By Michelle Keller
Vancouver, BC–Hardwoods Distribution Inc. (HDI), located here, is a leading distributor of architectural decor materials, including lumber, decorative surfaces and composite panels, hardwood plywood and other architectural interior building products to the residential and commercial construction market.
This summer, HDI launched DesignOneSource, its new Specification Division. The new division is organized to provide the design and millwork community seamless specification support for decorative surface materials across North America by aligning leading global suppliers and front-of-trend interior decor products that adhere to the highest environmental standards. Supported by a vast internal information platform that can help a remote workforce enable collaboration, providing instant access to design inspiration, trend insight, vendor coordination, and training and technical product support.
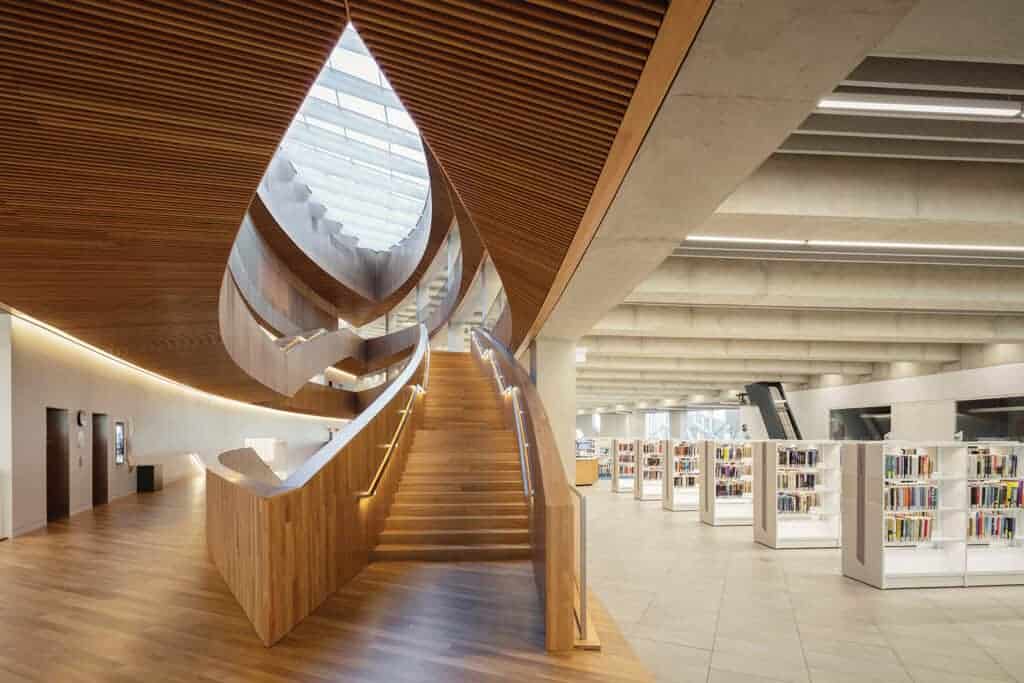
Hardwoods Specialty Products, Calgary division supplied its client Executive Millwork with 455,000 lineal feet of specially prepared Hemlock lumber for Calgary’s New Central Library. Hemlock lumber wood slats line the perimeter of the open atrium, shaped like a pointed ellipse, to help visitors to quickly grasp layout of the library.
HDI purchases millions of board feet in hardwoods annually. Hardwood species include alder, ash, aspen, basswood, beech, birch, cherry, cottonwood, cypress, hard and soft maple, red and white oak, walnut and poplar.
HDI also purchases Softwood species, including Hemlock, Sugar Pine, Ponderosa Pine, Douglas Fir and Willow.
HDI operates a network of distribution centers conducting business as Rugby Architectural Building Products, Hardwoods Specialty Products, the Frank Paxton Lumber Company, and HMI Hardwoods LLC.
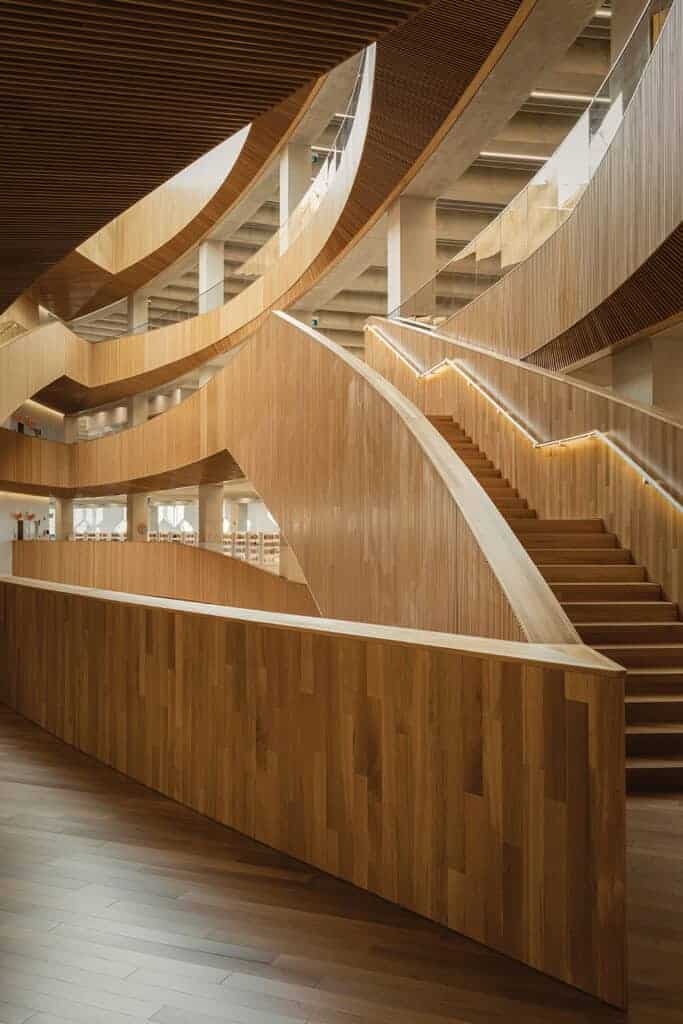
Vertical Hemlock lumber slats line the “Great Reading Room” to provide both privacy and visibility, defining an interior space without using solid walls.
HDI serves and supports over 40,000 customers across North America through its 66 distribution centers that combine for over 4,000,000-square-feet of warehouse and light manufacturing in a number of its distribution centers. HDI employs approximately 1,300 including about 500 sales personnel.
Over the past seven years, HDI has successfully acquired 49 U.S. locations and most recently the Diamond Hardwoods acquisition on March 9, 2020 with two locations, and on Oct. 29, 2019 the acquisition of the five locations of Pacific Mutual Door (PMD).
Organic growth at HDI is fostered in part by its access to a vast global supply of architectural décor materials coupled with the best of domestic production, together these materials are consolidated into its regionally located distribution centers, according to the company. Each of these distribution centers are carefully structured and aligned to meet the needs of its local community…no two are alike. The product assortment, depth of inventory, light manufacturing capability, and service profile of each facility is a reflection of the customer base it supports. Each of these factors are regularly evaluated to ensure that they are performing in accordance with customer expectations and as a result they are constantly being adjusted to ensure it exceeds customers’ expectations, according to a company spokesperson.
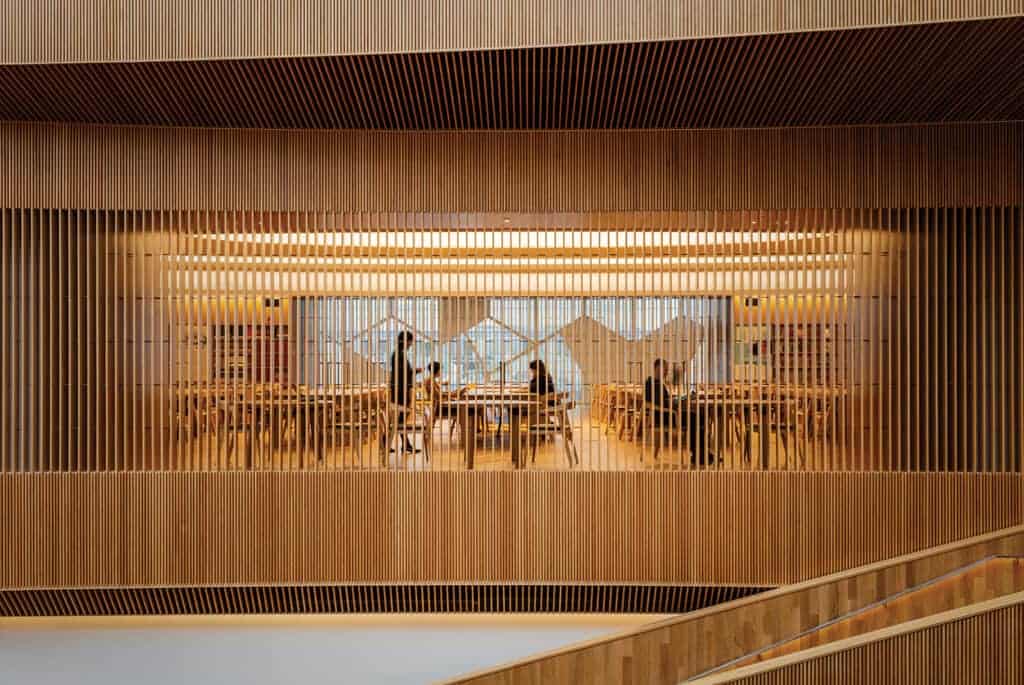
In addition to their appearance, the design and geometry of the wood panels played an important role in delivery on the acoustical properties of this “quiet” facility.
Some distribution centers offer light manufacturing to better support the needs of local businesses. Light manufacturing takes several different forms at HDI: with Paxton it is an extensive moulding program, Rugby is more diversified with moulding manufacturing, be it MDF, Softwood or hardwood lumber; fabrication of custom HPL countertops, cut or rip to size lumber, and door fabrication where doors from major manufacturers are custom hung in the frame.
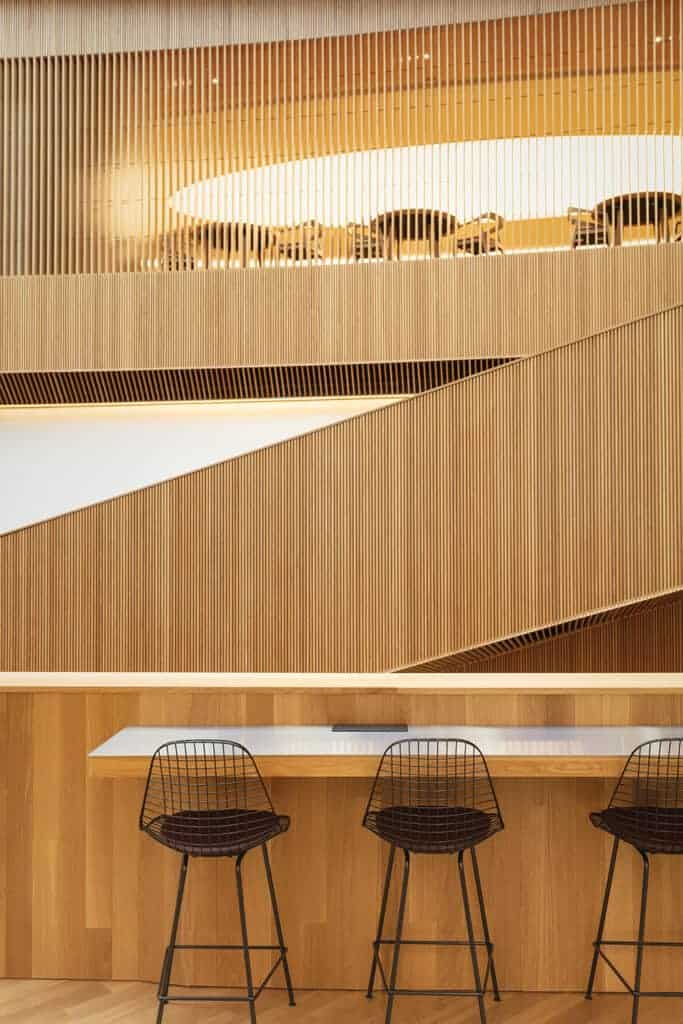
This is no ordinary Hemlock lumber. It was first selected for its appearance: it was required to be FSC certified, come from within 500 miles for local content, be Class “A” Fire Rated, and have an environmentally approved UV resistant clear coating. It was critical that the lumber was perfect in both appearance and in its physical properties.
HDI distribution facilities offer exceptionally fast and efficient will-call service, commented HDI’s Director of Marketing, Gord Clough. These areas are set up to provide will-call customers with an expedited buying experience. Specially trained willcall staff assists customers with product selection; technical information and fast order processing to get them back to their shop or job site as fast as possible. Clough added that one of the most notable improvements and areas of specialization is the new Rugby 33,000-square-foot will-call facility set within the expansive new 125,000-square-foot Rugby facility in the Dallas – Fort Worth, TX market.
Clough explained, “As North America’s largest distributor in our industry, with an unmatched network of locations and annual sales of over $1.1 billion, we are focused on leveraging our size, capabilities, and strong financial position to provide customers with convenient and local access to a world-class assortment of products.
“Sustainability plays a large role in our industry today,” said Clough. HDI and all of its companies are compliant and only source from sustainably managed lands. Its global sourcing programs are executed by the HDI Import Division and HDI Import Lumber Division that collectively procures the highest quality lumber and panel products from around the globe making them readily available to the North American market.
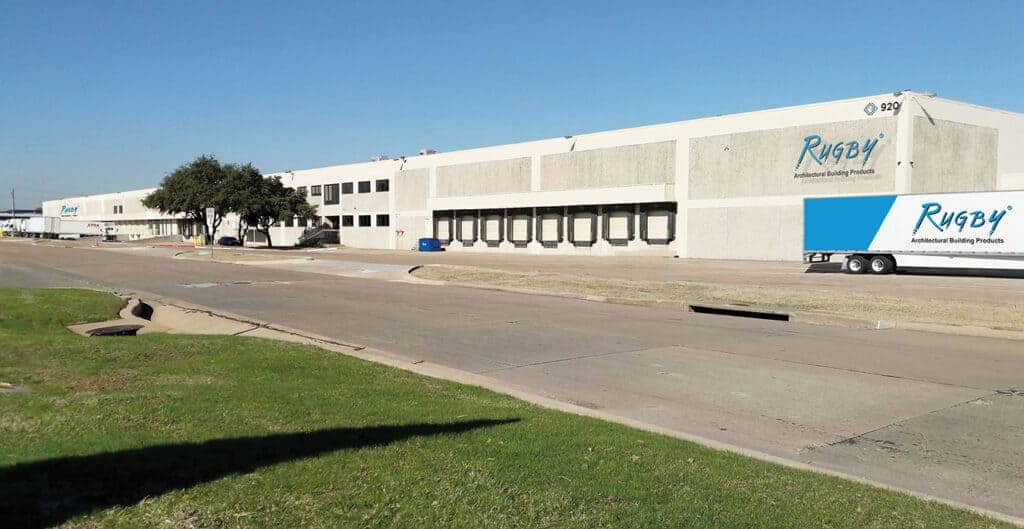
New Rugby Architectural Building Products distribution center features a 33,000-square-foot will-call facility within the expansive 125,000-square-foot Dallas facility.
Vendors are approved through a rigorous audit process to ensure that they conform to HDI’s quality standards as well as supply chain compliance with TSCA Title VI for emissions, and Lacey Act requirements for legal fiber. Factories meeting ISO 14001 and 9001 standards ensure the highest level of compliance and control. Internal production control is exercised by HDI as they oversee raw material specifications, production parameters and finished product quality standards to meet North America’s most demanding requirements.
“HDI is uncompromising in its commitment to be the preferred choice for its valued customers, the best partner for its vendors, and a great place to work for its valued employees,” added Clough. Core to its philosophy is the protection of the environment, and the goal to provide the North American market with products of exceptional value. This, in addition to its focus on the well being of its customers and employees, has allowed HDI to emerge as a powerhouse in the industry and to successfully operate in North America for over 50 years.
For more information visit www.hdidist.com.