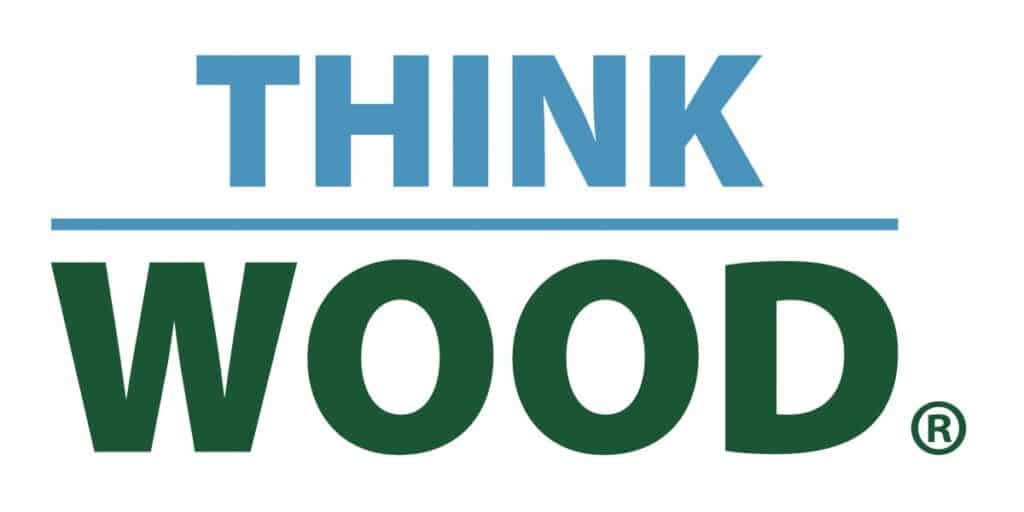
Climate change demands dramatic shifts in how we design and construct our buildings. At the same time, the urgent need for housing and supportive infrastructure continues to surge at record rates. One important part of the solution? Convert the built environment from a carbon source to a carbon sink.
The Urgent Need to Lower Building Carbon Footprints
The built environment is growing at a record pace in the United States. It is estimated that 2.5 million new housing units are needed to make up for the nation’s housing shortage.1 Buildings and their construction account for 39% of global carbon dioxide emissions; 28% of those emissions come from operational carbon — the energy used to power, heat and cool a building.2 Buildings’ operational carbon can be reduced through energy efficiency measures and policymakers, architects, developers, and engineers have made significant advances in this arena. The remaining 11% of carbon emissions are generated from building materials and construction.3 This “embodied carbon” can account for half of the total carbon footprint over the lifetime of the building.4 To reduce the GHG emissions associated with construction, specifiers and stakeholders need to act now to create embodied carbon strategies that reduce environmental impacts from buildings we’ll use well into the future. The costs of delaying any longer are too high. Greenhouse gas emissions have increased by 90% since 1970.5 A 1.5% increase in global warming will have catastrophic results for ecosystems and people around the world, including the United States.6
Embodied carbon is a priority for many environmental, architecture, and urban planning organizations including C40 Cities, Architecture 2030, Urban Land Institute, and the World Green Building Council. Many experts believe addressing embodied carbon for buildings and building materials is critical to achieve the goals of the Intergovernmental Panel on Climate Change (IPCC) and the 2016 Paris Climate Agreement.
Embodied carbon is determined by conducting a life cycle assessment (LCA) of a product, assembly or the building over declared life cycle stages. An LCA study returns results for a number of environmental metrics, including the potential to impact climate or “global warming potential” (GWP). Embodied carbon is the GWP result. Embodied carbon is measured for each stage of the product’s life cycle, allowing comparisons across any combination of stages.
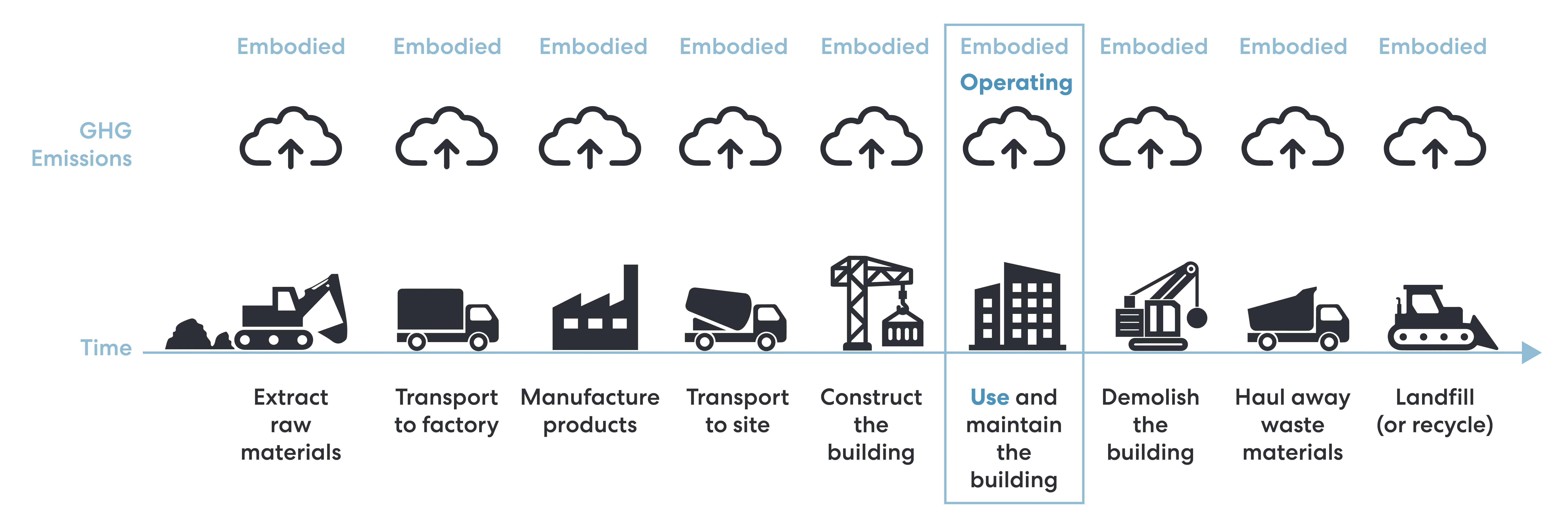
Very soon, embodied carbon is likely to become the dominant source of building emissions. Embodied carbon varies dramatically between concrete, steel and wood, making product decisions key in achieving lower carbon buildings. Manufacturing wood products requires less total energy, and in particular less fossil energy, than manufacturing most alternative materials including metals, concrete, or bricks. 7
Design professionals across the country and around the world are increasingly constructing buildings using light-frame and mass timber structures in a commitment to combat climate change. Not only does wood continue to store carbon, its insulative thermal properties lend well to energy efficient solutions like Passive House. A Boston-based CLT Passive House Demonstration Project is a mass timber, mid-rise, multifamily, and certified Passive House building that shows how cross-laminated timber systems can meet complex design and sustainability goals. It’s the brainchild of MIT start-up Generate and design-build firm Placetailor. “Mass timber buildings, like Model-C, have the ability to tackle climate change [and] are also mid-rise to accommodate urban density,” says Generate CEO, John Klein. The five-story mixed-use demonstration project is Boston’s first full cross-laminated timber (CLT) building, housing fourteen residential units and a ground floor coworking space. The project was designed to operate at net-zero carbon, which is achieved by calculating both the building’s embodied energy and its operational energy, and offsetting any annual excess energy use through carbon offset purchases. The building is Passive House certified and meets the Boston Department of Neighborhood Development’s Zero Emission Standards . It is scheduled to begin construction in spring 2021.
Carbon Conclusions: Future Outlook
Cutting carbon emissions and finding advanced ways to store carbon in our buildings requires a full court press by the architecture, engineering and construction sector. And industry leaders are stepping up with substantial commitments —from conducting leading research on carbon and climate to erecting important demonstration projects.
Footnotes:
1 – http://www.freddiemac.com/research/insight/20181205_major_challenge_to_u.s._housing_supply.page?
2 – New report: the building and construction sector can reach net zero carbon emissions by 2050, World Green Building Council – https://www.worldgbc.org/news-media/WorldGBC-embodied-carbon-report-published
3 – https://www.worldgbc.org/sites/default/files/UNEP%20188_GABC_en%20%28web%29.pdf
5 – https://www.epa.gov/ghgemissions/global-greenhouse-gas-emissions-data
7 – https://www.canfor.com/docswhy-wood/tr19-complete-pub-web.pdf, pg. 3