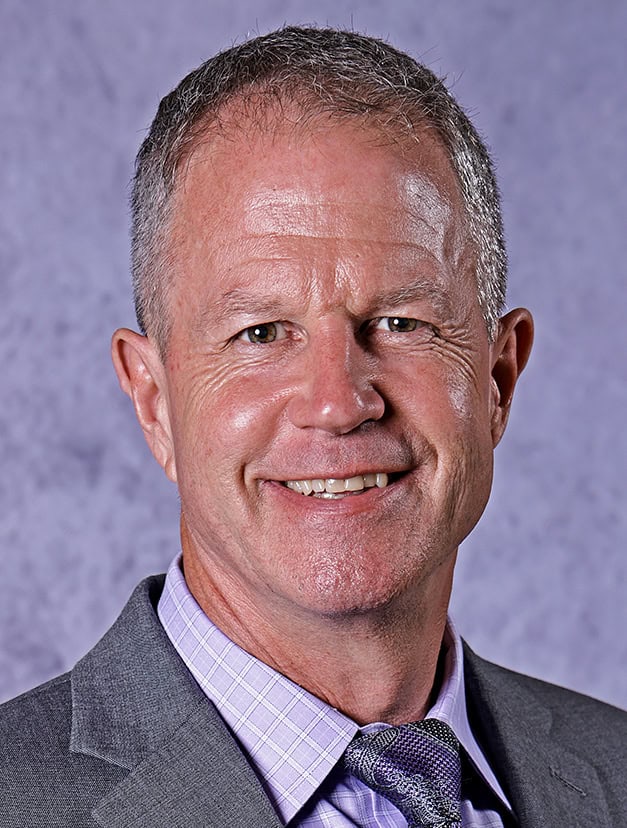
National Wood Flooring Association
NWFA.org
In the United States, most Hardwood comes from privately owned forests, and most privately owned forests are just a few hundred acres in size. Larger forests tend to be commercially owned operations. Hardwood forests are regenerated by natural cycle or by new plantings. As a general rule, it takes at least 40 years for an Oak tree to grow to maturity and to a size large enough to cut for useable lumber, but most Oak trees are harvested at about 60 years. This means the inventory is available an average of 20 years before it is needed or used.
Harvesting Lumber
When trees are harvested for wood flooring, the milling process usually works this way: First, the tree is selectively harvested from the forest. Only trees of the necessary height and diameter are selected. It is important to the health of the forest that these trees are removed before they start to decay, as decayed wood is not usable and no longer produces oxygen. In addition, clearing older trees allows younger trees to reach the forest canopy.
Next, the log is rough cut to the desired length. Maximum lengths are maintained whenever possible. All branches are cut (limbed) from the log. The logs then are removed from the forest, loaded onto logging trucks, and delivered to the mill yard.
Milling Lumber
The handling of the lumber when it gets to the mill is very important and is dependent on its intended end-use.
At the mill, the bark is first removed from the log. All bark, saw dust, and other non-usable wood fiber is collected and used for other purposes, like heating the facility or manufacturing wood pellets or mulch.
For sawn or sliced material, the rounded edges then are removed to produce a square log called a cant.
The square logs next are cut into wood slabs at a predetermined thickness, maximizing the usable lumber. The slab edges then are trued and trimmed square, creating what we typically call a lumber board.
Each board then is sorted by quality and classified by grade.
Drying Lumber
Like most biological entities, trees have a high water content. Water can comprise more than 2/3 the weight of a living tree. In order to use wood as a building material, most of this water must be removed. The natural removal of this water begins immediately after the tree is cut down, but is managed during the seasoning process.
After sorting, boards are stacked to facilitate air movement and begin the air-drying process. This is accomplished by placing small, thin boards called “stickers” between each stacked layer of wood. This maximizes air movement, which helps to bring the moisture content of the lumber into equilibrium with its surrounding environment. The temperature, humidity, and airflow will influence the time needed to reduce moisture content of the wood. The goal is generally to reach 18-30 percent moisture content.
Kiln-Drying Lumber
In order to get the lumber dried to a level appropriate for interior use, the lumber typically is dried in a kiln. A kiln is a large oven that provides a controlled environment that removes moisture using a combination of heat and airflow. Temperatures typically range from 100-180 degrees Fahrenheit and help to slowly remove moisture from the wood. Kilns typically dry the lumber down to a moisture content between 6-9 percent. Kiln drying also results in sterilizing the wood by destroying insects and fungi. This drying process will cause dramatic dimensional changes. As the cells of the tree dry, they shrink in thickness and/or diameter, but shrink very little lengthwise. Shrinkage and swelling in response to moisture — strain — is characteristic of both Hardwoods and softwoods.
The National Wood Flooring Association provides detailed information about harvesting, sawing, and seasoning lumber for wood flooring manufacturing in its Moisture and Wood technical publication. NWFA’s technical publications are provided to all NWFA members as a member benefit. They are available to nonmembers for purchase. NWFA also provides online training for wood flooring through NWFA University.
For more information, visit www.nwfa.org.