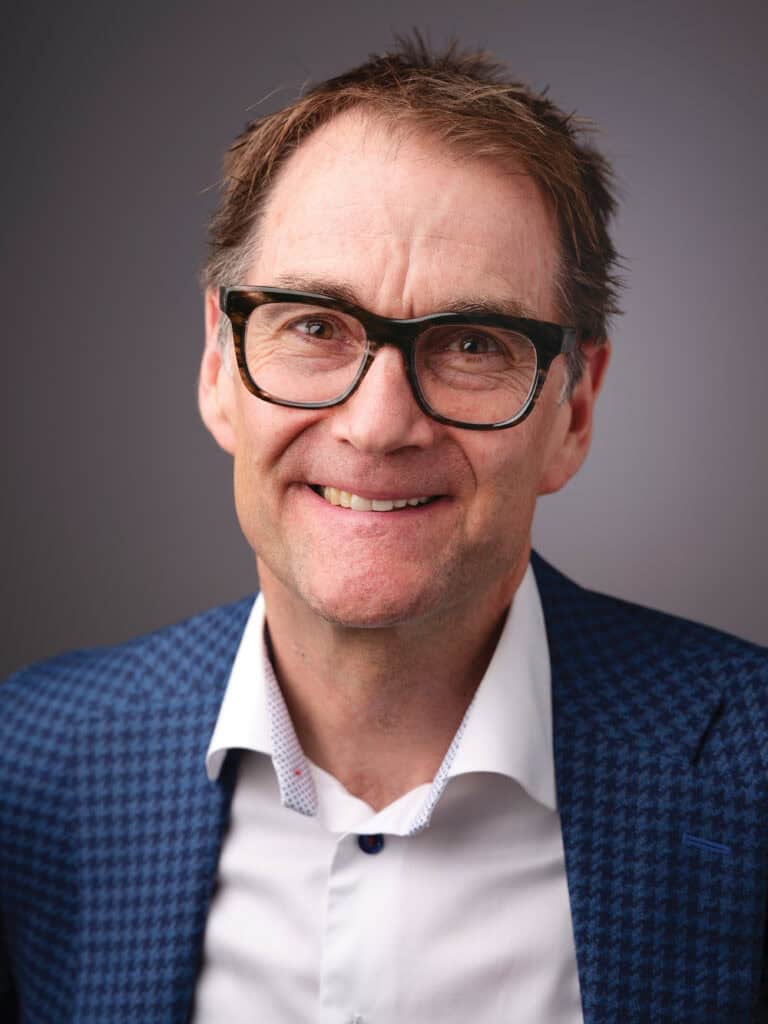
Tolko Industries’ Brad Thorlakson Receives 2024 Lifetime Achievement Award from Canada’s Forest
Products Sector
Forest Products Association of Canada (FPAC) presented its 2024 Awards of Excellence at the National Arts Centre in Ottawa recently, with Tolko Industries’ Brad Thorlakson being awarded the 2024 Lifetime Achievement Award.
The Lifetime Achievement Award celebrates visionary leaders who have made remarkable and sustained contributions to the forest products sector.
“Brad Thorlakson’s impact on the forest sector and on FPAC has been profound. He has guided Tolko Industries, a proud BC-based family business, for many years with visionary leadership and a deep commitment to Tolko employees, community well-being, and sustainability,” said Derek Nighbor, FPAC president and chief executive officer (CEO).
Thorlakson served as Tolko’s president and CEO from 2010 to 2024 before transitioning to the role of Executive Chairman.
He began his career at the Lavington Planer Mill, rising through the ranks to become vice president of marketing and sales before assuming the role of president and CEO. As the third generation of the Thorlakson family to lead Tolko, he has been instrumental in guiding the company’s growth while maintaining its core values of safety, sustainability, and excellence in product delivery.
FPAC provides a voice for Canada’s wood, pulp and paper producers nationally and internationally in government, trade and environmental affairs. As an industry with annual revenues exceeding $97 billion, Canada’s forest products sector is one of the country’s largest employers operating in over 600 communities, providing 200,000 direct jobs, and over 370,000 indirect jobs across the country.
For more information, visit www.tolko.com or www.fpac.ca.
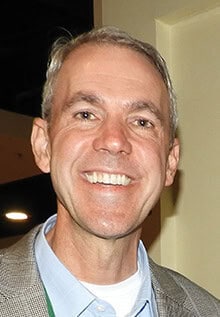
Culpeper Wood Preservers Acquires Long Life Treated Wood
Culpeper Wood Preservers, based in Culpeper, VA, a leading manufacturer of pressure-treated lumber, has acquired Long Life Treated Wood, a Maryland-based supplier and manufacturer specializing in marine-grade lumber. This acquisition bolsters Culpeper’s marine division and enhances its ability to serve customers with durable, high-quality products designed for harsh water environments.
“The acquisition of Long Life Treated Wood allows us to continue our growth strategy to better service new and existing customers,” said Jonathan Jenkins, president of Culpeper Wood Preservers. “We are deeply grateful to both Pat and Tom O’Malley of Long Life Treated Wood for their trust and collaboration throughout the acquisition. We are committed to honoring the legacy they have built.”
Founded in 1977, Long Life Treated Wood has established a reputation for manufacturing high-quality pressure-treated forest products with a commitment to outstanding customer service and integrity, paralleling the values of Culpeper. For more than 40 years, the company has operated on Maryland’s eastern shore, serving the region with high-quality Southern Yellow Pine pilings, timbers and lumber with a focus on marine applications.
“At Long Life Treated Wood, we have always been focused on doing business honestly and putting the customer first,” said Pat O’Malley. “Culpeper maintains that same commitment as a business. Our customers will be in great hands with them, and we wish Jonathan and the team at Culpeper nothing but continued success.”
Culpeper Wood Preservers is one of the largest producers of pressure treated lumber in the United States. In 1976, Culpeper Wood Preservers started from a single location in Culpeper, VA. Today, the company is a leading manufacturer of pressure-treated products for the residential, commercial, industrial and marine markets. Culpeper Wood Preservers’ brand name products are sold exclusively through independent lumber dealers throughout the Mid-Atlantic, Northeast, Midwest and South.
For more information, visit www.culpeperwood.com.
Nyle Dry Kilns Installs Cutting-Edge Kilns at Steinkamp, Enhancing Production and Efficiency
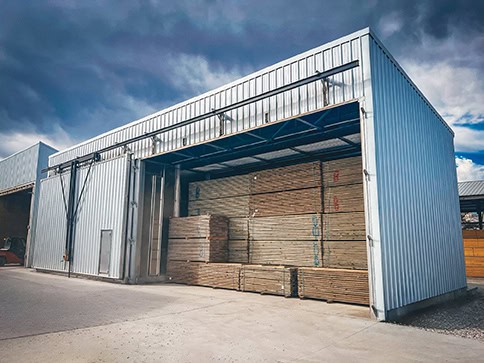
Nyle Dry Kilns announced the recent installation of two 65 thousand board feet Gas Kilns at Steinkamp’s in Huntingburg, IN. These kilns are specifically designed to handle treated softwood lumber, offering superior performance and efficiency for Steinkamp’s operations, according to a company spokesperson.
Each kiln is equipped with indirect-fired gas heaters and high-efficiency heat recovery vents. These features ensure optimal energy use and precise control over the drying process, providing consistent and high-quality results. The kilns’ advanced control systems allow for detailed data logging, remote access and enhanced operational efficiency.
This installation significantly upgrades Steinkamp’s operation, enhancing their production capacity and operational efficiency. According to Nyle Dry Kilns, Steinkamp has invested in top-tier technology that not only boosts their production capabilities but also aligns with sustainable and cost-effective practices. The successful completion of this project marks a significant milestone for Steinkamp, demonstrating their commitment to quality and innovation in the wood processing industry.
For more information on Nyle Dry Kilns’ wide range of products and services, visit www.nyle.com or call (800) 777-6953.

Bid Group Becomes Comact: Pioneering The Future Of Wood Processing
BID Group, a leader in the wood processing industry for over a century, is proud to announce its new identity as Comact.
This transition marks a significant evolution in the company’s journey and reflects its commitment to innovation and excellence. From its origins as an OEM, Comact has been instrumental in transforming the wood processing industry. The company has consistently invested in research and development, addressed customer challenges, and adapted to their evolving needs. Through strategic alliances and acquisitions of leading brands, Comact has established itself as a world-class leader and pioneer renowned for its high-performance technology and equipment and its exceptional customer engagement.
As Comact, the company will continue to focus on what matters most to its clients: optimizing operational performance, leveraging advanced technologies and delivering exceptional field support. The company’s comprehensive project services, including construction and installation, will continue without interruption.
The company also recently unveiled its new brand identity and logo, which embody its customer-centric approach and the robustness and high performance of its equipment.
The company is gradually implementing the new brand across all touchpoints. Customers, partners and stakeholders can expect a seamless transition with no disruption to its operations.
For over 100 years, Comact has been a leading OEM in high-caliber wood processing equipment, digital technologies, cutting solutions, project services and aftermarket support. Whether for brownfield or greenfield projects, Comact’s expertise provides wood processing facilities with the confidence that their investments will yield superior performance, throughput and ROI, stated a company representative. This ensures they remain competitive and achieve sustained growth in an ever-evolving market.
For more information, visit www.comact.com.
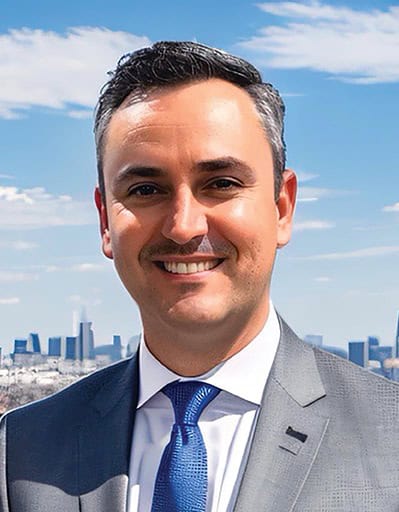
The AGL Group Welcomes Adis Nadarevic As Their Newest Drayage Analyst
Adis Nadarevic recently joined The AGL Group as a drayage analyst, where he is poised to make a significant impact on the company’s drayage operations. In his new role, Nadarevic is responsible for optimizing drayage processes, analyzing performance metrics, and developing strategies to enhance efficiency and cost-effectiveness.
His expertise aims to drive the success of AGL’s drayage program and foster continuous improvements in service delivery.
Nadarevic graduated from Englewood High School in Jacksonville, FL, before earning a bachelor’s degree in finance from the University of North Florida. With nearly a decade of experience in the Transportation and Logistics sector, Nadarevic has established a strong track record in freight management and transportation coordination. His career commenced as a freight specialist at a brokerage firm, and he further honed his skills at Florida East Coast Rail, managing transportation operations across Jacksonville, Atlanta and Charlotte. This background underscores his capability to navigate complex logistical challenges and deliver operational excellence.
Prior to his focus on transportation and logistics, Nadarevic accumulated valuable experience in the financial services sector, including roles in auto finance and the mortgage industry. This diverse background has endowed him with a keen analytical perspective and a thorough understanding of financial management, which he now applies to enhance logistics operations and improve financial outcomes for AGL.
Outside of his professional pursuits, Nadarevic is an avid soccer enthusiast and a dedicated supporter of Manchester United. He enjoys attending various sporting events, such as soccer, basketball and football. Nadarevic shares his life with his fiancé of eight years and their Golden Retriever. Together, they value time spent at home, visiting the beach and engaging in other leisure activities.
For more information, visit www.theAGLgroup.com.
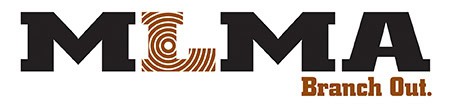
Mississippi Lumber Manufacturers Association Endow Professorship
Mississippi’s expansive forests have long been a bedrock of the state’s economy, with the timber industry serving as a key driver of growth. However, as industries progress, there is a growing need to evolve practices and materials.
In partnership with the Mississippi Lumber Manufacturers Association (MLMA), the College of Architecture, Art, and Design (CAAD), the College of Forest Resources (CFR) and the Department of Sustainable Bioproducts at Mississippi State University (MSU) are spearheading efforts to ensure the state’s timber industry thrives in a changing world.
Timber remains one of Mississippi’s leading agricultural commodities, with the forestry industry supporting over 64,000 jobs and contributing $1.355 billion to the state’s economy. However, the industry faces challenges that limit its potential growth, particularly in adopting new technologies like mass timber. Mass timber, including innovations such as cross-laminated timber (CLT), can revolutionize construction by making wood a more viable and sustainable resource for building. Despite its benefits, CLT still faces obstacles to mainstream adoption.
To address these challenges, the idea of establishing an endowed professorship at MSU emerged. Established with the MLMA’s recent gift, the Mississippi Lumber Manufacturers Association Endowed Professorship in Innovative Wood Construction and Design aims to spread awareness and further research on mass timber as a viable and sustainable innovation for the timber industry.
The endowed professorship will focus on teaching, research and outreach, promoting CLT and other innovative wood technologies to the next generation of builders and producers. The objective is to ensure that students not only learn these technologies but also engage in research and real-world applications.
Through the partnership between MSU and the MLMA, Mississippi is poised to become a leader in sustainable construction. This collaboration is not just about developing new technologies; it’s about reimagining timber’s role in the future of construction.
For more information, visit www.mlmalumber.com.
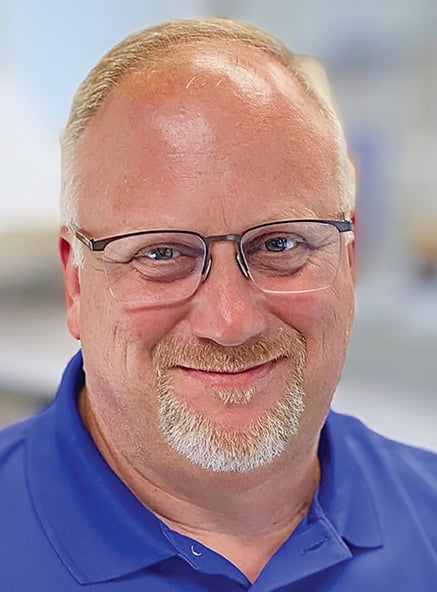
LMC Named Tedd Cartwright As New Purchasing Manager
LMC, located in Wayne, PA, recently announced the promotion of Tedd Cartwright to purchasing manager, overseeing the treated lumber, Southern Yellow Pine and components/B2B departments. In this expanded role, Cartwright will manage these three departments within the lumber division, reporting directly to Chris Ford, vice president of the lumber division.
With over 29 years of experience in the industry, Cartwright brings deep market and product knowledge, a strategic approach and many strong relationships. Cartwright began his career at LMC in 2001 as a trader in the treated lumber department. He later transitioned to the East/West commodity lumber department before being promoted in 2016 to department manager of Southern Yellow Pine.
As purchasing manager, Cartwright will focus on developing innovative programs and initiatives that strengthen LMC’s Dealer network. His leadership will ensure that LMC’s independent dealers remain central to the company’s strategy, reaffirming its commitment to helping them thrive in today’s competitive marketplace.
“I’m excited to play a larger role in helping to shape LMC’s future,” said Cartwright. “Our mission is about more than competitive purchasing strategies—it’s about empowering the independent lumberyards that serve local communities. By supporting these dealers, we contribute to stronger economies and make a meaningful impact in the lives of the people they serve.”
Cartwright’s extensive expertise in the Southern Yellow Pine market, combined with his ability to build strong relationships with suppliers, staff and dealers, positions him to drive significant growth in his new role.
LMC is a leading forest products and building materials buying group in the USA owned by independent lumber and building material dealers. There are over 1,800 LMC dealer locations in the United States. “Building Business Together” is LMC’s philosophy, rooted in a history of working together and standing the test of time since 1935.
LMC dealers are united in their purchasing, creating a strong foundation that supports the growth of unique supplier relationships and purchasing opportunities.
To learn more about LMC, visit www.lmc.net.
USDA Announces Appointments to the Softwood Lumber Board
The U.S. Department of Agriculture (USDA) announced the appointment of six members to serve on the Softwood Lumber Board. The appointees will serve three-year terms beginning January 1, 2025, and ending December 31, 2027.
Newly appointed members are:
- Trey Hankins, Ripley, MS (flex seat)
- Kimberli C. Scott, Allendale, SC (flex seat)
- Marc Brinkmeyer, Coeur d’Alene, ID
- Vaughn Emmerson, Anderson, CA
- Susan Yurkovich, Vancouver, BC
- Jerome Pelletier, Saint John, NB (flex seat)
The Softwood Lumber Board has 14 members, including 10 domestic manufacturers and four importers. Members can serve up to two consecutive three-year terms.
“The Softwood Lumber Board would like to thank Secretary Vilsack for appointing a dynam-ic group of directors who reflect the diversity of the industry and the people that work in it, each bringing valuable insights from their respective regions,” said Cees de Jager, SLB pres-ident and CEO. “The SLB looks forward to working with the new Board to grow and diversify demand for softwood lumber products in the United States.”
Since 1966, Congress has authorized the development of industry-funded research and promotion boards to provide a framework for agricultural industries to pool their resources and combine efforts to develop new markets, strengthen existing markets and conduct im-portant research and promotion activities. Agricultural Marketing Service (AMS) provides oversight of 22 boards, paid for by industry assessments, which helps ensure fiscal ac-countability and program integrity.
AMS policy is that diversity of the boards, councils and committees it oversees should re-flect the diversity of their industries in terms of the experience of members, methods of production and distribution, marketing strategies and other distinguishing factors, includ-ing but not limited to individuals from historically underserved communities, that will bring different perspectives and ideas to the table. Throughout the full nomination process, the industry must conduct extensive outreach, paying particular attention to reaching under-served communities and consider the diversity of the population served and the knowledge, skills and abilities of the members to serve a diverse population.
For more information, visit www.softwoodlumberboard.org.
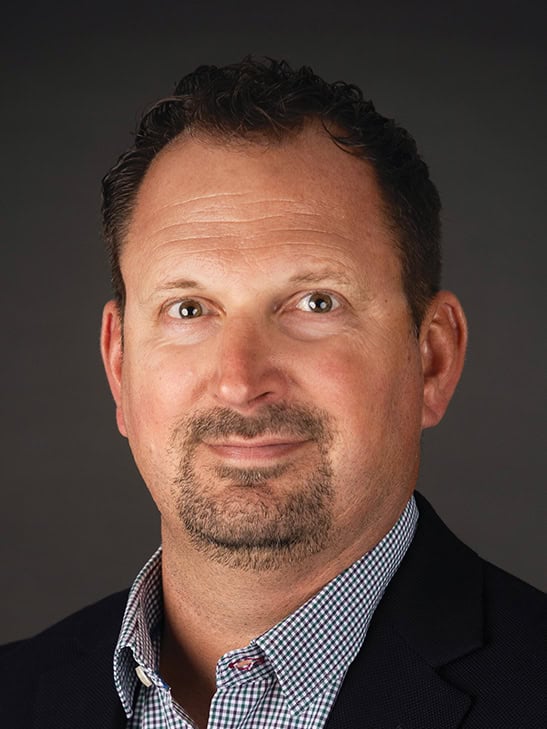
Landon Tarvin Named President of UFP Retail Solutions
UFP Industries, Inc. announced that Landon Tarvin has been selected to replace Will Schwartz as president of UFP Retail Solutions, effective December 29, 2024. UFP Retail Solutions is a business segment of UFP Industries that produces ProWood pressure-treated lumber, Deckorators composite decking and accessories, UFP-Edge siding and trim products, and Outdoor Essentials fence and garden products. Tarvin currently serves as vice president of Deckorators.
“We had many internal candidates who were qualified for this role, making it a difficult decision,” said Will Schwartz, who will replace Matt Missad as CEO on December 29, 2024.
Tarvin joined UFP Industries in 2002 as an account manager and advanced into roles of increasing responsibility, including senior account manager and sales manager, before becoming general manager of the company’s plant in Harrisonville, MO. In late 2019, he was named vice president of outdoor essentials. He was named to his current role of vice president of Deckorators in 2021.
UFP Industries, Inc. is a holding company whose operating subsidiaries – UFP Packaging, UFP Construction and UFP Retail Solutions – manufacture, distribute and sell a wide variety of value-added products used in residential and commercial construction, packaging and other industrial applications worldwide. Founded in 1955, the company is headquartered in Grand Rapids, MI, with affiliates in North America, Europe, Asia and Australia. UFP Industries is ranked #493 on the Fortune 500 and #128 on Industry Week’s list of America’s Largest Manufacturers.
For more about UFP Industries, go to www.ufpi.com.