By Michael Culbreth
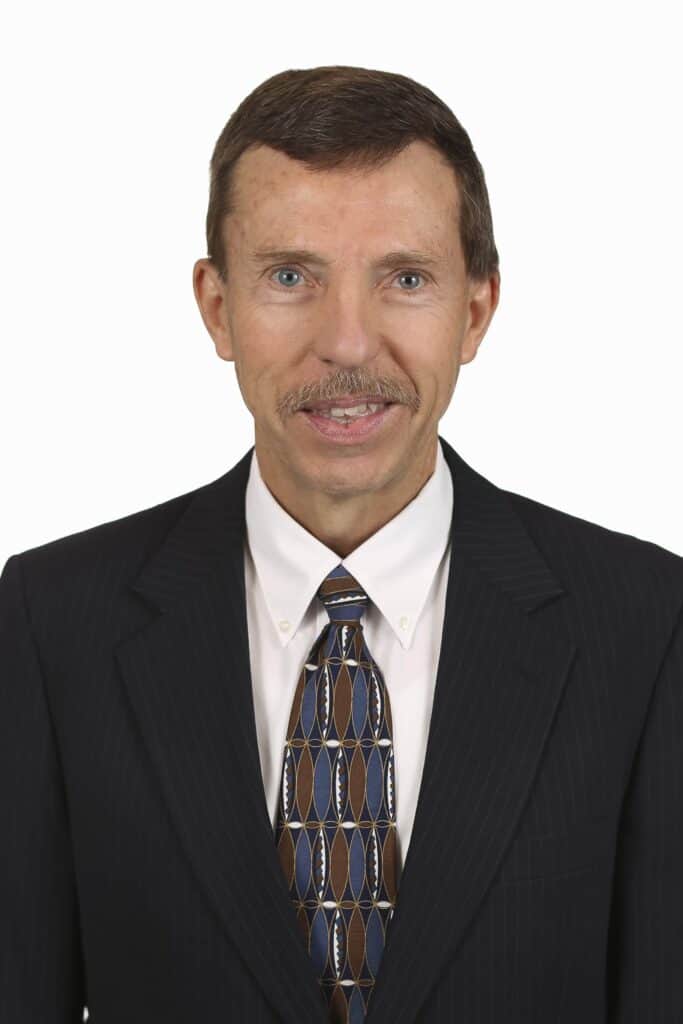
PLM
Almost every Hardwood business understands the importance of safety. Yet a company’s risk profile changes constantly, and it’s difficult for many business leaders to keep up with all the latest developments. One way to stay ever ready is to embrace a culture of safety.
Let’s examine the core business risks impacting Hardwood suppliers and dealers today and explore how a safety-first mindset can help you address those risks effectively.
How risks have evolved
Over the past 12 months, we’ve seen significant changes across four of the most common risks: commercial auto, cybersecurity, weather and fire.
In commercial auto, losses keep trending upward. This is creating a phenomenon known as “social inflation,” where the increase in claims cost is outpacing inflation across the general economy. Rearend accidents often lead to the most expensive commercial auto claims. Distracted driving is one potential cause for these types of crashes.
Hardwood businesses with delivery operations are at major risk. These fleets often include heavy and extra-heavy vehicles that must share crowded urban roadways with multiple vehicles. Another contributing factor is the ongoing shortage of well-qualified drivers, which sometimes leads companies to lower their standards during the hiring and screening process.
While commercial auto risks keep rising, so too do cybersecurity-related exposures. We live in a digital world, and today, data breaches and ransomware attacks impact companies of all sizes. Hardwood businesses must continue to bolster their data security postures or run the risk of serious financial and reputational damage.
When it comes to weather-related losses, we’re seeing an interesting pivot. Claims activity rose dramatically in 2023, but the root cause of those claims was different. In most years, property damage from catastrophic storms like tornadoes and hurricanes made up the bulk of wind and weather losses. In 2023, roof damage ranked as the top claim, driven mostly by more powerful thunderstorms and straight-line winds.
Amid all these emerging risks, there was encouraging news: major fire losses were down in 2023, according to data from Pennsylvania Lumbermens Mutual Insurance Company (PLM). However, this is one area where companies can never let their guard down, because it takes just one fire to devastate a Hardwood business.
Why having a culture of safety matters
A culture of safety can help companies reduce their loss frequency dramatically. Take, for example, a company with a high incidence of commercial auto-related claims. It may choose to reverse the trend by investing in safety-related technology, such as installing telematics and video cameras on their vehicles. The company can then capture data, use it to inform safety training sessions, and reduce their losses substantially.
Five building blocks of an effective safety culture
Creating a culture of safety that addresses the top Hardwood-related risks doesn’t have to be complicated. Five best practices to follow are:
1. Start at the top. Everyone from the CEO on down must embrace a culture of safety. Having management buy-in will create a ripple effect throughout the entire business.
2. Commit to ongoing safety training. Establish and fully implement written safety policies with the support of management. You should offer safety training to new hires and host refreshers at least annually. Implement in-the-moment training after any incident.
3. Show genuine concern for your employees. Let them know that your goal is for them to return home in the same condition – safe and healthy –as they arrived.
4. Recognize safe performance. While a formal incentive program is value-added, you should also give your employees affirmation for doing their job safely. A simple word of thanks can go a long way.
5. Develop a tight relationship with your carriers. Seek insurers who understand the Hardwood niche. They can help you design a program that best mitigates your risk. The right carrier will offer you property and casualty coverage, and also help you identify other coverages, such as cybersecurity or employment practices liability, that could benefit your company.
What to include in your risk mitigation plan
As you build out your culture of safety, consider taking these steps to reduce some of the most frequent causes of losses.
- Step up your fleet safety. Create a fleet safety program that addresses driver training, hiring and screening. At minimum, review motor vehicle reports before hiring any candidate. Consider adding telematics and cameras to your vehicles. This has quickly emerged as the gold standard approach because it empowers companies to address risky driving behaviors before an accident occurs.
- Fortify your facilities. Protect yourself from wind damage with proper roof maintenance. If you’re not sure of your roof’s current condition, perform an inspection. Use aerial photography to identify emerging issues. Then compare those photos with a walk-through inspection. Look for signs of water intrusion or damage in potential trouble spots.
- Enhance your fire protection. Test and maintain all fire protection systems, including smoke or heat alarms, automatic sprinkler systems and fire pumps. Implement a hot work permit program for welding fire safety. Sawmill and pallet manufacturers should consider using infrared thermography to scan electrical panels for potential hot spots.
- Test your network safety. Work with IT professionals and put appropriate cybersecurity safeguards in place. Consider running phishing simulations that give your employees a score based on how accurately they identify potentially harmful emails.
- Reduce your general liability-related risks. Keep aisles of retail locations clear and clean. Make sure storage racks are secured properly. Institute forklift safety programs that address optimal loading and unloading procedures. Make sure employees wear personal protective safety equipment. If your business contracts with installers, institute proven risk-transfer controls.
As weather-related risks grow and digital networks become more complicated, the risk profiles of Hardwood businesses will continue to evolve. By taking a top-down approach to risk management, you can make safety an ongoing part of everyone’s job, improve your loss profile, and help keep your workers happy and healthy.
The author
Michael Culbreth is a loss control consultant with Pennsylvania Lumbermens Mutual Insurance Group (PLM). PLM is the nation’s oldest and largest mutual insurance company dedicated to the wood products, lumber and building materials industry.
To learn more about Pennsylvania Lumbermens Mutual Insurance Group, visit www.plmins.com.