New technology and machinery has resulted in increased efficiency and smoother operations at Deer Park Lumber Inc., based in Tunkhannock, PA.
Deer Park Lumber recently installed a Pichè Inc. 60-bin sorter, as well as a Comact trimmer and grading scanner from BID Group Technologies Ltd. and PLC Controls from Logitech Controls. “These installations have made us more efficient,” said Joe Zona, sales and marketing manager. “Everyone has had struggles with getting employees and this takes a lot of the physical labor out of lumber handling. We have more technical positions now, where they need to know how to operate computers, automatic lumber stacking and stick placement, as well as how to troubleshoot the machine when a board is skipped and has become skewed.”
The new installations will increase Deer Park Lumber’s capacity as their employees become more proficient in the use of the new technology. The new Pichè sorter will allow them to sort two species at a time in both kiln-dried and green lumber as the computer continues to learn how to recognize different grades, species and colors. “It’s a 60-bin sorter with two rejects on each side, so we end up with 58 sorts,” said Bob Seidel, mill operations manager. “We used to only have 15 sorts on the grade side, so this has significantly improved our efficiency.”
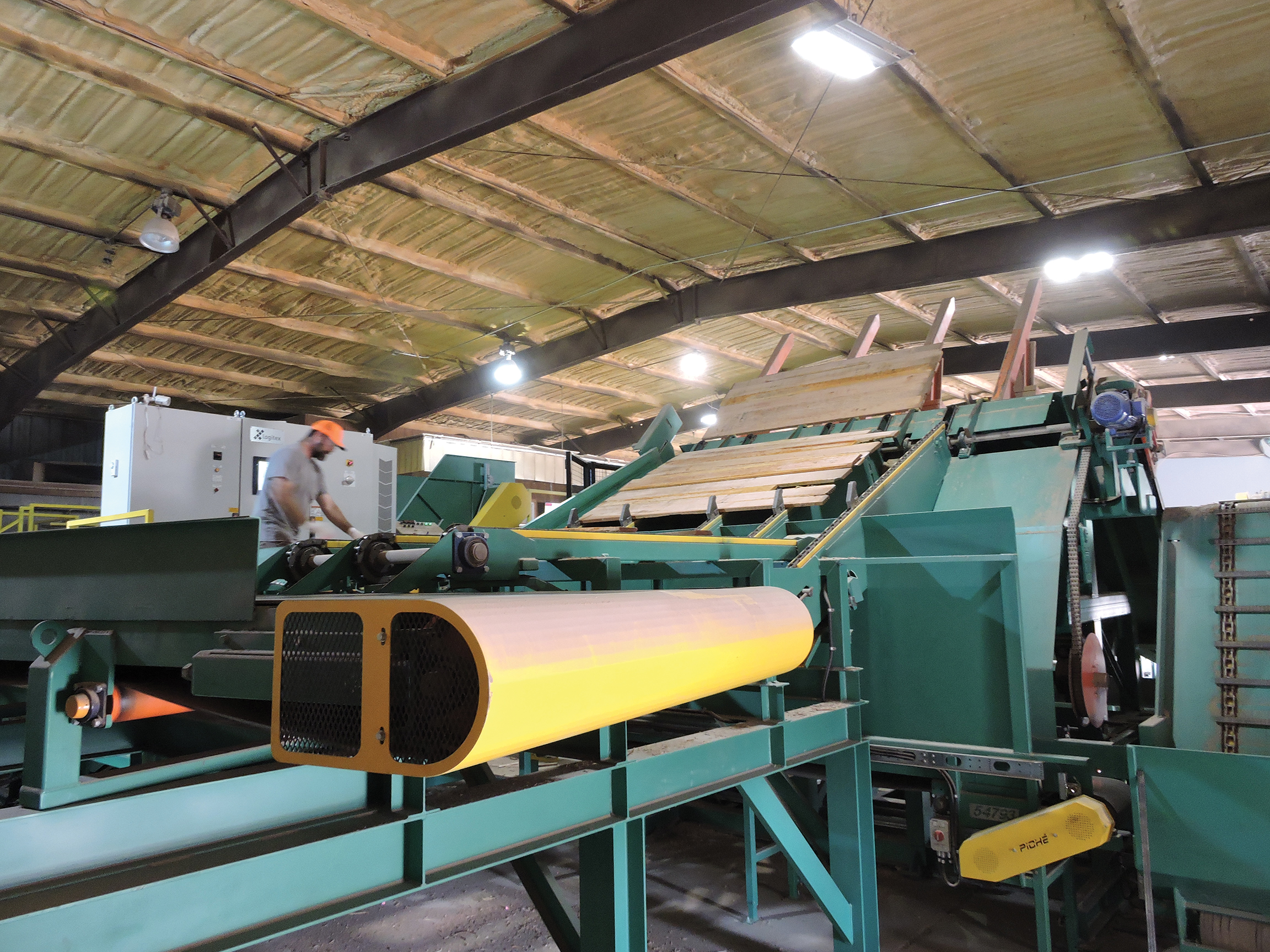
“We have the bins now to take all the green lumber that Jack Monnoyer has been buying, and re-enter it through the Comact, allowing us to trim the outside purchased lumber during our regular milling process,” said Zona. “We are cutting White Oak and re-entering Cherry. These boards aren’t sorted by grade, but by length, width and thickness and while they are being sorted we add the stickers.”
As the sorter bins become full, they dump down onto the decking and are transferred to a “trolley train” that goes to an unscrambler to the stacker where the boards are simulated and make six-foot course if they are being dried or a 42 inch dead piled pack if it’s going out green. “Everything is automatic, the course placement, course making, stick placement and scanning,” said Seidel.
Deer Park Lumber has made the switch to Duramax sticks from Redwood Plastics and Rubber Company located in Stockbridge, GA. “I know we are the wood guys and these sticks are plastic, but they stay straight and they are stronger. We don’t have to worry about moisture and they can be left outside in the rain and it doesn’t matter. They work and they feed well through the automatic machines,” said Zona. “We would have to throw away a lot of the wooden style sticks. The wooden sticks bowed during the drying process and they didn’t feed as well.”
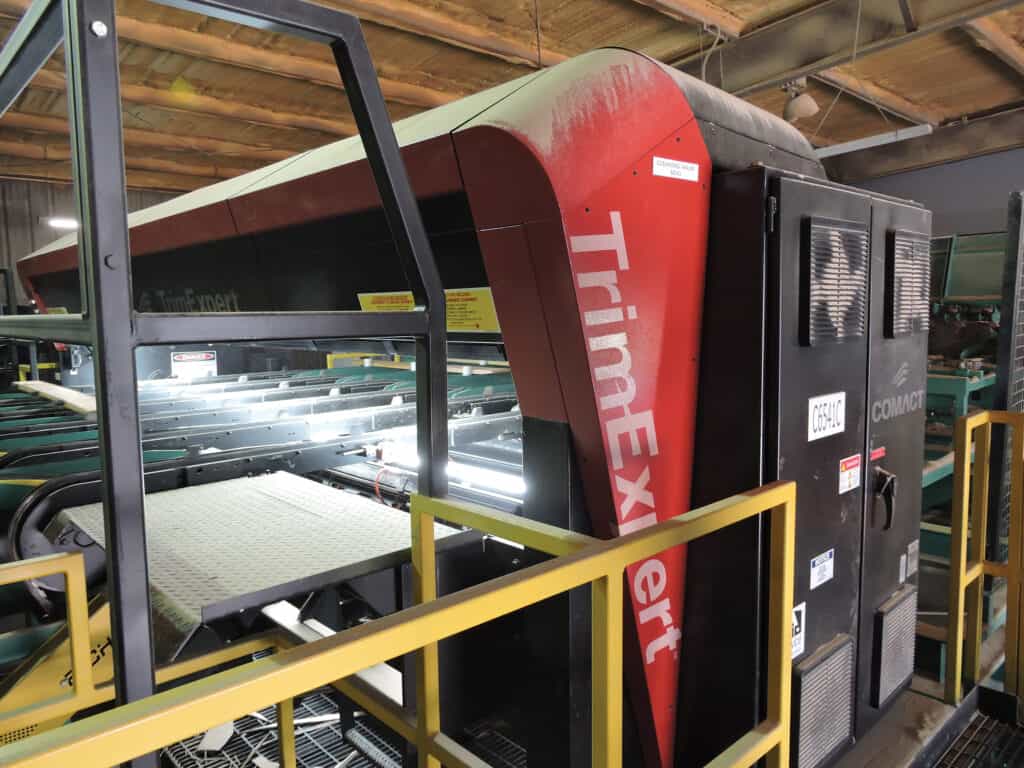
Deer Park Lumber’s facility has a total dry kiln capacity of 500,000 board feet and an annual production of approximately 12 million board feet. The average lumber inventory available is 2.5 million board feet. Log inventory is approximately 800,000 to 950,000 board feet to allow about a three-week turnaround, preventing defects and staining in logs.
Top-quality lumber begins with good inventory management. “We rotate the inventory as quick as we can, but we have a generous log supply and we are on in the summer months so, we use the black Shade-Dri®,” Zona said. “Black actually reduces the heat by 10 to 15 degrees in a log pile, which stops checking and staining. We also use U-C Coatings Corporation’s Anchorseal® on the lumber to wax and seal, and as we’re drying it we use 8-inch concrete rooftops that run through the drying process to keep the lumber flat. This is especially important for the top packages. The bottom packages get weight from all the other packages. The ones on top don’t have any weight unless we put these rooftops on them.
Deer Park Lumber ships globally and offers customer pickup at the mill, flatbed delivery and/or container loading for both railcars and export shipping. “We’re marketing to distribution yards and direct to furniture and kitchen cabinet manufacturers, both internationally and domestically,” Zona said. “We’re shipping into China, Italy, Germany, Vietnam, Indonesia, Japan, Malaysia, South Korea, mostly in Pacific Rim countries.”
Key personnel includes Joe Benko and Jack Monnoyer. Benko has worked at Deer Park Lumber for 12 years, he handles the sales of low-grade lumber, kiln-dried lumber and does some green purchasing. He also assists with logistics, trucking and accounts receivable. Monnoyer handles sales and purchasing of green lumber.
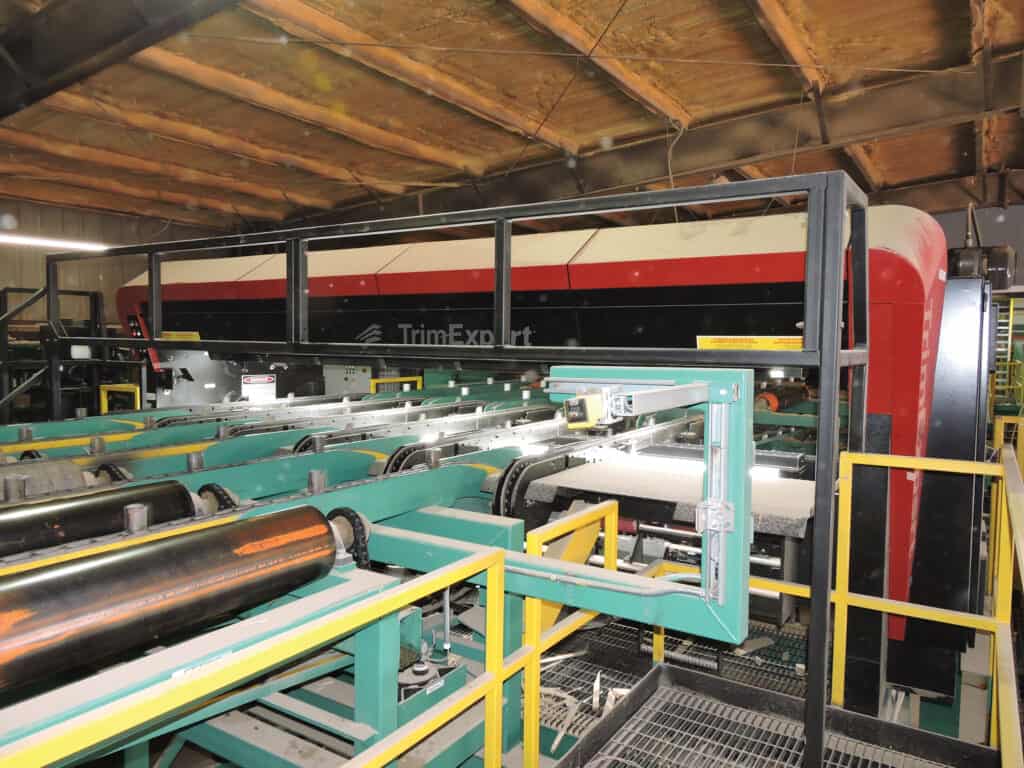
The Deer Park Lumber Construction Company purchased D & K Lumber Co. in August of 1972. The partnership incorporated in 1978 and became Deer Park Lumber Inc. By 1982 the firm was purchased by Ronald Andrews, who, according to the company’s website, would forever change the dynamics of the operation by leading the way for it to become the progressive business it is today.
Andrews and his family manage the business by promoting self-growth, customer service, harvesting quality timber, which in turn enables Deer Park Lumber to produce quality lumber. Because of his dedication to sustainable forestry, Andrews purchased and donated a truck and trailer for the WoodMobile, which travels Pennsylvania as an educational exhibit. This exhibit is displayed at schools and county fairs where people can learn about the forest and how it plays a part in our lives.
In 2011 Deer Park Lumber added a forestry division that helps individuals make informed decisions where their timber tracts are concerned, thereby preventing needless damage to forestry resources.Deer Park Lumber Inc. is a member of the National Hardwood Lumber Association, Pennsylvania Forest Products Association, Penn-York Lumbermen’s Club, Keystone Wood Products Association, Indiana Hardwood Lumbermen’s Association and Northern Tier Hardwood Association.
For more information, visit www.deerparklumberinc.com.